Zirconium alloys in nuclear reactors
A patented method for loading zirconium alloys with hydrogen to test components used in nuclear reactors.
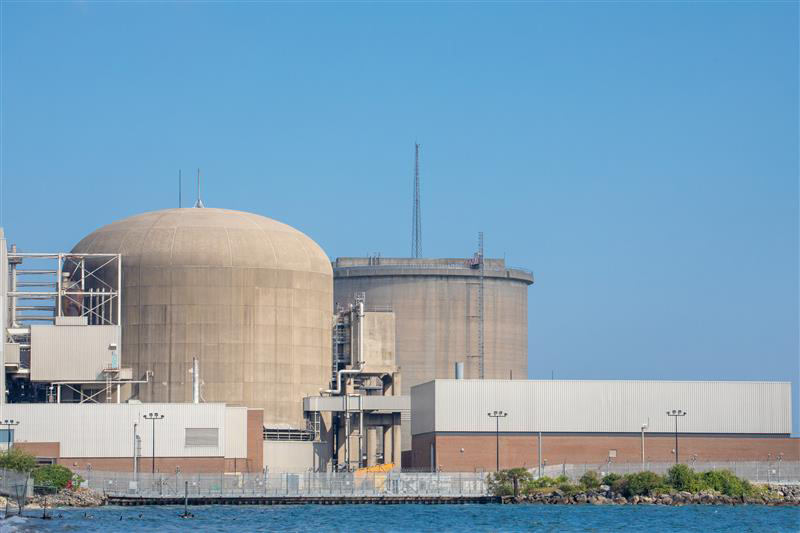
One of generating units at the Ontario Power Generation Pickering Nuclear electric power plant on the shore of Lake Ontario near Toronto, Canada. It is one of the oldest nuclear power stations in the world and Canada's third-largest, with eight CANada Deuterium Uranium reactors
© sockagphoto / ShutterstockNuclear reactor components often withstand a wide range of challenging conditions, including exposure to ionising radiation, high temperatures and corrosive environments. The materials used depend on the type of reactor and the specific component function, but many facilities use zirconium alloy components.
Zirconium alloys are commonly used because of their low-capture cross-section for thermal neutrons, combined with good mechanical properties and strong corrosion resistance. Indeed, resistance to corrosion makes zirconium particularly suitable for use in water reactors, including pressurised water reactors (PWRs) and heavy-water reactors like the CANada Deuterium Uranium (CANDU) reactor.
However, zirconium is not immune to environmental effects and its fracture toughness can be reduced with long exposure to hydrogen and neutron irradiation. A phenomenon known as delayed hydride cracking (DHC) has been observed in zirconium alloys exposed to hydrogen concentrations exceeding critical levels.
DHC appears to be a sub-critical mechanism for crack-growth, in which brittle hydride phases are formed at the crack’s tip, followed by failure of the hydride and further crack extension until the zirconium matrix is reached. This can eventually lead to failure of zirconium alloy components.
Accordingly, there is a need to assess the risk of future DHC-related failure. For example, reactor pressure tubes can be removed from service, loaded with hydrogen until typical end-of-life concentrations are reached, and then subjected to burst testing.
This type of testing requires hydrogen to be added to the material in a way that preserves any changes to the zirconium alloy microstructure (such as defect cluster formation) and mechanical properties caused by in-service radiation damage, since this can also contribute to the DHC phenomenon.
So far, hydrogen has been added during testing of zirconium components using three main techniques – electrolytic hydriding, gaseous hydrogen addition and aqueous lithium hydroxide corrosion. However, all three techniques suffer from disadvantages.
For instance, electrolytic hydriding requires large volumes of corrosive sulphuric acid that must be contained in a hot cell. This method is also time-consuming and expensive and can lead to uneven hydrogen uptake.
Gaseous hydrogen addition typically requires large volumes of high-temperature, high-pressure hydrogen gas, which is a potential fire and explosion hazard. Alternatively, gaseous hydrogen addition can be achieved using highly specialised equipment, which must be constantly adjusted and calibrated if carried out at atmospheric pressure.
Hydrogen addition by aqueous lithium hydroxide corrosion can also lead to unwanted lithium ingress, uneven hydrogen uptake and uncertainties in the metal’s final hydrogen concentration.
Atomic Energy of Canada Limited has recently been granted European patent EP363882B1, which describes an alternative method of adding hydrogen to metal alloys.
The patent claims protection for mechanically assisted gaseous addition of hydrogen to metal alloys.
The method comprises an article formed of the metal alloy; a metal hydride; a shell metal covering at least a portion of the article and the metal hydride to form an assembly; applying load to the assembly; and heating the assembly, wherein the shell metal deforms around the portion of the article and the metal hydride and forms a gas-proof seal.
Here, the metal hydride thermally decomposes to form hydrogen gas, at least a portion of the hydrogen gas dissociates and moves as monoatomic hydrogen into the article.
The patent also claims protection for an associated assembly, including an article formed of the metal alloy; a powder formed of a metal hydride; and a shell metal covering at least a portion of the article and the powder, wherein the shell metal forms a gas-proof seal around them.
According to the patent, the method enables quantitative homogenous addition of hydrogen to the article at relatively low temperatures and in a short time frame, preserving any existing irradiation damage that can be lost at elevated temperatures.
In particular, the mechanically assisted technique uses external pressure to drive hydrogen concentrations beyond the solubility limit at a given temperature.
Such methods have been found to enable precise control of the amount of hydrogen added to a metal, as this can be determined accurately using a standard analytical balance. In fact, the patent includes experimental results indicating that observed hydrogen concentrations – determined using differential scanning calorimetry – show good correlation with those predicted by mass-balance equations.
The technique also eliminates, or substantially reduces, the explosion risk traditionally associated with gaseous hydrogen addition, by reducing the amount of hydrogen to the desired concentrations in the sample, while maintaining the ability to add any combination of protium and/or deuterium gas and avoiding the use of corrosive liquids.