‘ZeroCAL’ takes concrete steps to decarbonise cement
Calcium hydroxide – a zero-carbon precursor for lime and, subsequently, cement – is being billed as the solution to decarbonise cement production.
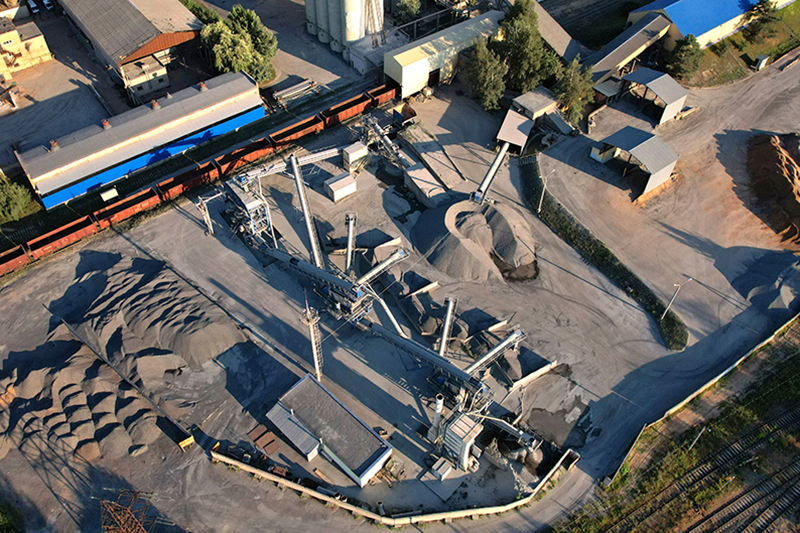
Cement plant and ready mix concrete site
© Maksim Safaniuk/ShutterstockThe thermochemical decomposition of limestone to produce lime, or calcium oxide – the primary precursor for cement production – currently accounts for about 60% of the CO2 released during manufacturing.
Researchers at UCLA in the US report to have developed a scalable process using hydrated lime (Ca(OH)2) – produced from calcium hydroxide – which only emits water when it is heated.
They first produce calcium hydroxide using limestone feedstock, which emits no CO2 when burned to make lime for cement.
The hydrated lime can subsequently be directly integrated into the existing cement production process, and its use could reportedly remove 98% of CO2 emissions associated with the thermochemical process of manufacturing lime.
The team, led by Gaurav Sant, Director of UCLA’s Institute for Carbon Management, first uses ethylenediaminetetraacetic acid – a common industrial water-softening chelator – to convert limestone (CaCO3) into calcium chloride in a table salt solution that comprises sodium chloride and water, trapping the carbonate in the aqueous phase.
Next, membrane nanofiltration separates the calcium derived from the limestone. As Sant explains, the calcium chloride is then converted to Ca(OH)2 in an electrolyser where the cathode reaction provides the alkalinity required.
Although the 'follow-on calcination of Ca(OH)2 to produce lime is very similar to the calcination of CaCO3', he says, the Ca(OH)2 calcination not only requires less energy, but also only releases water vapour during calcination.
Also, the ZeroCAL process has significant co-products, including oxygen and hydrogen gas, which could become clean-burning fuels for the cement kiln, he adds, while the Ca(OH)2 can also be used for direct air capture of CO2.
Sant expands, 'Others have considered the use of hydrated lime as a cement precursor…what makes the ZeroCAL process unique is that it provides a means to produce hydrated lime using limestone without emitting CO2.
'It [also] enables onsite decarbonisation, while making use of existing kilns and limestone feedstocks, without having to build separate carbon capture and storage facilities.'
Sant admits the approach requires more energy than other lime-production methods, and so the team is undertaking work to see how it can achieve energy-use parity.
They are exploring how to simplify and eliminate unit operations to achieve better integration. Second, they want to make better use of the electrolytically produced acid and base co-products.
'Based on bench-scale data and process models, we are currently on track to significantly improve the process energy demands and achieve reductions of more than 30% per unit of lime,' he says.
To meet ZeroCAL’s water demand, the team suggests focusing on cement plants near coasts or rivers, or facilities with ready access to water supplies.
They are collaborating with Ultratech Cement Limited to build a demonstration plant in India that will produce several tonnes of Ca(OH)2 per day.
This will validate operations using commercially relevant equipment, alongside an operating cement plant, to demonstrate economic viability, compatibility with existing industrial infrastructure, and the ability to use quarried limestone as technical feedstocks.
ZeroCAL’s developers are also exploring how the same process could work in steel production, which relies on limestone-derived fluxing agents that generate CO2 emissions.