What lies beneath - new phosphate mining industry in Norway
In a remote area of southern Norway, large deposits of a precious rock hide beneath the surface.
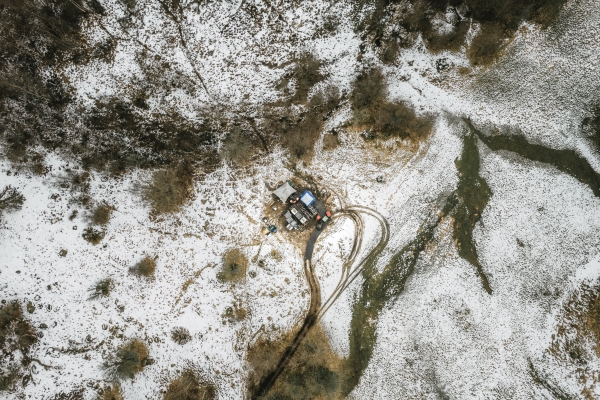
Exploration drilling for extracting core samples in the Skeipstad deposit and mineral resource estimate area, Eigersund Municipality.
In the Bjerkreim lobe of the Bjerkreim-Sokndal layered intrusion, Norway
Tessa Parry-Wingfield, writer for Norge Mining, sheds light on plans to extract the ‘white gold’ phosphate rock that is integral to both global food security and the green energy transition.
Phosphorus, which derives from phosphate rock (P2O5), is a finite resource. While P2O5 is a vital ingredient in fertilisers that help crops grow, significant deposits of phosphate rocks have previously only been found in a select few countries – China, Morocco, Western Sahara and Algeria.
With huge amounts of P2O5 fertiliser sold around the world every year, scientists warn we are reaching ‘peak phosphate’. If that rings true, an urgent conundrum looms – how to feed the eight billion people on Earth and counting (rapidly) without it? It is no surprise therefore that phosphorus and phosphate rock are listed on the EU Critical Raw Materials (CRM) list.
Michael Wurmser, Founder of Anglo-Norwegian exploration firm Norge Mining, elaborates, 'Phosphate security equals food security and is emerging as a vital global sustainability challenge.
'Supply strategies to ensure farmers have sufficient access to phosphates to feed the world are therefore becoming increasingly urgent given the ongoing invasion of Ukraine by Russia – a major exporter of phosphate – putting in jeopardy the security of supply from this region. Phosphate…could become a key player in trade leverage.'
Enter Norway
Cue one of the world’s largest resources of phosphate (alongside vanadium and titanium) in Europe at the Bjerkreim Exploration Project in southern Norway, for which Norge Mining has exploration rights.
At approximately 70Bt of igneous phosphate rock deposits, the potential mine in Europe’s ‘backyard’ intends to set high standards for stakeholder engagement, carbon management and reuse of remaining resources.
Norge Mineraler AS’ Project Director, Jørgen Stenvold, says, 'I’ve only seen one deposit with phosphate quality similar to Norge Mining’s and that’s in the Kola Peninsula in Russia. Europe needs this and we must protect the strategic value of this phosphate in the best way possible.'
Ingvil Smines Tybring-Gjedde, Non-Executive Director of Norge Mining and the former Norwegian Minister of the Interior, adds, 'I see Norway’s vast experience in natural resources and existing regulatory framework – with the environment always at the forefront – as a fantastic foundation on which to build a new mining industry – one that will provide EU CRMs to the world.'
The pressure is now on to create a domestic supply of these critical minerals as Norge Mining and its operations arm Norge Mineraler AS advances through the exploration process towards mine construction and operation, in a new era of responsible, sustainable mining.
Giving the deposits even greater international significance, is the fact this ‘white gold’ has another increasingly significant use – in lithium iron phosphate (LFP) batteries for electric vehicles (EVs). Tesla, Toyota, Hyundai, Ford are all adopters. Safety, longer-cycle length and greater cost effectiveness are all reasons for the LFP battery’s popularity.
Provenance is pertinent
However, aside from greater demand, the environmental sustainability and provenance of components is also an important factor for car manufacturers – and their customers.
Other popular battery components – nickel and cobalt for example – are dubbed ‘dirty metals’ and come laden with the burden of environmental and social concerns, in an era where palatable provenance is increasingly becoming an environmental, social and governance (ESG) prerequisite.
In the past, mines have been developed in ‘someone else’s back yard’ – generally, in commodity-dependent developing countries that gain little or no economic benefit from natural resources, while suffering low standards of worker and environmental protections.
As John Vergopoulos, CEO of Norge Mining, explains, 'Mineral resources are at the very beginning of supply chains, so if they are not fully compliant in terms of social responsibility and environmental factors – including the quantification of carbon emissions – then the entire supply chain is impacted.
'During the past six years, the strategic and geopolitical context of our business, and our focus on the EU CRMs phosphate, vanadium and titanium, has magnified in importance much faster than we had envisaged, adding to the momentum in the company and the urgency in terms of potential demand for our minerals.'
ESG concerns, regulation and other powerful drivers are shaping our future when it comes to the products we want and the materials we need to create them.
Geopolitical instability has exposed the fragility of long supply chains, where Europe is dependent on far-flung places for materials desperately needed for the resilience of their economies – now and in the future. This is the very reason the EU created its CRM list in the first place – to highlight how crucial they are, combined with the risk associated with their supply.
A diversified, secure and stable supply of minerals within the western marketplace is needed – reducing reliance on vulnerable chains and bringing them closer to home.
Not all phosphate is created equal
The phosphate deposits Norge Mining intends to extract in Norway are free of cadmium. This is important – the quality of phosphate varies hugely, depending on its source.
'Roughly 80% of extracted phosphate comes from sedimentary sources that suffer from higher contamination levels,' explains Dr Jana Plananska, an independent consultant in electric mobility and battery technology, and Advisory Board member at Norge Mining. 'The quality of this is lower than the pure magmatic resources found beneath Norway’s surface. This means there is a lot of hard graft at the processing stage midstream. It needs to be treated with more laborious procedures to get to the purity that’s needed for high-end applications, such as batteries. This incurs higher energy costs and greater manpower.'
Vertical thinking
What’s more, there is currently no facility in the West processing elemental phosphorus. This is a key precursor within the chemical industry for high-end applications within electronics (such as for semiconductors and microchips), the energy storage sector and for solar panels. There is an urgent need, therefore, to increase extraction of phosphate from igneous formations and develop a phosphorus processing capacity inside Europe.
The pandemic and geopolitical instability have forced a rethink, but one that should create value chains that are less susceptible to vulnerabilities.
The whole concept of ‘just-in-time’ global trade is being turned on its head wherever possible – with companies, manufacturers and governments all starting to think more vertically.
Oliver Baring, Chair of Norge Mining, expands, 'During the course of our market analysis, we expanded the scope of our potential activities to include downstream processing in addition to mining, as we see an opportunity to enhance our value proposition for customers while maximising value for the company through refining our raw materials into products. This evaluation of downstream activities, including the negative carbon production of phosphorous from phosphate, is ongoing.'
It’s no coincidence, therefore, that the European Raw Materials Alliance has recently supported Norge Mining in securing finances for responsible sourcing of CRMs in Norway, to secure greater EU autonomy.
The power of three
Importantly, the Norge Mining deposits also contain vanadium and titanium – the former is also on the EU CRM list, while titanium has been classified as a ‘Strategic Raw Material’.
Vanadium’s potential lies in efficient power storage. Vanadium-based redox flow batteries (VRFB) have a long lifecycle of decades, retaining value through thousands of recharges. Vanadium may also have a role to play in the EV revolution as research continues into creating rechargeable batteries with a longer range.
Did you know?
The need for mined vanadium for commercial use has received a boost thanks to the American Bureau of Shipping. It has issued a new technology qualification for vanadium-based redox flow batteries in the maritime industry.
However, currently, 75% of global vanadium supply is sourced from China, South Africa and Russia. As steel production accounts for most of the vanadium consumption – and with China increasing its enforcement of new high-strength rebar standards – the need for vanadium in construction is still high. With vanadium demand continuing to grow for energy storage as well, Norway is perfectly poised to become a supply centre in the future.
Titanium, meanwhile, is a relative newcomer to the EU CRM and Strategic list – joining in 2020 due to a shift of criticality scores both for economic importance and supply risk. Titanium metal’s extraordinary strength and light weight make it a key ingredient in aeronautics, space and defence manufacturing.
It is also widely used in the pigment industry. Finely ground titanium dioxide is a bright white powder and a component in base pigment for paint, paper and plastics, where a supply shortage is forecast over the coming years.
China has been the major supplier and makes up almost half of the global annual production. Going forward, titanium feedstock demand will require additional global supply and further import requirements for Europe.
Sustainable sourcing
A world-class resource is under Norway’s surface. The urgent need and clamouring demand are palpable across Europe – and the wider world. Now comes important decisions about how to create a sustainable mine that sources as responsibly as possible – setting industry standards and innovative approaches that respect the land and its people. More than that, the creation of long-term local employment and building local supply capacity, along with broader economic benefits, are integral to the plans.
In the words of Olav Skalmeraas, Norge Mineraler’s Managing Director, 'Will our strategies of today still be perceived as responsible in 2040? Sustainability is not about the now. It’s also about the future. How things have been done in mining before, is not how it will be done now and in the future.'
"Next-generation mine”
ABB is collaborating with Norge Mining to conduct a Front-End Engineering and Design study for future Norwegian mine production.ABB will be using their eMine approach for the electrification of mining and downstream operations including control system options.
The ABB study will address electrification, automation and digitalisation to ensure maximum sustainability, cost-efficiency and productivity at the mine from the outset and for the long term. ABB’s recommendations will also focus on low-energy consumption within mine operations as well as optimising CAPEX and lowering OPEX with solutions for lower maintenance and higher efficiency.
Additionally, they are exploring the circularity options for tailings, the potential generation of hydrogen by-products from processing facilities, and the implementation of carbon capture and storage.