Using graphene flakes for industrial surfactants
New research demonstrates that graphene flakes can be used as a surfactant with amphiphilic properties. Shardell Joseph finds out how.
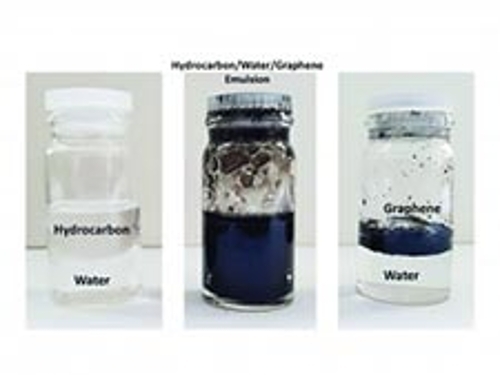
From oil extraction to paper processing, researchers at Cranfield University, UK, are discovering how graphene can act as a versatile 2D stabiliser for many different industrial applications. As the material attracts water at its edges and repels it on the surface, it can act as a surfactant with potential for stabilising oil and water mixtures.
The researchers found that even though pristine graphene is completely water repellent, at below one-micron lateral size, amphiphilic behaviour is possible.
‘Its stability is superior to traditional surfactants, both in terms of temperature and pressure,’ says Professor Krzysztof Koziol, Head of the Enhanced Composites and Structures Centre at the University.
‘We produced pristine graphene flakes, without application of any surface treatment, at a specific size which can stabilise water/oil emulsions even under high pressure and high temperature.’
Traditional surfactants tend to experience issues around 100°C but there are high-temperature surfactants available, continuously at 180°C or even to 240°C. ‘In our case, it is a completely different story, graphene will not evaporate until above 3,000°C,’ says Koziol. ‘However, in the presence of oxygen it will degrade at about 550°C. We have done successful stable trials at 400°C which is really an exciting new level of performance.’
Koziol explains that by decreasing the flake size, they are increasing the proportion of the edges of the material to the basal plane surface. ‘This behaviour becomes quite obvious as one goes much below
one-micron in flake diameter. This particularly enhances the flake solvent interaction and the amphipathic behaviour.
‘The amphipathic nature which we observed is coming from the basal plane surface, hydrophobic behaviour, and edges, hydrophilic behaviour. The oil will interact with the basal plane of the flake while water molecules will interact with the edges of the flake,’ he adds.
Graphene is a resistant material, which unlike traditional surfactants, can be stored as a solid powder for a long time without degradation or corrosion. In addition, the material can be filtered much easier than traditional surfactants, allowing it to be reused.
‘Finally, to make these flakes, only biogas [biomethane] is used as the raw material without any need for a catalyst,’ says Koziol. ‘One can consider that we are locking methane to produce this type of surfactant, creating a very sustainable manufacturing background.
‘It was possible to achieve the required interaction without many challenges. Furthermore, the stability of the mixture can be optimised by varying the amount of graphene presence.’
Overall, the researchers claim graphene offers a more stable, cost-effective and environmentally friendly way to operate in harsh geological or chemical environments.
The researchers have explored its suitability in only one environment so far – transportation and extraction in the industrial water environment – which involved a hydrocarbon, in this case decane.
But they believe the graphene flakes can meet the demand for better quality surfactants as plasticisers for fluid concrete, additives in flameproofing and waterproofing, as well as lubricants in drilling fluids. This can improve industrial processes including metal processing, pulp and paper processing, mining, leather processing, crude oil production, fibres and textile processing, plastics production, paints and coatings, construction and petroleum products.
The team will continue to analyse the material by developing a testing programme across the various fields where surfactant use is critical. In addition, they will explore selectivity of the graphene surfactant with further control over the flake size.