Turning corrosion science on its head
Researchers in Germany claim to have harmonised alloying with dealloying.
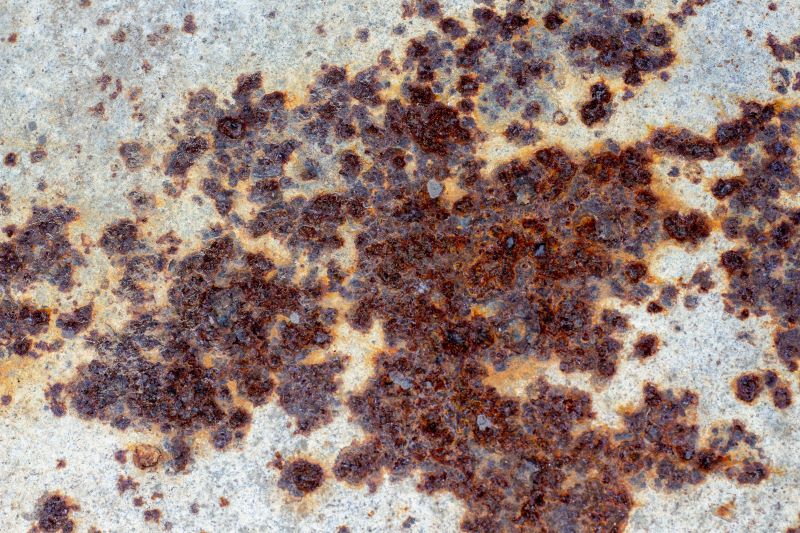
They have reportedly transformed these counteracting processes to create lightweight, nanostructured, porous, martensitic alloys that are said to reduce carbon emissions and save energy.
Traditional dealloying naturally removes atoms from the lattice, causing degradation. But the research team at the Max Planck Institute for Sustainable Materials (MPI-SusMat) asked, 'What if we could harness dealloying to create beneficial microstructures?'
The team’s approach integrates four metallurgical processes into a single reactor step:
- Oxide dealloying – removing oxygen from the lattice to create excessive porosity while simultaneously reducing the metal ores with hydrogen.
- Substitutional alloying – encouraging solid-state interdiffusion between metallic elements upon or after complete oxygen removal.
- Interstitial alloying – introducing nitrogen from the vapour phase into the host lattice of the gained metals.
- Phase transformation – activating thermally induced martensitic transformation for nano-structuring.
Dr Shaolou Wei of MPI-SusMat explains, 'We have conceived to do this in a reactive vapour atmosphere, which allows for active alloying element exchange between the solid and the vapour phase.'
The atmosphere consists of ammonia, which acts as both a reductant (via its hydrogen content) – selectively extracting oxygen from the host lattice – and acts as a donor of interstitial nitrogen, filling vacant lattice spaces to enhance material properties.
'This dual role of ammonia – removing oxygen and adding nitrogen – is a key innovation in our approach, since it assigns all atoms from both reaction partners specific roles,' says Professor Dierk Raabe, Managing Director of MPI-SusMat.
Wei continues, 'Lightweighting and high-porosity content are naturally achieved as the redox process facilitates the formation of oxygen vacancy, which can agglomerate and lead to the formation of pores.'
Modulating porosity was achieved by 'controlling [ammonia’s] partial pressure, or the maximum temperature achieved. Though we have not yet carried out a systematic parametric study for porosity modulation.'
He shares, 'Nano-structuring was achieved through a martensitic transformation rooted in our composition design in the Fe-Ni-N [iron-nickel-nitrogen] system.'
'The mass density of our Fe-Ni-N martensitic alloy is only 5.69g/cm3, roughly 70% of the bulk counterpart with the same composition. It reaches a specific Vickers hardness (i.e. hardness divided by mass density) value of 36.9 when tested under 100g load, which is about 1.5 times that of the fully dense alloy.'
This is as a result of precise microstructure control from the millimetre to the atomic scale.
The team explains that usually achieving such porosity requires time and energy-intensive processes. In contrast, the new strategy accelerates porosity formation while allowing simultaneous introduction of interstitial elements that enhance material strength and functionality.
The energy-saving claim comes from its operation at a temperature of 700oC, far below the bulk melting point.
While the use of hydrogen as a reductant agent and energy carrier instead of carbon, means the dealloying-alloying process is CO2-free and the only by-product is water.
Thermodynamic modelling demonstrates the feasibility of this technique for metals like iron, nickel, cobalt and copper.
They hope to extend the approach to use impure industrial oxides and alternative reactive gases.
Wei believe this could reform alloy production by reducing reliance on rare-earth materials and high-purity feedstocks, so aligning with global sustainability goals.