The persistent polymer problem – tyre and road wear particles
Tyre and road wear particles are pervasive and reaching global waters. Sarah Morgan explores the scale of the issue and innovation to tackle it that is on the horizon.

In the UK alone, there were 40.8 million licensed vehicles at the end of September 2022, a 0.7% increase compared to a year before, according to the Royal Automobile Club. With this reality of huge and growing numbers of vehicles on the road in the UK and globally, the pollution they create is of huge significance to us all.
Greenhouse gas emissions have long been an issue on the automotive industry’s – and public – radar. Another pollutant gaining increased traction and attention is tyre ‘microplastics’ – specifically tyre and road wear particles (TRWP).
The friction between tyres and the road surface produces these tiny particles. These are known to be comprised of a mixture of tyre tread and road-pavement material. Although the colloquial ‘microplastics’ name suggests that these particles are a form of plastic, in fact they are largely made up of materials in the elastomers group with their own unique mix of chemicals used in each individual tyre making process.
Sally Beken FIMMM, Knowledge Transfer Manager – Polymers at Innovate UK, explains, 'We band the word plastics around all the time, but for me, it is any persistent polymer. It includes plastics, elastomers, thermoplastics, any polymeric like material that has longevity.'
Invisible pollutants
There is a growing body of evidence suggesting that these TRWP are polluting our environment and reaching our water sources around the world.
Most recently, experts at Imperial College London, UK, have called for 'more to be done to limit the potentially harmful impact of toxic tyre particles on health and the environment'. They warn that 'even though electric vehicles (EVs) remove the problem of fuel emissions, we will continue to have a problem with particulate matter because of tyre wear'.
A SOENECS Insight Report entitled Invisible Ocean Pollutants from our Roads states, 'Vehicles drive over 330 billion miles per year in the UK. Every car tyre weighs about 1kg less when scrapped than at the start of its life and every truck tyre about 8kg less. A busy A-road in an urban area with 25,000 vehicles each day will generate around 9kg of tyre wear particles (TWP)/km. UK tyre wear produces approximately 63,000t of TWP per annum. Tyre wear particles could account for 28-34% of all microplastics released to UK surface waters.'
The same report states, 'The term ‘Invisible Ocean Pollutant’ has been coined because of the physical invisibility of TWP and that few people know TWP are a major source of pollution in the oceans. The conclusion from the research is that TWP are a major environmental pollutant and this is only starting to become recognised as an issue.
'Annually, between 28% (17,640t) and 34% (23,120t) of TWP are entering the UK marine environment. Globally, this is a major environmental concern, where it is currently estimated that up to 1.03Mt of microplastic will be in the oceans by 2030 (if using the UK assumption of 28-34%, 288,400-350,200t of TWP), and more than doubling to over 2.5Mt (700,000-850,000t of TWP) by 2053.'
Beken adds, 'Nature is so diverse that we are not quite sure the impacts of all these pollutants on nature itself. There are two aspects to the pollution: one is the physical particles, and the other is the chemicals they contain. I think of those as two separate issues.'
Did you know?
6Mt of tyre wear particles are released globally each year.Source: Tyre wear particles are toxic for us and the environment, Imperial College London, UK
She notes that as well as the physical problem of ingesting lots of particles, the additives and other particles digested could be more harmful. 'An elastomeric compound has got lots more chemicals in it than a plastic. Elastomers are highly formulated and plastics are generally a little simpler…In elastomers we use some many highly functional chemicals to get the kind of properties that we need for car tyres.'
Professor James Busfield FIMMM, Chair of the IOM3 Elastomer Group and Professor at the School of Engineering and Materials Science, Queen Mary University, London, UK, expands on this point saying car-tyre treads are nearly always made with styrene-butadiene rubber (SBR). 'SBR is a synthetic material that hangs around in the environment…for a very long time.'
He explains that SBR is used as it has lower rolling resistance, so as the tyres are being used, it dissipates less energy. The other benefit of the material is durability so the tyres last longer. In short, he says, 'there are lots of potential reasons why you would want to use SBR, but the waste material you get from the tyre debris is probably more damaging.'
Industry action
The Tyre Industry Project (TIP) is one of the bodies that has turned its attention to this issue. It is a global, voluntary, CEO-led initiative, representing approximately 65% of the world’s tyre manufacturing capacity and started operating in 2005.
While TIP was at pains to point out it does not address the reduction of tyre wear emissions by design or manufacturing, as this remains the responsibility of each manufacturer, it is keen to highlight the work they are doing in this area in bringing the sector together.
For more than a decade, TIP has sponsored research to contribute to the growing body of scientific knowledge on the physical and chemical characteristics of TRWP, their potential presence in the environment, and the risks they may pose to human health and the environment.
Gavin Whitmore, Senior Manager of TIP, comments, 'The peer-reviewed studies we have sponsored to date have found TRWP are unlikely to pose significant risk to human health and the environment. However, we are mindful of an evolving scientific understanding of TRWP, including some research that has reached different conclusions, so we continue to support independent research to improve the knowledge base.
'TIP’s ongoing research includes the sampling and modelling of TRWP in soil, air, rivers and oceans, studying the degradation of TRWP in the environment, and investigating any potential impacts of long-term exposure of organisms to TRWP. Our research is published in peer-reviewed scientific journals.'
Professor Richard Thompson of Plymouth University, UK, is more bullish on microplastics hazards having led the field in this area. He notes that evidence shows that a range of different types of microplastics have the potential to cause harm, and he includes TRWP in this. Though he admits, as far as polymers go, 'We do not have that full understanding'.
In terms of looking at safe polymers to use he says, 'I think we ought to take the precautionary principle and try to reduce the contamination of the environment rather than hundreds of different experiments to say, well, this microplastic of this polymer is less harmful…Because actually, at the end of the day, the formulation for tyres is the way that it is because tyres are important in saving lives…There are always going to be tiny particles.'
The Imperial College briefing paper calls for policymakers and scientists to investigate the complex problems related to tyre-wear pollution, from the basics of wear-particle production, to understanding how these particles affect the health of people and the planet. Potential innovation solutions include particle-capture technologies, new advanced materials, and disruptive business models that encourage different transport choices. The report says these need to be coupled with clear policy and regulation and a broader discussion of urban transport systems.
The research efforts, it says, should include the following:
- Establishing standardised ways of measuring environmental tyre wear levels and their toxicity.
- Reducing harm to land and water species, and in humans, by tightening limits on the use of harmful components in tyre materials.
- Launching new trials to better understand the short- and long-term effects of different sized particles on the environment and human health.
- Efforts to better understand underlying wear mechanisms and to propose wear mitigation strategies, such as reducing vehicle weight, using advanced driving techniques, and ensuring tyre materials pass wear-resistance regulations.
In the driving seat
Thompson and Whitmore also recognise the role of road-users in this mitigation effort.
Whitmore says, 'Importantly, driving and vehicle maintenance practices that are recognised for more efficient fuel consumption can also achieve direct positive impact on reduction of TRWP generation – these include accelerating gently, coasting to decelerate and maintaining appropriate tyre pressure.'
There are question marks over the impact of EVs, Whitmore notes a balance here. 'The instant delivery of torque in EVs and their additional weight have been associated with increased tyre wear. However, a key outcome of more EVs on our roads will be the increasing importance of non-exhaust emissions as EVs replace exhaust-emitting vehicles.'
Moving forward, Whitmore says, 'The tyre industry is helping to improve awareness of different TRWP mitigation strategies and their effectiveness. In 2022, the European and US associations that represent tyre manufacturers at the regional level (ETRMA and USTMA) launched a review of literature concerning TRWP mitigation strategies, and a resultant global state-of-knowledge report on TRWP mitigation strategies will be published later this year.'
He highlights there is growing recognition of the importance of a multi-stakeholder approach to managing TRWP. This is reflected in initiatives such as the European TRWP Platform. This platform brings together stakeholders, including tyre, automobile, road makers, the scientific community, and (national/European) policymakers to address the question 'how can we reduce TRWP without impacting the important role tyres play in road safety and mobility?'
TIP has also established a TRWP-Mitigation Task Force to complement their research efforts.
On the road
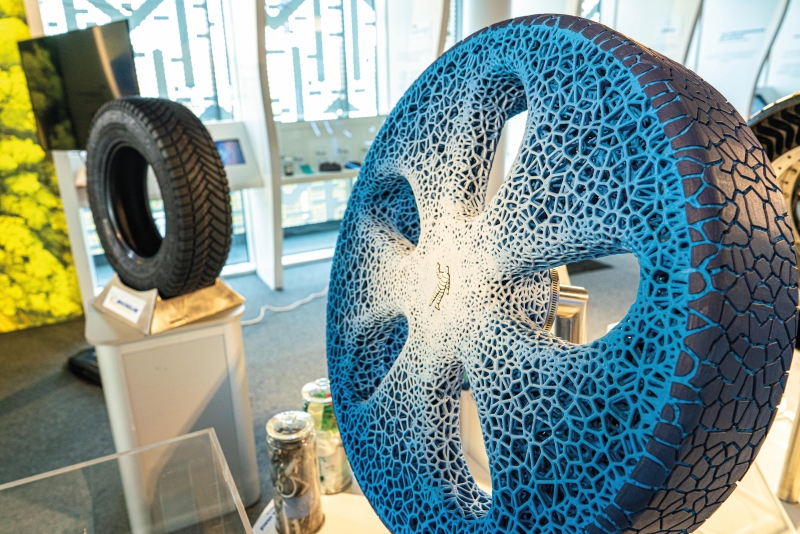
Several major tyre manufacturers are seeking to confront the issue of TRWP in terms of design. Michelin, for example, is developing the ‘Vision Concept tyre’. Cyrille Roget of Michelin states, 'Michelin Uptis is made exactly as a standard tyre in terms of materials…The only difference comes from the reinforcements.' Michelin Uptis is made using fibreglass. 'This specific fibreglass is made internally and is protected by 50 patents…It is embedded in resin and then inside normal rubber.'
Michelin Uptis is being assessed for environmental impact in real-life conditions. 'This is exactly what we started to do with DHL in Singapore, but we have already also tested Michelin Uptis in different parts of the world to measure the progress. Also, Michelin Uptis is designed so it can deliver a second life. So, it means, finding a solution to ‘recharge’ the tread so you don’t have to throw it away at the end of the first life.'
Michelin sees two main benefits for this tyre, 'First one is related to the airless technology. A conventional tyre is designed to have its optimal performance at the required inflation pressure. Any change to this required pressure is directly affecting performances, especially safety, the longevity of the tyre and its rate of particle emissions. So, a tyre pressure that is not regularly verified will lead to an increase in particle emissions. This will not happen with Uptis [as it] will always be at the optimal conditions.
'The second one is related to its construction, which will lead, with the same tread design as a conventional tyre, to a reduction of rate of particle emissions. The amount is still under calculation.'
Roget continues, 'In the world, on average 20% of the tyres don’t normally reach their end-of-life because they are prematurely removed because of punctures, sidewall damages or irregular wear due to lower pressure…This represents around 200 million tyres per year that have to be replaced because of those reasons.'
Another aspect to stopping TRWP reaching the environment is capture of the particulates. This is being addressed by a start-up based in London called the Tyre Collective. The co-founders are Hanson Cheng, Siobhan Anderson and Hugo Richardson. Cheng says, 'We discovered that tyre particles are charged from friction with the road so we can use electrostatics to capture them. The device is attached right behind the wheel and takes advantage of the airflow to capture this pollution.'
They were inspired to invent it because 'we were looking at microplastics at large and were shocked to learn that tyre wear is the second largest microplastic pollutant in our oceans. Even though this is a massive problem, there is no solution to tackle it and there is a lack of public awareness around this issue.
We saw this as an opportunity to innovate,' Cheng asserts.
In terms of the applicability of the device he says, 'At the moment, we are developing a retrofittable device that is fitted to the underbody of the vehicle. We are focused on delivery vans with the aim to fit our device on all vehicle segments. Long term, we want to work with vehicle original equipment manufacturers and integrate our device into new vehicles.'
In terms of efficacy, they do not have on-road capture efficiency at the moment. 'Our recent on-road test validated that our device selectively pulls out non-exhaust emissions (brake/tyre wear and road abrasion) from the air (up to 95% purity). Over half of what we capture is below 10µm (PM10).'
Further to this, 'Captured particles can be upcycled as a micronised rubber into a variety of applications, creating a closed-loop system. Some applications are shoe soles, new tyre treads, or bitumen. We work with a network of rubber recyclers to turn this pollution into products.'
The device is in R&D stage. They are running pilots to test the device and aiming for a soft product launch in 2024 at £150 per device, £600 per vehicle (assuming one on each wheel). They are working with vehicle and tyre manufacturers, fleet operators, researchers and government organisations to develop and pilot their device as well as complete advanced research on tyre wear.
Presently, the design is significant as many experts have highlighted particulate capture limitations, both in water treatment and from roads. Captured microplastics are not separated from sewage sludge, which is either landfilled or applied to the land in agriculture, according to the SOENECS report.
With new innovations in mind, another challenge Busfield foresees is lab-based test accuracy, 'We need to think about how to make sure that we can create lab-based tests that would actually work, in reality.' This is an area in which he has a personal interest.
Steering in the right direction
Beken, Thompson and Busfield all point to legislation‘s role in tackling the TRWP issue. As Busfield succinctly puts it, 'If you really want to force a change on the tyre sector, legislation is hugely important. But you do not want knee-jerk responses, you want something that is sensible, that actually improves the environmental impact. So, I think you have got to be very careful about banning things that are not necessarily detrimental, imposing additional costs. But then you have got to balance this against that the overall performance of the tyre over its lifetime. Make sure that you can achieve something.'
The SOENECS report sees some hope for road design going forward. 'Of the number of new roads that could be ‘smarter’ in 2030, if implemented now, these will only make up a fraction of the 262,300 miles of paved roads in the UK, but many of these roads will be high traffic flow and the world of 2030 may see smart roads with integral TWP capture technology.'
Busfield is optimistic, 'I think the technology is coming at speed with lots of academics working in this area.' Beken herself notes that she does not envision a future where we do not use rubber in tyres.