The future of chemical recycling – recycling the unrecyclable
The future of chemical recycling was explored in an online event held over the summer.
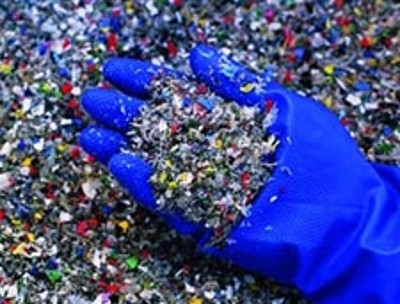
Chemical recycling needs to play a vital role in the waste management mix to tackle the ‘hard to recycle’ products and therefore requires financial backing, concluded speakers at The Future of Chemical Recycling webinar hosted by the British Plastics Federation.
This is said to be especially important as across Europe all plastic packaging has to be reusable or recyclable by 2030. The presenters agreed that chemical recycling cannot solve the world’s ‘plastic problem’, but rather it is a complementary approach to well-established mechanical recycling.
Carlos Monreal, President of Chemical Recycling Europe (ChemRecEurope), put forward a definition of chemical recycling as ‘any reprocessing technology that directly affects either the formulation of the polymeric waste or the polymer itself and converts them into chemical substances and/or products whether for the original or other purposes, excluding energy recovery’.
He continued by highlighting its role in processing contaminated plastics, noting that several countries in the south of Europe have more waste piling up in their landfills, while north European countries incinerate more of their waste.
However, gaining initial financial backing is a hinderance in getting chemical recycling technologies and methods off the ground, said
the speakers, whereas it is easier to access additional funds once up and running.
‘I think that as with a lot of clean tech, probably the biggest barrier is finance. I think we’ve lost a lot of time [and we could have moved] a lot quicker if we had more investment at the appropriate time,’ Adrian Griffiths, CEO and Founder of Recycling Technologies, stated.
From a retail perspective, James Bull, Head of Packaging at Tesco, noted that there are several soft materials in a shopper’s basket that ‘are fantastic from a property perspective – they have been designed really well – but from an end-of-life perspective, we struggle to encourage our customers to recycle it because there is nowhere for that material to go’.
Bull detailed a project to deal with these materials, whereby customers can bring the flexible packaging back to the store for Tesco to handle. Pre COVID-19, 10 stores participated in the trial and reported a return of around one tonne per store per month.
Bull highlighted, however, that there is a problem with scale. Tesco recognises that they can take the material back, segregate what can be mechanically recycled, but struggles with the next step. ‘We recognise that we can offer a service, we just struggle with where to take that material and where to channel it to get a positive end-result. We’d like to do more, but without the capacity, without the transparency, without the confidence and without clarity of timescales – it is very difficult for us to engage with customers at the scale we’d like to,’ he said.
A final recommendation from the event was that policy needs to catch up and recognise the potential of chemical recycling to fast track its use. It was suggested that chemical recycling is further incentivised over linear alternatives and fully recognised as a recycling method.
A second life for hard-to-recycle polymers
ReNew ELP, based in North Yorkshire, UK, who featured in the above event, is developing what it claims is a ‘world’s first’, commercial-scale, plastic chemical recycling facility using the Cat-HTR technology (catalytic hydrothermal reactor). This process uses supercritical water, heat and pressure to convert waste plastic considered unrecyclable via traditional mechanical recycling, back into valuable chemicals and oils for the petrochemical industry and into feedstock for new plastic and other materials.
Kim West, Spokesperson for ReNew ELP, explains, ‘To begin the process, the waste is prepared for conversion in the front-end processing facility. Here it is shredded and contaminants such as glass, stones and metal are removed. The mixed polymer stream is then mixed with supercritical water and heated, and placed into the reactor where the supercritical water acts as molecular scissors to break down the existing carbon to carbon bonds, donating hydrogen and reforming shorter-chain hydrocarbons. The product is then separated through a flash distillation column into four main products – naphtha, distillate gas oil, heavy gas oil and heavy wax residue. These are then stored and shipped back to the petrochemical industry.’
She notes that what distinguishes the technology from others is ‘our use of direct heat transfer, which occurs due to the use of supercritical water – this gives more control over parameters and reaction conditions, resulting in very stable end products’.
West elaborates, ‘Cat-HTR can process any polymer type, however, our target polymers are the plastics that cannot be recycled via traditional mechanical recycling, such as multi-layer, flexible and rigid plastic like films, pots, tubs and trays…including contaminated post-consumer plastics from both the food and medical sectors…These plastics would normally be sent to landfill or incineration. The plastic is sourced from post-consumer waste, and it is the residual stream remaining after materials that can be mechanically recycled [that] have been removed.’
She continues, ‘Vitally, new materials made from ReNew ELP’s chemically recycled feedstocks are suitable for use in food-contact packaging material, a problem area for mechanical recycling systems.’
Independent studies have also shown that the Cat-HTR technology can reduce CO2 emissions by two tonnes for every one tonne processed when compared to incineration, notes West, and ‘a lifecycle assessment of ReNew ELP’s process against traditional fossil resource has shown a potential CO2 saving in excess of 70%’.