The changing face of business
IOM3 Student & Early Career Committee members explain how sustainability issues are affecting their roles.
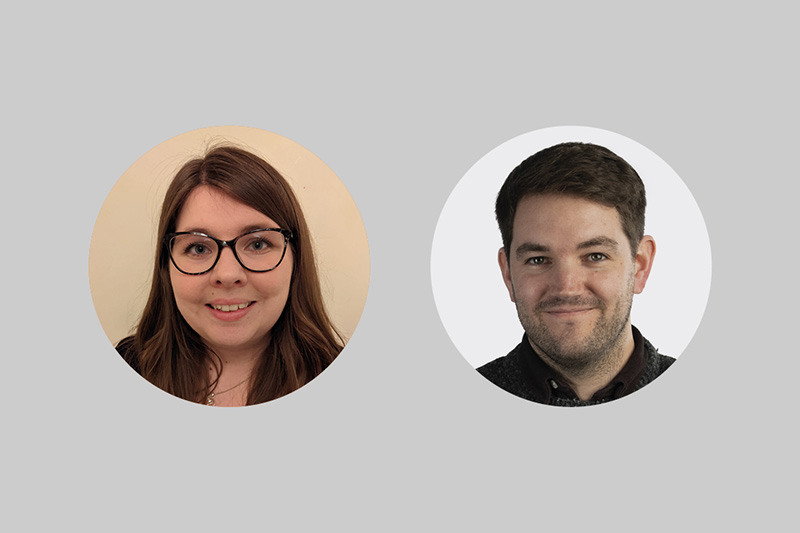
AG = Aimee Goodall MIMMM from Tata Steel UK, and MK = Michael Kenyon MIMMM from Innoval Technology.
Tell us more about your role?
AG: I am the Through Chain Value Manager within Technical at Tata Steel UK. I have been in the role since October last year. I am also the Chair of the Student and Early Career Committee (SECC) within IOM3.
MK: I am a Senior Materials Engineer at Innoval Technology. We are a technical consultancy to the global aluminium industry. I have two main roles, which are working as a sustainability analyst and physical metallurgist. I have been at Innoval since October 2018, so just over four and a half years. Before I started at Innoval, I completed a PhD in Advanced Metallic Systems with my project based on automotive aluminium alloys.
Within my sustainability role, I help our clients understand their product environmental footprint by conducting Life Cycle Assessments (LCAs) on processes along the aluminium supply chain. One of the biggest and most important aspects of the role is to educate the industry on the capabilities and future new technologies that will lead the sector to a more sustainable future. This includes increased recycling of end-of-life products and investment into using a higher degree of renewable energy in the production of primary aluminium and the rest of the supply chain.
My role as a physical metallurgist allows me to prepare, test and analyse aluminium alloys across multiple sectors, helping our clients with alloy development and microstructural investigations that may lead to improved performance or more efficient design. I also enjoy delivering interactive talks on metallics to students of varying ages from university to primary school level. I try to portray the varied roles that students can gain from a career in material science including metallurgy.
What does sustainability mean in your industry?
AG: To me, sustainability means using what you have well, not producing unnecessary waste and reducing the impact of what you produce. It also means helping to produce technology that promotes and develops environmentally sound practice.
MK: The global aluminium industry, like most other material sectors, is not currently sustainable with 1.175Gt of CO₂e emitted in 2021. These emissions are increasing year-on-year and there are many other environmental impacts to consider. In order to align with a 1.5°C pathway, there are significant technical, financial and infrastructure challenges to overcome. However, it is not beyond reason that these pathways can be met by 2050, and there are significant opportunities to lower the environmental impact of the global industry.
Aluminium can be a key material in the transition to a more sustainable world as the basic properties align with a circular economy. Aluminium is lightweight, conductive and can attain high strengths, in combination with other beneficial properties that make it suitable for automotive, construction, electrical, packaging and the consumer industry, among others. Most importantly, aluminium is infinitely recyclable. This means the material can be remelted and cast repeatably without losing any of its inherent properties.
For the industry to achieve the targets set out in the Paris Accord for limiting global warming to a maximum 1.5°C, the key levers that need to be achieved are energy decarbonisation, increased recycling of secondary material (both post- and pre-consumer scrap), resource efficiency and development of new technologies to reduce direct process emissions. By 2050, the estimated total global aluminium sector emissions need to be a maximum of around 53Mt CO₂e. This equates to a reduction of 95% in the next 30 years, while maintaining growth of the industry in its key markets.
How do environmental challenges currently affect your work?
AG: Steel is a very energy-intensive industry. This poses challenges that the industry is working hard to address. As society changes to address environmental challenges, new skills, technologies and ways of working will appear within all industries. People need to be adaptable and ready to take on challenges. Having a broad background to bring new ideas will help make this transition easier.
MK: One of the main challenges we face across the wider industry is the use of LCAs. LCAs as a methodology is a useful tool to help us understand both product and process environmental impacts. However, various methodologies exist, and greenwashing can easily occur when methods and standards are manipulated, or there is a lack of transparency in reporting the methods used.
Trade associations around the world are working to release more stringent guidelines on the use of certain methods in LCA for the aluminium industry. In combination with more transparent reporting, the aluminium and other metallic sectors can avoid greenwashing and provide more detailed environmental footprints that can be used to understand and lower emissions.
How do you anticipate these issues affecting your career in the future?
AG: Careers will need to change in industries to address sustainability and environmental challenges. We will have to learn new technology, new skills and change our current priorities, as well as being prepared and flexible to anticipate the unknown. Even in the last few years, Industry 4.0 has started to play a part in all industries, so it will be interesting to see what skills people will need to develop to accommodate new technology.
MK: My entire career could easily be forged by the targets and actions of the aluminium sector to improve environmental targets over the next 30 years, as moving towards a more sustainable industry is the number one topic and conversation in most projects. Physical metallurgy, process engineering and sustainability will be interlinked moving forwards.
I look forward to working on these challenges the sector faces, and hope I can contribute to improving the sustainability of the industry. I particularly look forward to working on improving post-consumer secondary material content in the aluminium alloys used across all sectors. This can be achieved following several work streams, for example, designing scrap-tolerant alloys by understanding the effect of impurity elements on material performance. By understanding elements such as iron and copper in the microstructure, this will allow us to expand on existing alloy chemical specifications. These new expanded chemical specifications could be made using increased secondary material that may contain higher levels of the impurity elements. Advanced sorting techniques can also be used to extract specific aluminium alloys that are more aligned to the target specification.
How do you think your sector, business and work will have to change?
AG: We need steel to help transition towards net-zero. There are a number of strategies that could be used – different methods of production, different energy sources or carbon capture. Perhaps something we haven’t even thought of yet, only time will tell. I think the biggest asset businesses have is its people and their skills, knowledge and passion for their industry. Without people we won’t be able to take on any of the upcoming challenges.
MK: Innoval Technology has always been an advocate for recycling aluminium – leading and contributing to numerous projects, both private and publicly funded, that promote the increased use of pre- and post-consumer scrap. To help with reducing the need for primary aluminium with high environmental impact, recycling of end-of-life post-consumer aluminium should become the heart of the industry. This will require significant changes in current industrial practices to fully recover and utilise aluminium alloys.
For example, the largest sector for aluminium alloys is the automotive industry. The current global practice for vehicles at end-of-life is to partly dismantle, crush and shred the majority of the vehicle together with metallics (aluminium and steel) being the main constituents that are then mixed. Even though advanced sorting techniques are rapidly improving in terms of productivity and recovery, alternative end-of-life treatments of vehicles could significantly improve the recovery of specific alloy families. Advanced sorting will be critical to improving aluminium recovery and extracting specific alloy families, but increased dismantling of these allows for easier recycling into the same application, promoting a circular economy in the automotive sector.
Another key pathway is the transition to using renewable energy. Currently, the majority of the electricity required is for smelting of aluminium to a near pure form. The source of this electricity dictates the embodied carbon of the primary aluminium produced. Therefore, a sustainable aluminium sector is one with recycling as the main source of material and primary aluminium with a much lower carbon footprint.
By 2050, the carbon footprint of primary aluminium needs to be at an estimate 0.5t CO₂e per tonne of primary aluminium produced.
A lot of significant challenges lie ahead for the global industry, but also exciting opportunities for the aluminium sector to support a cleaner, greener future for the planet.