Testing the machinability of flexible packaging materials at high speed
A novel testing method could help optimise the feeding and running qualities of recyclable, flexible packaging materials in high-speed, flow wrapping.
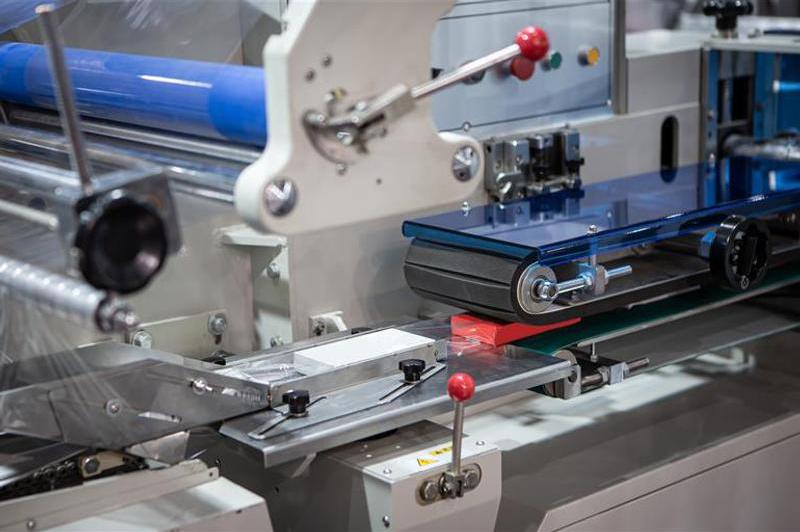
Researchers at the Fraunhofer Institute for Process Engineering and Packaging IVV in Dresden, Germany, explain that current industry standards allow the optimum machinability of flexible packaging materials – foils or paper from a roll – to be tested through evaluating the coefficients of friction (CoF) of these materials at low speeds.
However, when switching to recyclable packaging – films and tubular bag packaging – this test method fails to offer a realistic assessment of optimum machinability.
This is because the packaging process for these materials operate at very high speeds or cycle rates. Finding a way to overcome this is critical to avoid quality fluctuations, defective packaging, product damage and flatness issues.
A method for evaluating CoF values at the very high speeds or cycle rates used in the flow-wrapping process has been developed and tested at Fraunhofer for a new standard, VDMA 34171.
Nicole Ludat, Group Leader Material Testing and Monitoring Technologies, explains that an engineer’s first consideration when evaluating the optimum machinability of the flow-wrapping process is the friction behaviour between the different packaging materials and the tool surface.
Next, they must consider factors like velocity, the tool temperature or the tool surface that will influence the CoF, and consequently, the feeding and running attributes of different recyclable packaging.
The new test is based on the Euler-Eytelwein formula, which describes the friction of ropes against a tool surface, with a particular focus on the wrap-around angle.
'The idea was that most of the packaging material is pulled over a tool surface, for example, during flow wrapping, rather than pulling a weighted sled over a piece of packaging material,' explains Ludat.
'We have done some tests with different foils and paper materials, considered the velocity, the wrap-around angle, the kind of tool surface and radius of the tool surface.'
After taking measurements, the researchers say the CoF of polyethylene and polyethylene terephthalate decreases significantly with increasing velocity (20mm/s to 2,000mm/s), whereas it increases for paper. Although further testing is required.
According to Ludat’s team, the method has enabled them to evaluate the influences on the CoF of flexible packaging materials from a roll, rather than a flat piece of packaging material, with a recommended wrap angle greater than or equal to 120o. Where a wrap angle has not been specified, it should be undertaken at 135o, say the researchers.
Ludat says this allows for endurance tests to evaluate tool-surface changes, as well as examine the durability of coatings and the resulting changes in CoF.
The research project concludes that the speed of the flexible packaging material from the roll significantly influences the CoF of foils.
Significantly, the engineers say they can reproduce an industrial machine’s real load conditions in the laboratory, and have converted the test evaluation into the German standard VDMA 34171.