Taking shape – an inherently mouldable wood
Scientists claim to have developed a wood with a unique wrinkled cell structure that renders the material foldable and mouldable while also improving its mechanical strength.
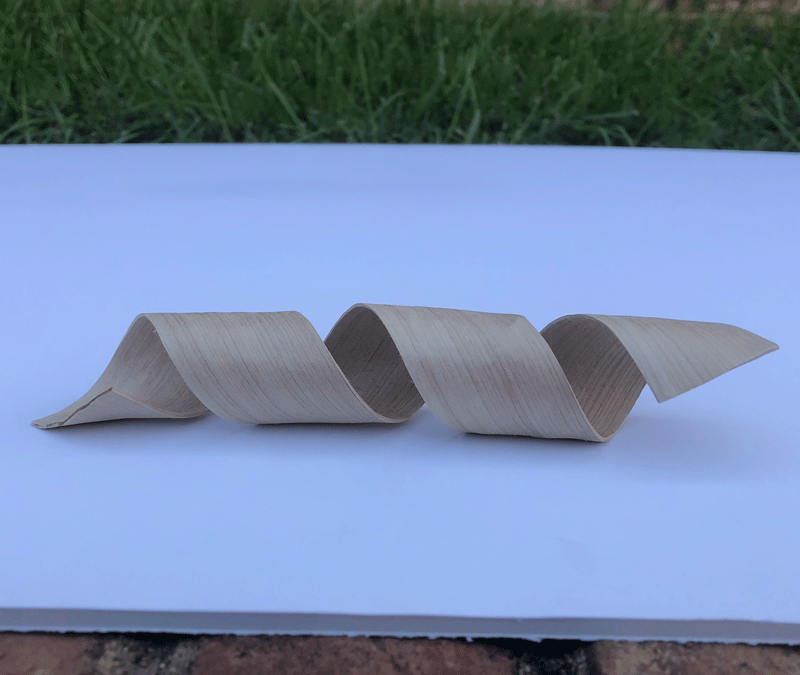
The technique, known as ‘water-shock’ assisted cell wall engineering, could help shape wood into lightweight and strong 3D structures that are processed in a similar manner to polymers and metals. This could open up possible applications in buildings, automotives and aircraft, where both complex shapes and strong mechanical properties are required.
Dr Liangbing Hu, from the University of Maryland, USA, explains, ‘The natural wood starting material has a 3D hierarchically porous cellular structure with many hollow vessels and fibres. Cell wall engineering approach involves partially delignifying and softening natural wood.’
The paper, Lightweight, strong, moldable wood via cell wall engineering as a sustainable structural material, published in Science, explains the process. ‘Firstly, a sheet of natural wood (basswood) was partially delignified by treating with a boiling aqueous solution of 2.5M sodium hydroxide and...sodium sulphite for 48 hours, followed by immersion in water several times to remove the chemicals.
‘Next, this partially delignified wood (~300wt.% water content) was air dried at room temperature (25±4°C) and a relative humidity of 45-60% for 30 hours to form the shrunken wood intermediate (~8-12wt.% water content), which was then immersed in water for three minutes (water-shock process) to form the mouIdable wood.
‘Finally, the 3D-moulded wood was achieved by shaping the mouldable wood into the desired structure and removing water from the material by air drying at room temperature for 30 hours.’
Hu suggests that the selective opening of the cell wall structure may provide two simultaneous effects. The partially open vessels create space that can accommodate both compressive and tensile deformation in an ‘accordion-like’ manner, allowing the material to undergo severe compression and tension while being folded, even up to 180˚ without cracking.
Meanwhile, the densely packed closed fibres can provide mechanical support for enhanced strength.
The different shapes and structures that can be achieved can then be set into place with air drying to remove the remaining water, forming the final 3D-moulded wood product by mechanical bending, folding, twisting and moulding press.
Hu believes this improves on current techniques of wood manipulation, which rely on physical sculpting, carving or turning into complex 3D shapes, but do not change the intrinsic material. Furthermore, he notes that conventional wood shaping techniques can only achieve large curvature i.e., the wood can only be slightly bended.
He says, ‘Our work describes an…approach to endowing wood with many of the advantages of metals and plastics (strength and formability)…Given that wood is one of the oldest structural materials, this development represents a significant advance for wood's structural applications with potentially transformative utility of this renewable material.’
As a proof-of-concept, the team has shaped the mouldable wood into a honeycomb core structure that can potentially replace aluminium alloy in construction.
Hu adds, ‘In addition to metal replacement, the 3D-moulded wood can also replace traditional wood with much better performance, with a selection of a broad range of wood species as the starting materials. For example, 3D-moulded wood veneer fabricated from fast growth wood can be a cost-effective, high-performance skin layer for advanced furniture with significantly improved mechanical properties (i.e., scratch resistance).’
He suggests that scaling the manufacturing of corrugated 3D-moulded wood structures could be accomplished using the mature roll-to-roll manufacturing processes from the wood and pulp industries.