Recent Developments in Additive Manufacturing
An overview of how 4D printing can be used to create complex geometries in high temperature alloys and ceramics on a nanoscale.
Please login or create your My IOM3 Account to access this on-demand webinar.
Engineering Structural Integrity Series
We are delighted to be working with FESI (Forum on Engineering Structual Integrity) to host a series of lectures highlighting the importance engineering structural integrity to a variety of sectors.
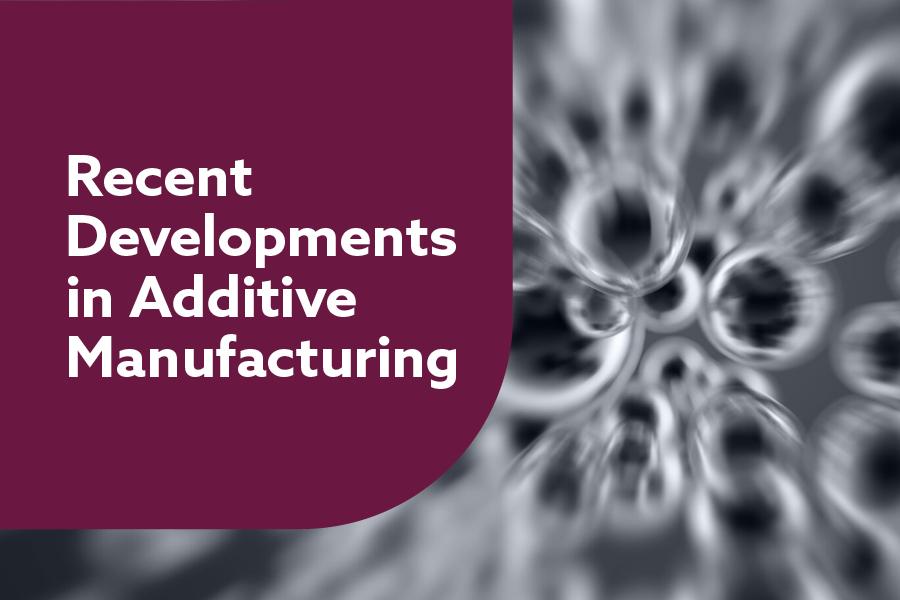
Additive manufacturing is a fast-growing technology with applications in a variety of areas such as: biomedical implants, aerospace components and structures. Achieving complex-shaped architectures in high melting point alloys and in ceramics is still challenging, but additive manufacturing of polymer-derived ceramics enables breakthroughs in geometrical complexity of ceramic structures.
This lecture focuses on solving the problem of applying nanostructured ceramic materials with complex shapes. The new concepts of supra-nanostructured materials and nanostructured dual-phase (glass-nanocrystal) composites will be discussed. The first supra-nanometre-sized, dual-phase, glass-crystal coatings were fabricated using the PVD process. The obtained supra-nanostructured magnesium alloy consists of ~6nm sized core crystals embedded in 2nm glassy shells. The mechanical properties are ten times higher than conventional crystal magnesium alloys. The second example is nanostructured, glass-nanocrystalline, aluminum-based alloys with very high deformation capacity and strength. The potential developments of nanostructured dual-phase (glass and nanocrystalline) functional materials with specific biocompatibility or optical properties and ultra-high strength can be anticipated.
Four-dimensional (4D) printing technology, which combines traditional three-dimensional (3D) printing with structural deformation , has been developed. 4D printing enables more complex shapes to be created than is possible with conventional 3D printing. Achieving this in ceramics, however, has been hindered by the fact that 3D-printed ceramic precursors are usually rigid and thus difficult to be deformed after full crosslinking. Directly 3D printed metallic materials have lower fatigue resistance compared to their counterparts produced by the powder metallurgy technologies including HIP. We will present their potential application in biomedical implants. The post-treatment of 3D printed components in a titanium alloy can drastically enhance the fatigue resistance. Finally, the perspective of new 4D printing methods with associated control media will be presented.
Meet your speaker - Professor Jian Lu, City University of Hong Kong
Prof. Jian Lu is Chair Professor of Mechanical Engineering and Director of the Centre for Advanced Structural Materials at the City University of Hong Kong. Professor Lu’s primary research interest is advanced nanomaterials and their integration in mechanical and biomedical systems using the combination of experimental mechanics and mechanical simulation. He has also branched out into several other areas of interest including surface science and engineering, biomechanics, residual stresses and nanomechanics. He has published more than 360 SCI journal papers including papers in Nature (cover story), Science, Nature Materials, Nature Communications, Science Advances, Materials Today, Advanced Materials, PRL, Acta Materialia, and Journal of the Mechanics and Physics of Solids. He received the French Knight of the National Order of Merit and French Knight of the National Order of Légion d’Honneur in 2006 & 2017 respectively. He was elected as a member of the National Academy of Technologies of France in 2011. He received the Guanghua Engineering Science and Technology Award from the Chinese National Academy of Engineering in 2018.
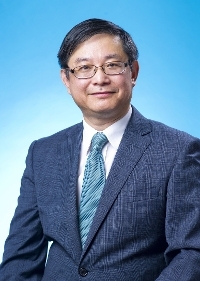
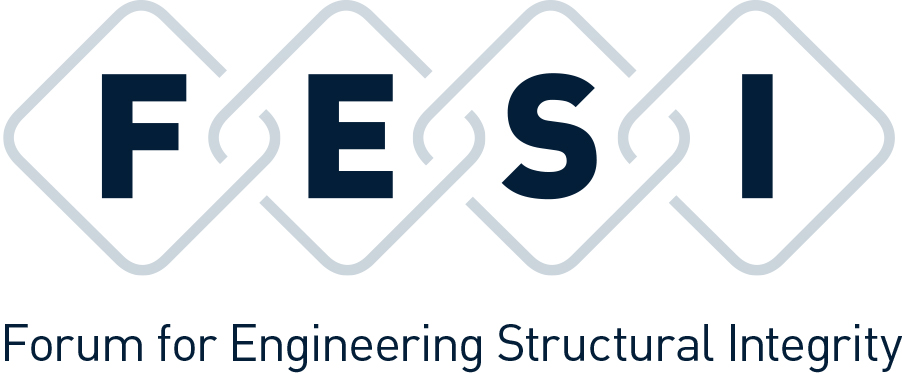
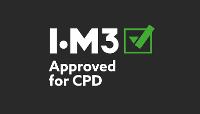
These activities are approved for Professional Development by the Institute of Materials, Minerals & Mining.