Still firing the imagination
An overview of kiln advancements over time
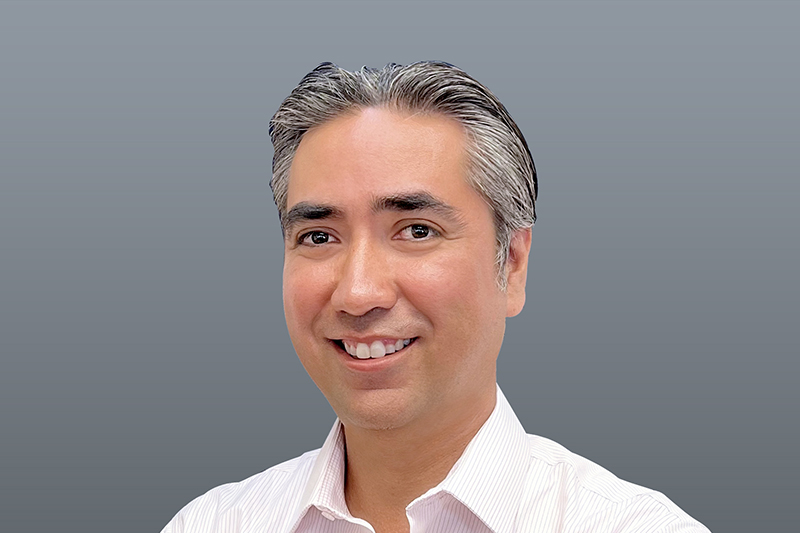
Kilns, rather than the simpler pit-firing process, have existed for a long time – certainly 8,000 years and very probably further back. Some sort of constructed chamber was necessary to consistently achieve the required temperatures for both firing ceramics and calcining materials at volume and to introduce some control.
Many people will be familiar with concepts such as wood-fired beehive and dragon kilns, and then later on Hoffmann kilns – predominantly for bricks – and bottle kilns for whitewares, where coal was commonly used as the fuel.
Not surprisingly, all around the world, manufacturing clusters built up in areas where both clay and these traditional fuels were in abundant supply. This resulted in increased volumes and the attendant economies of scale. However, these clusters also brought heavy pollution.
Over recent decades, kiln manufacturers have steadily cleaned the process while still enabling their customers to achieve consistency, excellent levels of productivity and superior end-product quality.
The advent of piped-in natural gas of course started to make a big difference. But, as with any finite resource, the question is how to make best use of it?
The old premix burners, which were common, had the disadvantage that only low-gas velocities were possible. Try forcing gas flow beyond a certain speed and you risk flashback.
These have now mostly been replaced by high-velocity burners. These burners are far more efficient but offer other benefits too. Greenhouse gas emissions are reduced – i.e.
low-NOx operation – while firing performance is enhanced. These burners also feature a high-turndown ratio, leading to much more flexibility and, over time, significant cost savings.
Now, we’ve all seen stacks and perhaps wondered what is being emitted – well, in the past, the answer was a good deal of wasted heat, along with the products of combustion, including some noxious elements. One way that kiln manufacturers have tackled this issue is the incorporation of regenerative and recuperative systems into modern designs, particularly where continuous (tunnel) kilns are concerned.
There are several different approaches to waste-heat recovery, but in simple terms, this involves collecting the preheated combustion air instead of allowing it to be vented to the atmosphere. Then it can be reused. This reduces overall fuel consumption, means that less cold air needs to be introduced into the chamber, and results in mitigated CO₂ emissions.
We can also see a move from heat recuperation via fairly simple heat exchangers to more complex heat-storage technology. There is an electrically conductive brick that can store and use renewable energy, while alternative systems can exploit high-temperature thermal storage. Both options reduce the reliance on fossil fuels for combustion, while also addressing interruption of supply issues and outages.
Moving from simple temperature-control loops to sophisticated, programmable, logic controllers and control-system architectures, such as supervisory control and data acquisition, means everything is governed by human-machine interface panels.
With rapid advances in smart industrial technologies, or Industry 4.0, the timescales and accuracy around troubleshooting have greatly improved – remote monitoring, intervention and assistance can be provided and even programmes changed. All this in minutes or hours, rather than needing a flight halfway around the world.
The obvious corollary to all this is the integration of machine learning (ML) and artificial intelligence (AI). ML/AI is a logical extension to computer modelling that will surely be exploited to lift industrial manufacturing operations up to the next level.
And more users are explicitly specifying an electric kiln where previously gas firing would have been the norm. Electric heating, quite normal in ovens, is also widely used in higher-temperature intermittent (shuttle) kilns.
Element technology has come on in leaps and bounds, meaning there are a number of options suitable for industrial kilns, but as one might imagine, for tunnel kilns, there has been a great deal of complex thermal analysis and design effort to achieve the necessary heat delivery, distribution and control.
It’s safe to say that electric heating won’t always be the answer. There are still certain products that do not readily lend themselves to being electrically fired, and elsewhere this route may not meet decarbonisation goals, depending on how the electricity has been generated.
There’s also the newcomer – hydrogen. It’s early days, but it started with a blend of natural gas and hydrogen for kiln firing. There are issues to be addressed in terms of hydrogen storage and delivery, but technically it’s feasible.
Just months ago, a 100% hydrogen firing of ceramics was achieved. It’s probably fair to say that hydrogen firing is still in its developmental stage, but it does look like forming part of the future firing jigsaw.