Steel joint facilitates extraction of geothermal heat
A steel piling joint for concrete pile foundations under buildings, which also extracts geothermal energy, is reportedly quicker, cheaper and safer to use than boring separate wells.
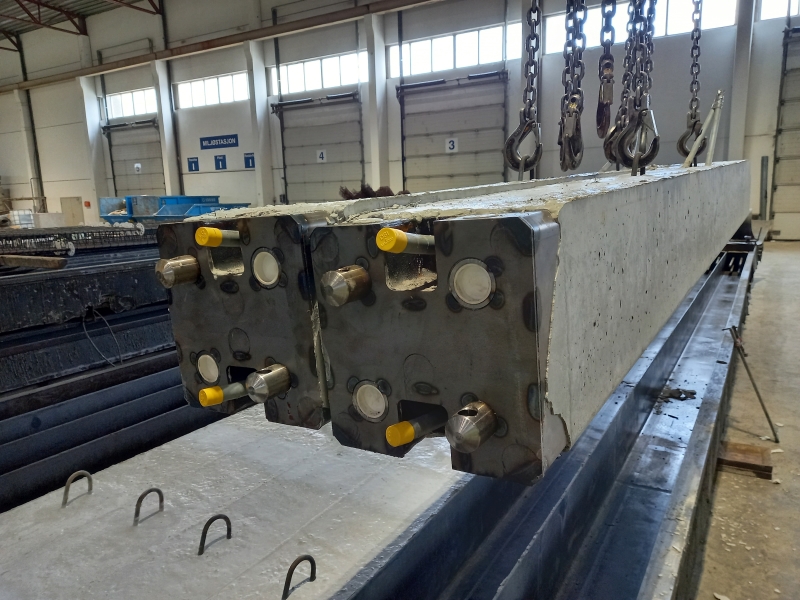
Geothermal wells for newbuilds are often bored to 150-300m deep, which removes large quantities of excess soil, notes PhD candidate Habibollah Sadeghi at the Norwegian University of Science and Technology.
The new prefab elements designed for precast-concrete-driven energy pile foundations are limited to 12-15m per segment. But even in shallow conditions, the amount of piles used and hence the total length means that the same energy can be extracted as from deep energy wells.
Sadeghi, the first person in Norway to earn a doctorate in energy piles, says, 'Using the energy piles as a source for ground source heat pumps decreases the energy consumption of buildings by 60-70%'.
He continues, 'The piles are normally driven up to the bedrock depth, hence they can have a length of a few metres and up to 100-200m in some projects. The ground temperature becomes stable after the first top 6-8m from the ground surface, hence there is a large potential...Using driven energy pile foundations will eliminate the cost of drilling borehole heat exchangers, hence making ground source heat pumps an economically viable option with an attractive payback period.'
The Driven Energy Piles (DEP) joint piece has two male and two female connectors. Two steel pins that lock the joints together connect the prefabricated concrete elements that form the piles, which are anchored in bedrock.
By using prefabricated concrete, the piles can be produced in large quantities with strict quality and safety requirements. The team behind them say the quality can be more easily checked compared to inspecting piles that are already cast in holes on site. Sidewall channels on the square joint are shielded by a small plate and allow embedded tubes to be connected without affecting the pile’s load-bearing capacity. Two joint sizes of 270mm and 350mm have been tested so far – the smaller has two sidewall channels and the large has four, but still weighs less than 20kg.
Sadeghi says that connecting the concrete segments takes less than 10 minutes and 40-60 can be installed in a day, while drilling a single cast-in-place pile might take half a day.
The piles are cast in horizontal formwork and reinforced using an internal ‘steel cage’ to strengthen the load-bearing capacity and protect against shocks, vibrations and other impacts as the piles are driven into the ground.
Using energy piles instead of conventional ones does not increase the number needed, notes Sadeghi, who highlights that the aim is to use the same length as what is structurally required.
The solution is intended for the first phase of construction, and so would be designed alongside the building.
Sadeghi notes he was inspired by the 100km of recuperator tubes running through the walls, bushings and cast concrete slabs of the underground line in Jenbach, Austria, which harvests 175 and 437MWh for heating and cooling from the ground surrounding the tunnels. He has published several studies comparing various heating systems in Norway and Europe and finds that, in colder climates, geothermal pumps are particularly efficient as the ground temperature remains stable.
'The concrete is a good conductor of heat compared to the surrounding ground, so the heat exchanged with the concrete will be exchanged with the ground. The principle in the design of the system is that the heat harvested/injected from/into the ground should be balanced so that the system works sustainably over the lifetime of the building.'
Initial prototypes were produced by Finnish manufacturer Liemet Oy towards the end of 2022, while the piles were subjected to European standard impact pressure and leakage tests earlier this summer, before being shipped to the University of Tampere, Finland, for flexural testing.
The joints, tubes and connections were reportedly undamaged during testing, with the piles having the equivalent load-bearing capacity and strength as traditional, precast concrete piles.
As the joint now satisfies the requirements for CE marking, it is deemed ready for use in the construction industry.