Steel in packaging
This section covers a brief history of the use of steel in the packaging industry.
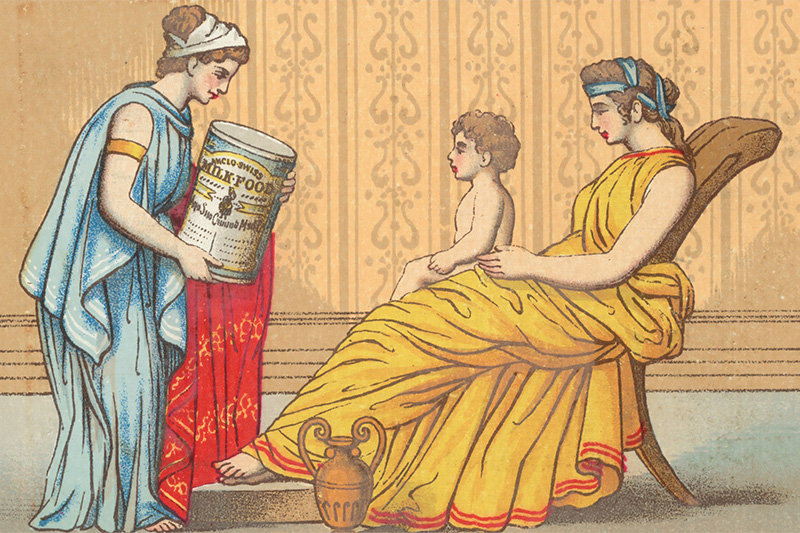
Food canning - the great innovation
Early in the 19th Century, Emperor Napoleon offered a prize of 12,000 francs for a new method to preserve food.
In 1806 Nicolas Appert, a French Inventor, presented a selection of bottled fruits and vegetables from his manufacture at the Exposition des produits de l'industrie française, but did not win the reward. In 1810 however, the Bureau of Arts and Manufactures of the Ministry of the Interior gave Appert an ex gratia payment of 12,000 francs on condition that he make his process public. Appert accepted and published a book describing his process that year. Appert's treatise was entitled L'Art de conserver les substances animales et végétales (The Art of Preserving Animal and Vegetable Substances). 200 copies were printed in 1810. This was the first cookbook of its kind on modern food preservation methods. Further information about Nicolas Appert can be found here.
This was the first technology that could be applied across a whole spectrum of food products to give a long shelf life. The work completed by Nicolas Appert was improved upon when the tin canister was invented by Bryan Donkin in England and patented in 1810 by Peter Durand.
The creation of the tin cannister, was the start of over 200 years of development and innovation for the food canning industry. Original tinplate cans were made from steel sheets dipped in a bath of molten tin. The Cans were handmade using solder to attach the disc end to the body. After the disc was applied, the contents were filled through a small hole, which was capped and soldered. The cans were heated in boiling water and the air expelled by repeatedly recovering a small vent called a brog. The end was then finally sealed with solder. The cans were processed in boiling water for several hours afterwards. A lifting ring was soldered on top and a label was added with the instructions ‘Cut round on the top near to the outer edge with a chisel and hammer’.
The early years of canning
In Britain, canning began with Bryan Donkin and John Hall. They bought the canning patent for £1,000 and set up the first canning factory, in Blue Anchor Road, Bermondsey.
Donkin's can operation commenced on 3 May 1813. King George III endorsed his product, canned beef, in June 1813. Donkin subsequently began canning mutton, carrots, parsnips and soup. In 1813, the Admiralty was first supplied with canned food and regularly by 1819 and a can of roasted veal was taken on Perry's voyage in search of the North-West passage in 1824.
In 1819, Thomas Kensett in New York started using glass canning for oysters, meat and vegetables and William Underwood in Boston, Mass, canned fruit and vegetables. It wasn't until 1837 did they completely over to glass and tinplate. A year or two after this, cans came into wide use in the United States.
Timeline
- 1820: canning of fish in France and Scotland
- 1842-3: Russia canned powdered milk
- 1846: First Australian tinned meat cannery
- 1849: Salmon canned in Ireland
- 1850: Condensed Milk in Britain *America in 1853; Switzerland in 1866)
- 1850s: Chicago: large expansion of meat canning industry e.g. Libby's corned beef in a tapered shape cans
- Late 1870s: Handmade cans were made at the rate of 60 cans per hour
- By 1900: Automatic machinery could make cans from sheet tinplate at 2500 per hour.
- 1901: Specialised can-manufacturing industry with formation of American Can Company
- 1905: In US, the rival Continental Can Company was established
Modern can systems - two piece & three piece
Modern can systems, both two piece and three piece, use steel plate electrochemically coated with either tin or other metal complexes.
Three piece cans use tinplate is coated on both sides from a tin chloride solution so that there is a higher tin coating on the interior, which is in contact with the can contents. Can bodies are side-seamed by welding plate edges together using an electrically heated copper wire. Can interior surfaces may be partially or totally lined with lacquers or polymeric coatings for asthetic reasons and/or added protection from corrosion.
Seamless, drawn two piece cans are manufactured in a number of different manners depending upon their end requirement. These fall into the catagories of single drawn, multiple drawn (DRD) and drawn and wall ironed (DWI) cans.
Two-piece cans are made using either pre-coated/polymer laminated and printed tinplate, or tin-free steel. TFS is also referred to as electrolytic chromium oxide coated steel (ECCS). TFS is coated to provide a corrosion-resistant surface. More recently due to EU REACH legislation on the use of hexavalent chromium, other forms of TFS have started to come onto the market, such as TCCT (trivalent chromium coated technology).
Creating value through packaging innovation
Steel food cans have a sound sustainability profile
- 100% recyclable with high recycling rates in Europe exceeding 72%
- The average shelf life of products in metal cans is 3 years, thus saving on food waste
- It does not require any chilling and thus has one of the highest eco-efficiencies
- It takes 5 hours to get from crop to can, so canned food is particularly safe
- Canned food locks in nutrients, vitamins and flavours directly after harvesting, without the requirement for preservatives or artificial colours
- The hermitically sealled can productes it's contents from damage by light, oxygen moisture and physical hazards of distribution. It also avoids spoilage by micro-organisms.
Due to the shelf life of canned products being extended, millions of cans are opened around the world and contents safely consumed. Innovations in the can ends have allowed socially sustainable improvements making them easier to open and use. Whilst tetrapak containers for some products are being adopted, so far the UK's 420+ million canned bean market has only been slightly disrupted by plastic pack innovations.
Steel packaging - the future?
Great innovation is deep and intelligent: when you understand user needs and can deliver solutions with valued benefits, society improves. This occurs, usually when you jump from one curve, to the next.
The packaging market is currently facing a wide number of disruptive products, from the beverage market, aluminium has dominated for years, in the food industry plastics from Tetra Pak and SIG Combibloc have started to come into the marketplace. The advent of retortable cartons is one change which the market has yet to be impacted by. Many of these markets remain the domain of the steel can.
In the future however, will subsequent generations shun the long-loved can and adopt these cartons, or opt for less processed and fresher product formats? With the growing green movement, our old friend the steel can remains uniquely placed, for it is 100% recyclable. Time, however, will tell.
Next Guide: Steel in transport