Spotlight: Shine like a diamond
Colin Lloyd, Head of Quality at Element Six, talks about building-in quality to synthetic diamond material processes.
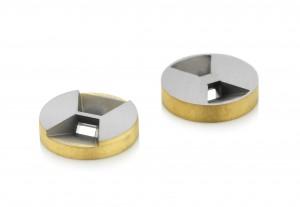
An approach to quality that encapsulates the needs of the customer and how this translates into production team activities was a key tenet of the work of Dr W Edwards Deming, American engineer and quality pioneer. The learnings from Deming have been absorbed into a variety of businesses across the globe, and his efforts to improve quality continuously are future-proof.
There are several activities a business must implement to achieve and sustain high quality. A leadership team’s thinking and strategy for organisational success must embed the idea of an ongoing, continuous adaptation and improvement of the organisation’s ability to serve its customers, making the principle of ‘building-in quality’ essential.
Consistency and reliability of the solution’s performance are crucial to ensure successful adoption and continued use of synthetic diamond. Building-in quality ‘rather than inspecting-in quality’ is of critical importance when you are pushing the boundaries of materials science and end-user applications.
What is building-in quality?
Heinrich’s Law, when considered from a product point of view, says, ‘One defect outflow could potentially incur many defects in a process.’ Good product conditions that are required to prevent outflow need to be identified.
Implementing counter-measures for defects at each process – so as not to make defective parts – indicates that poor quality must not be passed to the next process. Therefore, to make good products with no defects outflow, we need to adopt a building-in quality mindset at each step. The goal, therefore, of building-in quality is to make the process robust enough to make additional inspection unnecessary.
How do you involve the customer?
All businesses should listen to the voice of the customer (VOC). With synthetic diamonds, the customer’s drawing defines the product specifications, dimensional requirements and product attributes. There are nuances with customer requirements, such as their end application needs, which are not always clearly captured in the drawings. To improve on that, we developed a process to review directly with the customer what the critical to quality (CTQ) characteristics are for the product and revise the drawing accordingly.
A recent VOC study with a USA-based company that develops and markets products for optical spectroscopy has identified that the customer’s incoming check for diamond clarity was filtering the product for their viewing devices by 80% and non-viewing devices by 20%.
During the review, we agreed this verification process could be completed at Element Six, integrating a further value-adding step to the solution delivered. The VOC approach is a proactive tool to foster positive relationship building and collaboration between suppliers and customers.
How to deliver quality under pressure?
Smartphones have a refresh cycle that resembles the fashion industry. New materials, styles and technological advances are quickly introduced, demanding ever higher input and dynamic approaches from materials suppliers.For several years now, synthetic diamond has been the go-to solution for machining key components in a variety of industries and applications. On a recent customer project, an ultra-fine finish was needed for a smart phone housing, requiring a novel material solution.
Working with ultra-fine powders (0.5-1.5µm), synthesising the material at high pressure and high temperature and then producing the tool geometry are complex processes. With a sudden large increase in demand from the customer, operations had to build-in quality to deliver the required volume of material. This achieved the required solution – a tool so exact that it produces a near mirror-like finish due to the material’s manufacturing precision and quality.
The team focused on the process conditions, and for each individual step in the process, thought was given to the following questions: a) Is it easy to complete with success? b) Is it easy to notice if it has been completed successfully? c) Is it easy to determine if we have been unsuccessful (the team member needs to have comprehensive understanding of all the possible abnormalities)?
Ownership of building-in quality at each step sits with team members who are trained as ‘problem solvers’, while leaders and wider teams support with the design of a process to achieve the required quality and quantity of output.
What role does innovation play?
The building blocks of achieving high quality must start at the earliest possible stage. Generating ideas is a process of discovery with a large degree of freedom. As ideas come through the funnel and turn into strategy, the work of quality in assessing the technical and commercial feasibility involves completing a quality functional deployment (QFD) evaluation. This approach provides a structured method to identify and translate customer needs into measurable requirements and is used to map out the CTQ requirements at an early stage. The importance of design quality cannot be underestimated. QFD provides a communication tool for R&D staff, the product manager at the commercial interface with the customer, and the quality and operations teams in the manufacturing facilities.
A complementary approach to QFD is design for manufacture (DFM). The DFM manual describes key best practice for product design. The document outlines design guidelines and standards to enhance product manufacturability in terms of quality, speed, yield and cost.
Its importance is pivotal in ensuring that any issues are solved at design stage and not later and there are no steep learning curves at production stage (e.g. wasting time and resources on firefighting, volume ramp-up problems and post-launch redesigns).
Building-in quality ultimately means solving problems early by ensuring that design generates no defective solutions, delivers a seamless operation and provides an easy way to distinguish between good and less suitable products.
In the case of our oil and gas business, we use this approach to ensure that new solutions can flow through the product introduction process more smoothly and reach the market in a timely manner. This results in cutters of repeatable and predictable performance, enabling deeper and faster penetration below the surface, as well as reduced need for drill heads replacement, thus delivering cost efficiencies to field operators.
Who is responsible for quality?
Everyone is. Organisations are made up of individuals, teams, groups, functions, executive staff, etc., and there is a variety of business organisational models from bureaucratic top-down, to matrix organisations and agile teams, to name a few.
One underlying principle is that those closest to the product will have important insights on the solutions required due to the problems they face every day. Likewise, the leadership teams should understand the customer needs and the system problems, playing an active part in building-in quality in all that they do.
What is the future of quality?
Acknowledging that competitors are always looking to overtake the market leaders and continuing to surpass the competition with ever higher quality standards represent key strategic business objectives. With a clear sense that we are at the start of significant changes in both how we work and how we produce our materials, we need flexibility and agility to deal with the challenges and opportunities ahead.