Spotlight: How to perform aluminium surface cleaning and evaluate cleanliness
Innoval Technology aluminium surface consultant, Dr Junjie Wang MIMMM, presents the types of aluminium sheet surface cleaning used in industry and various techniques of assessing surface cleanliness to avoid problems by insufficient or over cleaning.
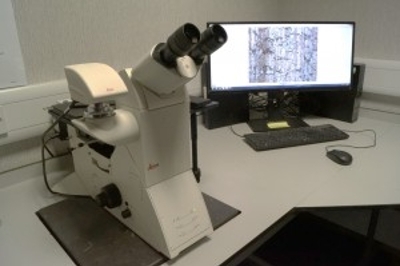
Aluminium rolled products are widely used in industry. In most applications, the surface of aluminium rolled products must be chemically or electro-chemically cleaned to remove residual mill oil, smut, surface oxides and most importantly, the near-surface disturbed layer to provide a uniform surface to receive pre-treatment. The near-surface disturbed layer is characterised with ultra-fine grains with oxide particles and lubricant residues pinning the grain boundaries. It is generated during hot rolling of aluminium alloys due to the interaction between the aluminium surface and the steel rolls.
Sufficient removal of the near-surface disturbed layer by cleaning is critical for successful pre-treatment, which can guarantee good corrosion-resistance after coating and long-term durability of adhesive bonding. Therefore, effective cleaning is vital to the performance of aluminium products such as automotive body sheet and beverage can sheet etc. While on the other hand, over cleaning should be avoided as it increases the cost of line maintenance.
Types of aluminium sheet surface cleaning
Cleaning of aluminium sheet surfaces is either carried out in a batch or a coil process. Coil cleaning has the benefit of taking a very short time – the treatment time takes seconds rather than minutes. Coil cleaning for aluminium alloys differ in terms of the solution chemistry used, the method of applying the solution and whether or not an external current is applied. It can utilise acid or alkaline cleaning solutions with immersion or spray application to the aluminium sheet surfaces. In each case, a multi-step water rinse follows the cleaning stage to thoroughly remove the cleaning solution from the aluminium sheet surfaces.
For acid cleaning, processes are usually based on sulphuric (H2SO4) or phosphoric (H3PO4) acid solutions and surfactants. However, hydrofluoric acid (HF) is usually added as an activator. Typical acid cleaning operating temperatures are in the range of 50–70°C for contact times of 5–60 seconds.
Alkaline cleaning processes are based on sodium hydroxide (NaOH) solutions. Typical operating temperatures are in the range of 50–70°C for contact times of 5–20 seconds. This is a fast etching process. However, solid precipitates form in the bath and aluminium hydroxide waste has to be managed. Some oxide particles and intermetallics, which are insoluble in the alkaline solution, form a smut layer that loosely attaches to the aluminium surfaces. As a result, alkaline cleaning must be followed by an acid de-smutting step.
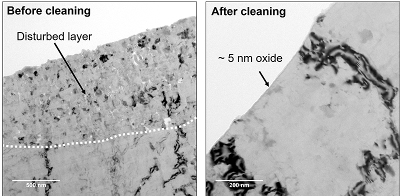
While the above-mentioned chemicals are relatively good cleaning agents when used alone, electrolysis can increase their power considerably. The mechanism and process of electrolytic cleaning in these acids is similar to anodising – the process generates the characteristic anodic oxide film with a regular pore structure on the aluminium surface.
The oxide film development is a competition between film growth and dissolution. By controlling acid concentration and temperature, along with the anodising voltage, it is possible to make the aluminium oxide dissolve at the same rate as it is formed.
This electrolytic cleaning does not need HF which is good news for health and safety and the environment. Furthermore, the process is very fast and flexible. For example, effective cleaning with minimal residual oxide can be achieved in 0.5–3 seconds. What’s more, the equipment can also work as an anodising pre-treatment line.
Evaluating aluminium surface cleanliness using microscopy
It is important to know how to evaluate the surface cleanliness of rolled aluminium for product quality control and process optimisation purposes.
Transmission electron microscopy (TEM) has been the main research method to examine the near-surface disturbed layer since it was re-discovered at the Norwegian University of Science and Technology (NTNU) in the 1990s. This involves cross-sectional specimen preparation using either ultramicrotomy or focused ion beam milling (FIB). The TEM method can only examine a very limited size of specimen each time, and it involves a high level of expertise, high cost and it can take a long time.
High-resolution low accelerating voltage scanning electron microscopy (low kV SEM) can also be used for cross-sectional examinations. In this case, you would examine the ultramicrotomed sample block, rather than the thin specimens for TEM. Low kV SEM has the capability of imaging the ultrafine grained disturbed layer directly on the rolled aluminium alloy surface by the channelling contrast of backscattered electrons. However, the topography of the rolled surface significantly influences the effectiveness of this technique. This is especially true for aluminium automotive body sheet rolled with electro-discharge textured rolls, which has a surface roughness Ra of 0.7–1.3µm.
Optical microscopy
Another technique is optical microscopy. This method of cleanliness evaluation is based on the optical characteristics of the disturbed layer which reduces the reflectivity to visible light, particularly in the short wavelength range. This makes the disturbed layer appear brown or yellow in contrast to the silver white aluminium.
Using this technique, it is possible to observe the freshly exposed aluminium alloy surface which progressively replaces the original brown surface during cleaning. In other words, it is possible to see gradual removal of the disturbed layer.
This optical approach has many advantages, including a relatively large sampling area compared with electron microscopy and the use of low-cost equipment. This is important for a fast, quantitative analysis of the coverage of the disturbed layer on rolled aluminium sheet surfaces. No specific sample preparation is required other than degreasing the sample surface with solvent. Furthermore, a relatively low level of expertise is required to perform the observation and the data collection.