Spotlight: How to carry out image analysis for steel quality control
The latest Olympus Stream software helps to determine the non-metallic inclusion content in steel.
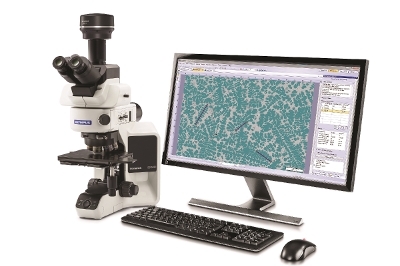
Non-metallic inclusions are chemical compounds and non-metal materials embedded inside steel during the manufacturing process. Inclusions have a different chemical origin and give different mechanical properties to steel, such as formability, toughness, machinability and corrosion-resistance.
As a general rule, the fewer or less severe the inclusions, the higher the quality of the steel. Therefore, analysing and documenting non-metallic inclusions is an important requirement for quality control.
Olympus Stream software helps steel manufacturers manage and maintain quality during manufacturing. The latest version has improved image analysis, resulting in a greater ability to measure and rate non-metallic inclusion contained within high-purity steel.
Smart stream
Stream software is suitable for analysing all high-purity steel such as special and controlled dilation steels, as well as treatments including roll bearing.
The software provides intelligent step-by-step workflows to help evaluate images for quantitative measurements and professional reporting. With Olympus Stream, users can conduct complex image analysis tasks with flexibility - the software has a broad scope of functions to enable fast, precise observations on a variety of samples while maintaining data security and reliability.
Optional solutions enable users to adapt the software to their application, including quality analysis, research and development, process development and quality control.
The new non-metallic inclusion content solution detects and classifies individual fields on a large scan area, expanding on the software’s capabilities to detect and classify individual inclusions in worst field mode. The setting provides statistical results of inclusion content on the entire scan area according to three international standards:
The inclusion content mode provides statistical results of this selection on the entire scan area according to three international standards: ASTM E45-18 (method D), ISO 4967:2013 (method B) and EN 10247:2017 (method K).
Rating non-metallic inclusion process
Non-metallic inclusions in steel can be accurately, repeatedly and easily detected using Stream image-analysis software.
After correct sample preparation, non-metallic inclusions can be observed directly on the surface of a given steel sample using a compound microscope – either an upright or inverted model – that is capable of reflected-light, brightfield conditions. Inclusions are easy to observe and analyse due to their high contrast ratio, as they appear dark on the bright, highly reflective background of polished steel.
Morphological parameters differ between inclusion types, i.e. globular oxide and silicate, as do their grayscale values, i.e. alumina and sulphide.
Digital analysis
In North and South America, ASTM E45 is the dominant standard for non-metallic inclusion analysis in steel.
Quality control laboratories used, and continue to use, the ASTM chart comparison method to analyse inclusions. With this method, operators perform a visual estimate of the inclusion type and severity by comparing a live image under an optical microscope against a micrograph chart, often posted on the wall near the microscope.
Prior to the advent of digital imaging, the magnification criteria specified by the standard was that inclusion ratings be performed with a compound microscope at 100 × total magnification (10 × objective lens and 10 × eyepieces).
However, this was updated to accommodate the growing trend in digital image analysis, stating that a resolution of 1.0μm/px or better is required when using a 10 × objective lens.
Digital image analysis is now the preferred methodology because of its superior accuracy and repeatability, helping eliminate the risk of subjectivity introduced by the human eye. Furthermore, documenting the analysis results is seamlessly integrated into the workflow.