Spotlight – How to use piezo actuators for microscopy
Physik Instrumente (PI), Head of Segment Marketing for Microscopy and Life Sciences, Dr Thomas Bocher, explains how piezo actuators can help deliver better quality inspection.
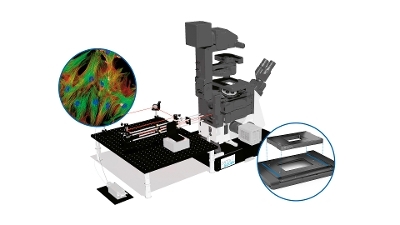
Super-resolution microscopy (SRM) allows researchers to non-destructively investigate structures in previously unattainable detail, at a molecular level. During the past two decades, advances in the field have led to significantly higher resolved images, faster processing times and further insight into the functionality of molecular machines within cells. Nanometre precision positioning has been a major enabler for rapid advances in this field.
Unlike other methods offering comparable resolution – such as scanning electron microscopy (SEM) – SRM can also be used to investigate metabolic interactions in living cells. Nanometre precision positioning has been a major enabler for SRM, and its rise in popularity has prompted many laboratories to revisit imaging-based research in applications that had been hindered by diffraction-limited image resolution.
The first SRM instruments were built in academia by physicists using standard parts from other microscope platforms. The ability to position samples and objectives accurately was key and, as piezo-based positioning systems were already commercially available and had a proven track record across multiple microscopy disciplines, they were the natural choice for the first generation of SRM platforms.
Piezo power
Piezoelectric actuators have long been considered the gold standard for the fine positioning of both sample stages and objectives in a broad range of microscopy techniques. Their main advantage is that movement is controlled by converting electrical energy into mechanical motion. In theory, the piezoceramic material itself has unlimited resolution, allowing precise, stable and reproducible fine positioning down to the sub-nanometre range, and typical travel ranges between 10 and a few hundred micrometres for linear actuators. As piezo materials have no moving parts, the resulting motion is friction free and not subject to wear, reducing maintenance and making them capable of several billion cycles without measurable changes in their behaviour.
Piezo actuators offer rapid response times – down to a few microseconds – and acceleration rates of more than 10,000g, very fast start and stop behaviour, and velocities to several hundred millimetres per second. Many of the latest generation piezo flexure actuators combine 0.5 nanometre (nm) precision with long travel – up to nearly 500,000nm in some cases – and rapid settling times of less than 20 milliseconds, making them ideal for fast scanning and high throughput. Conversely, piezoceramics can also be used to provide high-resolution motion at a low, constant speed – down to single encoder counts per second – in combination with suitable control and regulation processes.
Piezo actuators are used for three main applications in SRM – Z-positioning of objectives for autofocusing, manipulation of illumination systems such as in light sheet and 4Pi microscope techniques, and positioning of sample stages. Each of these applications has unique requirements in terms of travel range, reproducibility and settling times but, in general, system integrators want piezo-controlled movements to be as rapid, precise and stable as possible.
Piezo testing
Total internal reflection fluorescence microscopy (TIRFM) is a comparatively simple and inexpensive method that benefits greatly from piezo-based solutions. For this technique, a laser beam hits the glass surface of a microscope slide, microplate or Petri dish at a total internal reflection angle to stimulate fluorescence. Because the electromagnetic field of this beam only penetrates the sample on the other side of the glass plate to a depth of 100–200nm, the stimulated area in the Z-plane is reduced, offering better Z-resolution than standard wide field or confocal fluorescence microscopy. Piezo solutions precisely position the lasers and Z-drive within this system.
Similarly, light sheet fluorescence microscopy uses a unique planar illumination approach, orthogonal to the observation direction. This minimises photobleaching and phototoxicity for living specimens, allowing 3D and live cell imaging of large specimens over time. Piezo-driven stages and objectives are used here to position small organisms to within a few millimetres with a bidirectional repeatability of 100nm.
Super-resolution microscopy is driving rapid advances in our understanding of many molecular structures and interactions. The latest generation SRM systems are achieving spatial resolutions of around 20nm, and the sub-nanometre positioning precision offered by current piezo-based drives will help to increase this resolution even further. Despite this, microscope integrators have been demanding longer travel ranges, greater stiffness and higher speeds since the construction of the first SRM systems, and the development of customised solutions to meet this growing demand will be vital as fluorescence microscopy pushes further into the nanodimension.