Solid-state batteries
Ilika Product Commercialisation Manager, Denis Pasero, discusses the prospects of solid-state batteries in electric vehicles with Anthony Caggiano.
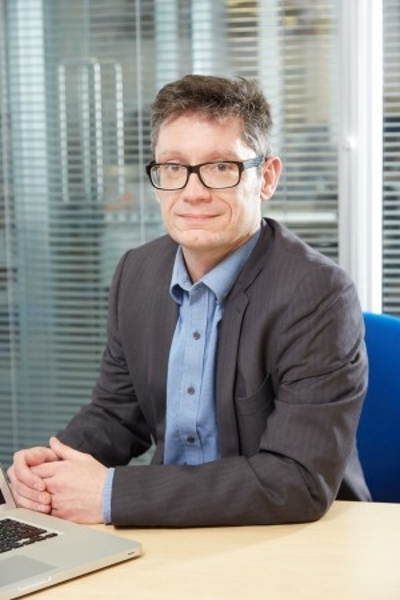
Battery developer Ilika, UK, has received funding for three projects as part of the Faraday Battery Challenge - a government initiative to invest in research, innovation and new sites to advance the production, use and recycling of batteries.
While the programme’s main focus is on electric vehicles, the outcomes will help battery development in other applications. The initiative comes as part of the government’s plan to ban new conventional petrol and diesel vehicles by 2040, to be replaced with electric and zero-emission vehicles. The government estimated that by 2025, the UK battery market could be worth £5bln, and the EU £50bln.
Ilika’s programmes in the challenge come under the Goliath project, which aims to develop a solid-state lithium-ion battery for a range of electric vehicles.
Its most recent project to receive funding is called Granite, which includes collaboration with Jaguar Land Rover (JLR), Warwick Manufacturing Group (WMG) and AGM Batteries. Announced in September 2019, it will explore cost-effective routes for scaling up the company’s solid-state technology. JLR will develop the new battery pack designs to fit within its future electric vehicles, and WMG will add its skills in abuse modelling and cell performance evaluation.
The PowerDrive Line project, in partnership with engineering and environmental consultancy Ricardo and others, is the longest-running project, and received funding in 2018. It will develop a lithium-based solid-state battery for plug-in hybrid and EVs, and establish a pre-pilot line for cell technology and processes for a solid-state materials supply chain. The consultancy will design and construct a prototype battery module to demonstrate its potential in-vehicle performance. Ricardo will apply its expertise in EV battery management systems (BMS) technology, which it will develop to enable a capability for super and ultrafast charging at ratings of 50-350kW.
The second project is MoSESS, led by McLaren Automotive, which will develop batteries for high-performance vehicles, with the aim of creating a fast-charging and high-power battery system based on advanced cell technology from Ilika and A123 Systems. It will deliver a simpler cooling system and an optimised crash structure for the battery, as well as reduced charging time and weight. WMG will also be involved.
Pasero said Ilika has partnered with many consultants to help drive the development of packs – here he discusses the technology, and where it might sit in the landscape of automobiles.
What are the benefits of solid-state batteries?
I think it is the safety aspect of these batteries. The difference between a solid-state battery and a conventional lithium-ion battery is the electrolyte – the section between the cathode and the anode, which is solid in the case of the solid-state battery.
In a conventional lithium example, the electrolyte is a liquid that may heat up, have electrochemical reactions, gas evolution, and possibly explode. I think the interest for solid electrolytes is that they do not do these things, so there is a safer solution, especially in an electric vehicle. The big worry for electric vehicle manufacturers would be a catastrophic event, which means the recall of a whole fleet. With solid-state batteries, that would not happen.
As people started developing and looking at them technically, they found other advantages. The liquid electrolyte in lithium-ion batteries is great for conduction, but this is also the component that will limit a battery’s lifecycle – those electrochemical reactions between the anode, cathode and electrolyte. The solid-state battery electrolyte is more stable, so we expect a longer life and less degradation over time.
Finally, the energy density of lithium-ion batteries is going up every day. There is lots of progress on increasing it, but there is an understanding that there will be a third theoretical limit, in terms of energy density for a lithium-ion battery, for conventional ones, that is likely to be more like 300-350w/kg.
To go above that, you need to look at alternative chemistries like lithium sulphur perhaps, or maybe lithium metal anodes. Solid-state batteries have a much higher theoretical limit in terms of energy density.
What is the main structure of a solid-state battery?
In a way, you will find there is not very much difference at all in terms of the cathode and the anode – the chemistry is very similar. These are films of lithium, cobalt, manganese, nickel, oxide in the cathode, and maybe silicon or carbon in the anode. So the same materials and the same chemistry and the same processes, really.
The main difference is the component in the middle that makes the conduction of the electrons impossible through a kind of barrier, and the conduction of lithium ions through the electrolytes. In the lithium-ion battery you have a polymer or plastic separator, so that there is no short between. This is replaced by a film of ceramic materials. So you have a structure that is totally solid. You get a film of cathode, then a film of electrolytes, and on top of that a film of anode. That is a simplification, because those layers slightly go into each other so you have good conduction.
What materials lend themselves well to solid-state use and still achieve good performance?
There are nuances. There is belief that high nickel content in cathodes could be more helpful in solid-state batteries than conventional lithium-ion batteries. Those high lithium nickel oxide type materials would be used in a more stable and safer way in solid-state batteries. These provide higher power, typically. But there are limitations with using them in conventional lithium-ion batteries in terms of their stability, so that would help a little bit with power.
The key chemistry answer is what materials are in the electrolytes. People often use the words solid-state batteries for a range of chemistries. People will use these words to describe an electrolyte, which may be a polymer, or a polymer composite with some glassy elements in it, or a material that is typically a dense ceramic film.
In terms of the ceramic contents, there are two types – an oxide and a sulphide. The sulphide type appears to have the highest ionic conductivity and therefore could help with power, however, the sulphide materials may, under some conditions, create toxic and dangerous gases, like H2S, a sulphuric acid. So manufacturers of this type of electrolyte material will need to have a lot of safety aspects related to these batteries.
The oxide type, which is what Ilika is working on, is elysium metal oxide, which is safer and the team is trying to make it as conductive and high power as possible.
How can solid-state batteries be managed at end-of-life?
For electric vehicles, there is thinking that batteries which may have lost some percentage of their capacity could be reused, for example for domestic stationary storage, so the devices that store energy from solar cells mounted on roofs.
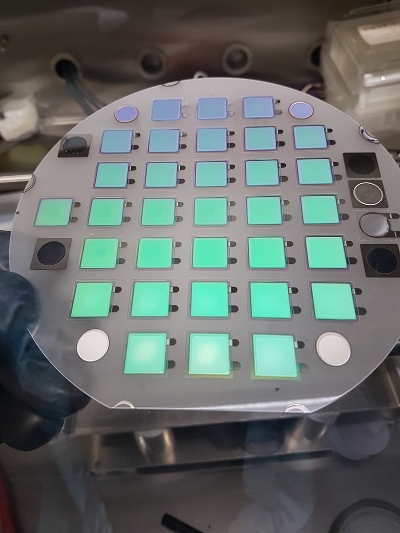
For environmental impact, there is a school of thought that the liquid electrolytes, with all those possibly toxic materials, are not present in a solid-state battery. So you will not have this problem when trying to recycle these toxic materials. In terms of reusing the materials from solid-state batteries, I think there is still quite a lot of work to understand what could be done – whether these could be recycled, or whether they would just have to be incinerated.
What packaging issues can solid-state batteries solve in an automotive situation?
In terms of packaging at the cell or pouch cell level, it is likely that solid-state batteries will require less packaging, as there is no liquid. Conventional lithium-ion batteries have a liquid that needs to be safely contained in the packaging, which also helps with avoiding water or oxygen or anything going inside the pouch and damaging the liquid electrolytes. So there is significant packaging required for that safety aspect of the device.
The batteries will have higher energy density, so either you get a lighter vehicle for the same power and energy, or you can fit in more power for the same volume.
How do you think solid-state batteries could improve charging times?
In the last six years, we have been working on solid-state batteries at a very different scale. The work has involved developing micro solid-state batteries – these are extremely small batteries, of the millimetre scale, that we integrate into Internet of Things sensors or medical implants, for example, devices that need to be really small. And we have developed those batteries using solid-state battery materials and processes that are adequate for the task.
At that scale, we found that solid-state batteries have a much superior rate capability and power density than conventional lithium-ion examples. This gave us hope that this could scale up to batteries that achieve amp hour and tens of amp hour levels. That is quite a few orders of magnitude higher, which remains to be seen. What dominates the power aspect of cells is the ionic conduction through the electrolytes, and liquids are usually better than solids.
There is still work to be done for solid-state battery manufacturers to use tricks like choosing a material that is very well mixed. Regarding the electrolyte, this would be something that would work with the cathode and anode. Power may be improved, so there is possibly a higher rate to be obtained, but there is still some work to do.
With the rise of transport apps and an increase in short trips, is range anxiety warranted?
I think range anxiety around electric vehicles rises from the early generations, where this was a problem. But even conventional lithium-ion batteries are rapidly increasing their energy density. Their ranges are getting higher to the extent that, in general, for a person using a car, just travelling to work in the morning and returning in the evening, or doing short distances in an urban environment, there is no such problem of range, really, for most people.
If we look at models for driving attitudes in the five to 10 years to come, with this shared ownership model, where somebody does not own their car, but just borrow it to go into work, and then the car goes, somebody else will use the vehicle. Here, it is not really a question of range anxiety, it will be a question of charging very fast between one user and the next, so rapid charge will be important.
And also, very long lifecycle. Because in that scenario the vehicles are being used much more efficiently and being recharged many more times. So, there could be a change in attitude. Battery developers using these types of materials need to think, ‘what is the battery that we really want to be developing?’. It is not the battery for today, with today’s driving attitudes, it is the battery of five to 10 years time, where driving attitudes might change.
What materials have you been looking at?
We are at very early stages with our projects, so I can only speak broadly. In terms of cathodes, we are trying to push the boundary towards higher nickel content, because that would provide higher energy and power density.
In terms of electrolyte materials, we have proprietary materials. At the moment, we are concentrating on oxide, lithium, and metal oxide types of electrolyte, which have a higher safety aspects than the sulphur. We have a lot of knowledge in using silicon, at the anode. So, this is part of a library of materials that we are using.
What are the next steps for the Faraday Challenge?
Step number one is successful delivery of three high-level projects with high-level partners –we want to develop the batteries and deliver them to our customers. What is important for Ilika is understanding the next step, in terms of commercialisation and production. This is what we are working on through the Granite project. Also, talking to partners via Innovate UK and trying to understand how we can scale up this technology.