Solid fuel compositions from mixed solid waste
Dr Tahsin Ali Kassam at UDL Intellectual Property discusses a recently granted patent relating to forming a solid fuel composition from mixed solid waste.
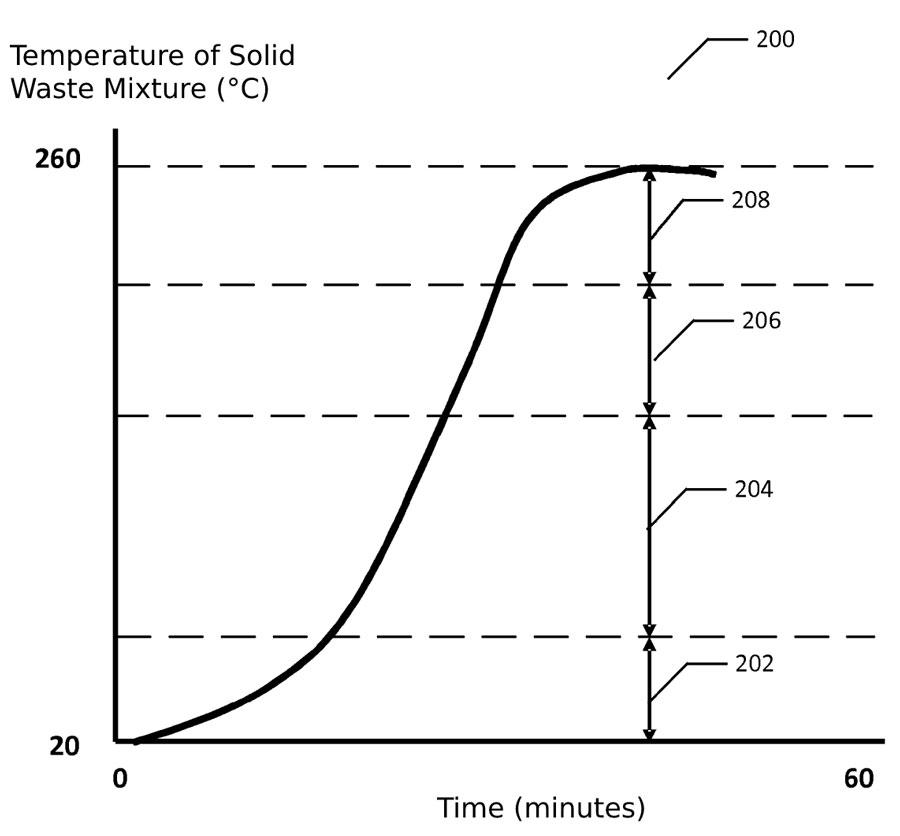
Pyrolysis and gasification are thermal treatments used in waste-to-energy processes for releasing energy in solid waste streams. However, most plants tend to incinerate the solid waste stream due to its inherent low density and variable composition. For example, municipal solid waste such as organic material, household waste, plastic, or agricultural waste can have high-water content, low density and lack of homogeneity.
Pelletised solid waste can retain this variation in composition and may fail to transform the waste into a high density and low moisture fuel appropriate for the efficient operation of a pyrolysis or gasification chamber.
In December 2020, Ecogensus LLC was granted European Patent, EP3212741B1 designating the UK, titled Process for forming a solid fuel composition from mixed solid waste.
The patent claims a method of producing a solid fuel composition from a solid waste mixture without the formation of syngas. It comprises heating a solid waste mixture, including between ~5-60wt% mixed plastics within a process vessel to a temperature no greater than ~110°C to separate the solid waste mixture into a dried solid waste mixture and vaporised compounds.
Prior to introducing the mixture into the process vessel, there is also an option to sort and blend solid waste and mixed plastics to form a mixture and subsequent shredding of it.
The next steps include removing the vaporised compounds from the process vessel, followed by heating and mixing the dried solid waste mixture to at least 160°C and below atmospheric pressure to form a heated solid waste mixture comprising melted mixed plastics.
The method then proceeds to extruding the mixture with a temperature of ~100-260°C to produce an extruded solid waste mixture; and finally, cooling it to less than ~65°C to form the solid fuel composition – having an energy content ranging between about 18,608kJ/kg (8,000BUT/lb.) and about 32,564kJ/kg (14,000BTU/lb.); a density ranging between about 481kg/m3 (30lb./ft3) and about 1,282kg/m3 (80lb./ft3); and a water content of less than ~1wt%.
The mixture is processed in a vessel below atmospheric pressure, driving away excess moisture, volatile organic compounds (VOCs), chlorinated organics and chlorine gas, which are sequestered without exposure of these gases to the atmosphere.
A typical temperature profile (200) of the solid waste mixture in the process vessel is depicted in the figure opposite. At a first temperature range (202), it is heated from an initial ambient temperature to ~100°C. Moisture and other volatile compounds within the solid waste mixture may be separated, vaporised and released as a mixture of vaporised compounds. For example, at ~190°C, chlorinated organic compounds and chlorine gas may be liberated from the waste.
As the temperature increases above ~200°C in the second temperature range (204), various organic compounds may be broken down. With the release of steam and other vaporised compounds, the mixture may also be sterilised.
In the third temperature range (206) from ~200-240°C, various volatile compounds may be liberated from any plastics included within the solid waste mixture and released as additional vaporised compounds, in addition to any steam that may continue to be released. For example, chlorine may be released from chlorine-containing plastics such as PVC.
As the temperature further rises above ~240°C in the fourth temperature range (208), plastic material is melted and ad-mixed with the other constituents of the solid waste mixture – thereby distributing the plastic throughout and forming a high-density solid fuel composition. The composition may form a homogenised, dry, dense and energy-rich fuel primed for high-efficiency pyrolysis or gasification. Read the full patent here: bit.ly/3q8THf3.