Slowing down from fast fashion
How can we design more sustainable textiles and move beyond the trend for fast fashion? Dr Celina Jones MIMMM, at The University of Manchester, UK, gives us the lowdown.

In November 2022, the UN Sustainable Fashion Strategy highlighted that the fashion industry was responsible for 4% of global carbon emissions. A proportion of these emissions was linked to the cultivation, harvesting and transportation of the raw materials used to produce textiles. The authors note that the application of colourants and performance finishes pollutes primary waterways in countries manufacturing these materials.
These issues are magnified by the doubling of fashion consumption in the past 15 years, highlighted by the Ellen MacCarther Foundation, fuelled by shorter fashion trend cycles and the continuing adoption of a ‘take-make-waste’ linear model.
Additionally, prior to disposal, laundering and aftercare of fashion items have been attributed to global carbon emissions along with ocean microplastic pollution.
In this piece, we begin to highlight current and future challenges for the industry, as the word ‘sustainable’ centres around a process that has minimal impact to the environment and is able to be maintained over a significant period of time. The UN Alliance for Sustainable Fashion extends sustainability to encompass social issues and working conditions.
Where to begin?
Due to the breadth of the supply chain, in terms of scope, location and range of processes involved in producing textiles for fashion, it can be a challenge in itself to know where to begin to address these issues, and indeed the discussion.
Let’s focus on the raw materials used to create our textiles. Currently, the two fibres dominating global fibre production are polyester, followed closely by cotton.
Natural fibres such as cotton, wool and flax have been used for thousands of years in the production of textiles for clothing. Derived from plants and animals, they are cultivated and reared in different climates and countries around the globe. Different varieties of cotton and breeds of sheep produce natural fibres with varying performance, aesthetics and quality. In a global supply chain, provenance is one of the first challenges for fashion brands where quality is key. Furthermore, the need for vast amounts of land, water, pesticides, insecticides and manual labour for various parts of the cultivation and rearing process, presents a variety of challenges relating to climate change, working conditions and impact on the local environment.
For this reason, according to The Global Preferred Fibre Market report in 2020, by the Textile Exchange, there is growing preference for virgin cotton fibre production associated with Fairtrade, Fairtrade Organic, Better Cotton Initiative and Cleaner Cotton.
There are also developments in genetically modifying cotton to have insect and pest-resistant traits, and researchers have explored modification of colour to reduce pollution associated with finishing of cotton fashion goods. With an aim of reducing global emissions associated with cultivation, harvesting and transportation of cotton fibres, GALY (winner of Global Change Award 2020) has produced lab-grown cotton without the need for specific growing conditions or climate.
To have a better understanding of the future challenges faced by the fashion industry, in 2015, global luxury group Kering – which includes brands such as Gucci, Saint Laurent, Bottega Veneta, Balenciaga and Alexander McQueen – published a report titled Climate Change: Implications and Strategies for the Luxury Fashion Sector. It highlighted climate change risks associated with six luxury raw materials and an agenda for the future, aimed at providing resilience for the sector.
The report identified the impact of climate change on the quality and availability of these raw materials in the future, including the increase in temperature causing a rise in pest and diseases for cotton crops, through to the degradation of habitats and reduced winter hair growth in goats providing cashmere fibres.
While natural fibres present challenges associated with cultivation, harvesting and transportation, they are obtained from a natural resource and, when considering end of life, they are biodegradable.
Some brands and designers have highlighted this as a favourable choice of fibre, often contrasted against the current dominant fibre in the global market – polyester.
Despite deriving from a depleting resource, fossil fuels production is predicted to continue to grow by 2030, according to The Global Preferred Fiber Market report. This man-made manufactured fibre can be ‘tailored’ for use across fashion apparel, athleisure, sportswear and outdoor clothing. It can be blended with fibres such as cotton, for example, to produce easy-care products. The range of products, versatility, cost and performance of this fibre may be the reasoning behind its growth and popularity in our wardrobes.
Nature is natural
As we look to find a more ‘sustainable’ future for man-made manufactured fibres, there is a rise in popularity for exploring alternative feedstocks, sourcing from natural polymers and expanding the use of pre- and post-consumer waste.
While viscose rayon – an alternative to silk derived from wood pulp – is the most dominant man-made manufactured cellulosic fibre on the global fibre market, environmental issues have been highlighted associated with the feedstock and production process. It has resulted in groups such as Canopy developing the CanopyStyle Audit Guidelines, to help verify that the wood feedstock has not been sourced from endangered forests, for example.
Other regenerated cellulosic fibres such as lyocell and bamboo viscose have received increased interest from fashion brands using alternative feedstocks, such as wood pulp from eucalyptus trees and bamboo. In the case of lyocell, a non-toxic solvent is recycled in the closed loop production process.
Companies such as Lenzing have included the use of cotton scraps in the production of RE:FIBRA via the lyocell process, to help minimise waste and increase circularity.
As we reflect back on the early 20th Century, at a time when viscose rayon was developed in the pursuit for a man-made alternative to silk, we continue to look to nature for inspiration to resolve the challenges of the future.
Biomimicry has been explored by textile designers through a variety of different approaches to help overcome current and future challenges. Some have looked to the nanoscale structures of plants and animals to help address some of the challenges mentioned (see box-out below).
It can also be witnessed through the continued, renewed pursuit of poromerics (leather-like substitutes), but through natural resources rather than, historically, synthetics. A variety of approaches are being explored, highlighted in a recent review article in Nature by Jones et al, Leather-like material biofabrication using fungi as an alternative to bovine and synthetic leathers (also see article on p39 on nanocellulose bioleather).
It is important to note, that while these leather substitutes may be created straight from the raw material, the majority of textiles for fashion applications require woven and knitting technologies. At each stage of the production process, colouration and finishes also can be applied to the textile, which typically require the use of vast amounts of water in their production.
It is therefore easy to see how when designing sustainable textiles materials, there are a great deal of challenges in the manufacturing process alone.
Taking inspiration from nature
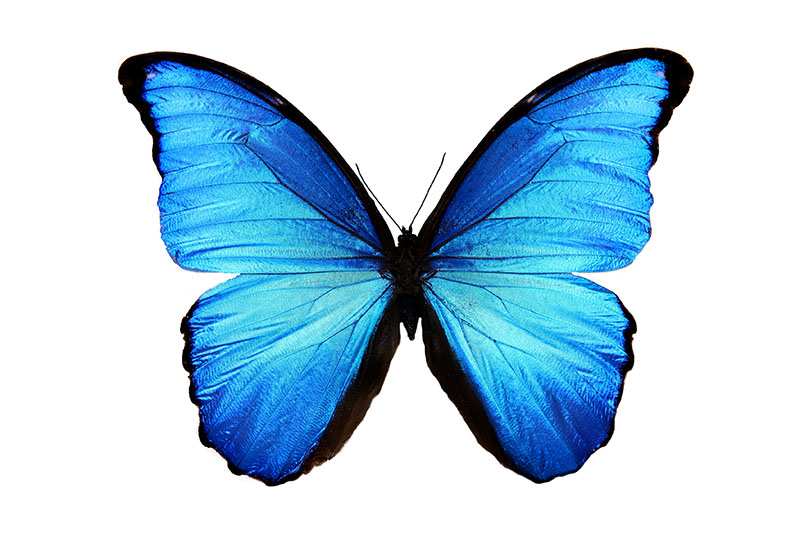
There are many examples of how nature has inspired the textile industry:
- Self-cleaning textiles that mimic the surface and self-cleaning properties of a lotus leaf.
- The use of structural colour as an alternative to traditional dyes and pigments in the pursuit of removing the dye kitchen from the textile supply chain.
- The development of the Morphotex fibre by Teijin fibres, mimicking the wing surface of the blue male Morpho butterfly. The fibre core is composed of 61 alternate layers of nylon 6 and PET, covered in a polyester sheath. The multilayer interference core is responsible for the iridescent appearance of the structually coloured fibre. By manipulating accurately the thickness of the nylon 6 and PET layers, a range of colours may be achieved.
Where does it end?
For some, the immediate challenge is tackling the large amounts of waste generated. According to the reports, globally more than half of all fast fashion is disposed of within the same year.
The Ellen MacCarther Foundation has put forward the suggestion of the fashion industry taking a circular approach (see article on p36 on circular design in fashion).
This approach sees parallels with the design framework published in 2002 by William McDonough and chemist Michael Braungart in their book Cradle to Cradle: Remaking the Way We Make Things. They presented the benefits to society from adopting the circular economy and eliminating the concept of waste.
For some, this can be achieved through recycling practices, whether that be fibre, fabric or garment recycling through mechanical or chemical processes in an industrial cycle. Yet others have highlighted that often this results in downcycling – producing a product of lower value and quality than the original product.
As highlighted previously, many textile materials contain a blend of natural and synthetic fibres, providing challenges in separation and uses for the output materials produced.
To overcome these obstacles, industries previously working in silos could come together to rethink its approach.
GR3N, an EU Horizon 2020 project for example, has explored the potential of chemical recycling PET plastic waste, and bringing together PET bottle manufacturers with fashion high street brands. In this approach, PET bottle manufacturers would see these brands as raw material providers.
While zero waste and circularity should be considered throughout the textile supply chain and when producing new fashion products, there is also a growing emphasis to consider reuse and repairing of those in circulation. For many researchers in this field, a statement commonly used is that the most sustainable garment you have is the one already in your wardrobe.
When referring to reuse this can be through renting, swapping, donating and repairing garments, removing the need for further natural resources to make new a product. Designing and producing better quality products would support recycling practices and also allow the possibility of extending longevity.
In 2008, Kate Fletcher highlighted in her book, Sustainable fashion and textiles: design journeys, the use of terms such as ‘slow’ and ‘fast’ in fashion and textiles, and considerations to local production (see box-out ‘Did you know’ below).
Fletcher highlights that sourcing locally not only mitigates transport emissions, but also encourage economic resilience and further addresses some of the social and working issues surrounding sustainability.
In the UK, The Sustainable Clothing Action Plan 2020 was developed in collaboration with clothing manufacturers, charity retailers and recycling companies with the aim of reducing the environmental impact of carbon, water consumption and waste. This has driven the Textiles 2030 Waste & Resources Action Programme initiative, bringing together expertise in the textile and fashion industry to accelerate the move towards a circular economy.
This leads us to conclude that it is important for us to have a holistic approach, where designers, material and social scientists, and industry experts work together, to communicate the challenges we currently face and collaborate to cope with the issues we may encounter in the future.
Did you know?
In 2008, Kate Fletcher highlighted in her book, Sustainable fashion and textiles: design journeys, the use
of the terms ‘slow’ and ‘fast’ in fashion and textiles.
The term ‘fast’ refers to the speed of consumption and production of fashion items. ‘Slow’ design, production and consumption could help overcome some of the challenges the sector faces in becoming more sustainable.
Part of the ‘slow movement’ idea is ensuring that designers, and all of those involved throughout the fashion supply chain, understand the environmental impact of the raw materials they are sourcing, how these materials are created, what were the working conditions for these manufacturers and the damage to the local environment.