Skin inspires de-icing surface
Drawing from the layered structure of the human skin, for a more durable de-icing surface.
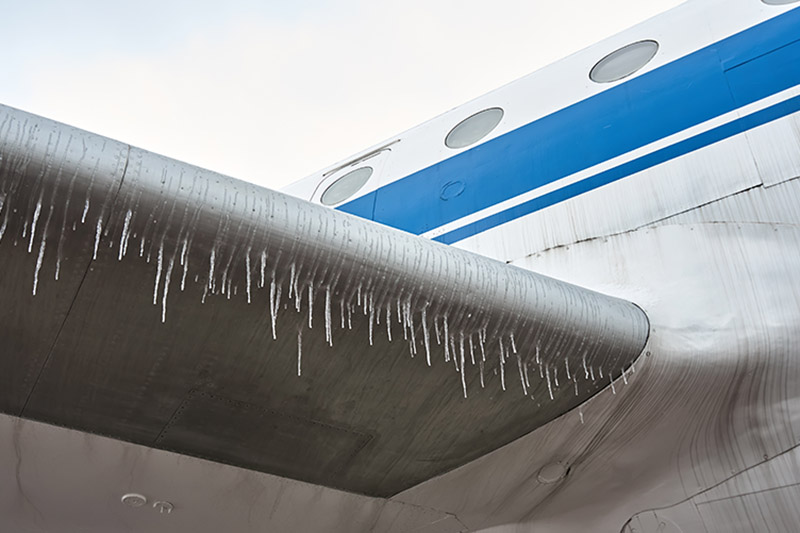
Surface icing presents challenges across industries, impacting the performance of aeroplane wings, wind turbine blades and high-voltage power lines. Ice accumulation not only disrupts normal operations but can also damage equipment.
Traditional anti-icing methods, though effective to some extent, often suffer from poor durability and reduced performance under extreme weather conditions, says a team led by Professor Xu Deng from the University of Electronic Science and Technology of China.
The researchers aim to combat this by mimicking the human skin, with its soft dermis and subcutaneous tissues covered by a protective hard epidermis.
A tough-skin de-icing surface is fabricated by combining a thin, rigid, top film with a soft substrate. This induces surface instability that generates extensive wrinkling at the ice-substrate interface and helps to distribute the interface effectively.
This design is said to mimic the skin’s natural response to external forces, allowing the ice to shed under its own weight without the need for external energy inputs.
A combination of large and small wrinkles enhance de-icing performance, according to the researchers. Large wrinkles reportedly initiate cracks at the ice edges, while smaller wrinkles accelerate crack propagation, ensuring complete ice detachment. They claim the ice adhesion strength is below 10kPa.
In the paper, A skin-inspired durable de-icing surface with boosting interfacial cracks in National Science Review, the researchers expand, 'To verify the universality of the mismatched-modulus strategy, we demonstrated the reduction of ice adhesion with multiple types of materials.
'Different kinds of micro-wrinkled tough-skin de-icing surfaces (TSDSs) were fabricated, including polyvinylidene difluoride (PVDF)-micro-wrinkled TSDS (elastic modulus of PVDF is 2.5GPa), polyethylene (PE)-micro-wrinkled TSDS (elastic modulus of [PE] is ~1GPa), polypropylene (PP)-micro-wrinkled TSDS (elastic modulus of PP is 1.14–1.55GPa), by using a hot press.
'The fabrication of micro-wrinkles on surfaces is well established, including methods such as thermal instability, hot pressing, photoinduction and solvent induction, many of which are suitable for large-scale production.'
Environmental tests have reportedly confirmed its robustness and versatility across many conditions, even after extended exposure to wind, rain and UV radiation. They claim this technology significantly reduces energy consumption and operational costs, making it ideal for long-term use in extreme weather.