Single-step alloy production
Metal extraction, alloying and processing have been merged into a single step by Max Planck scientists in Germany.
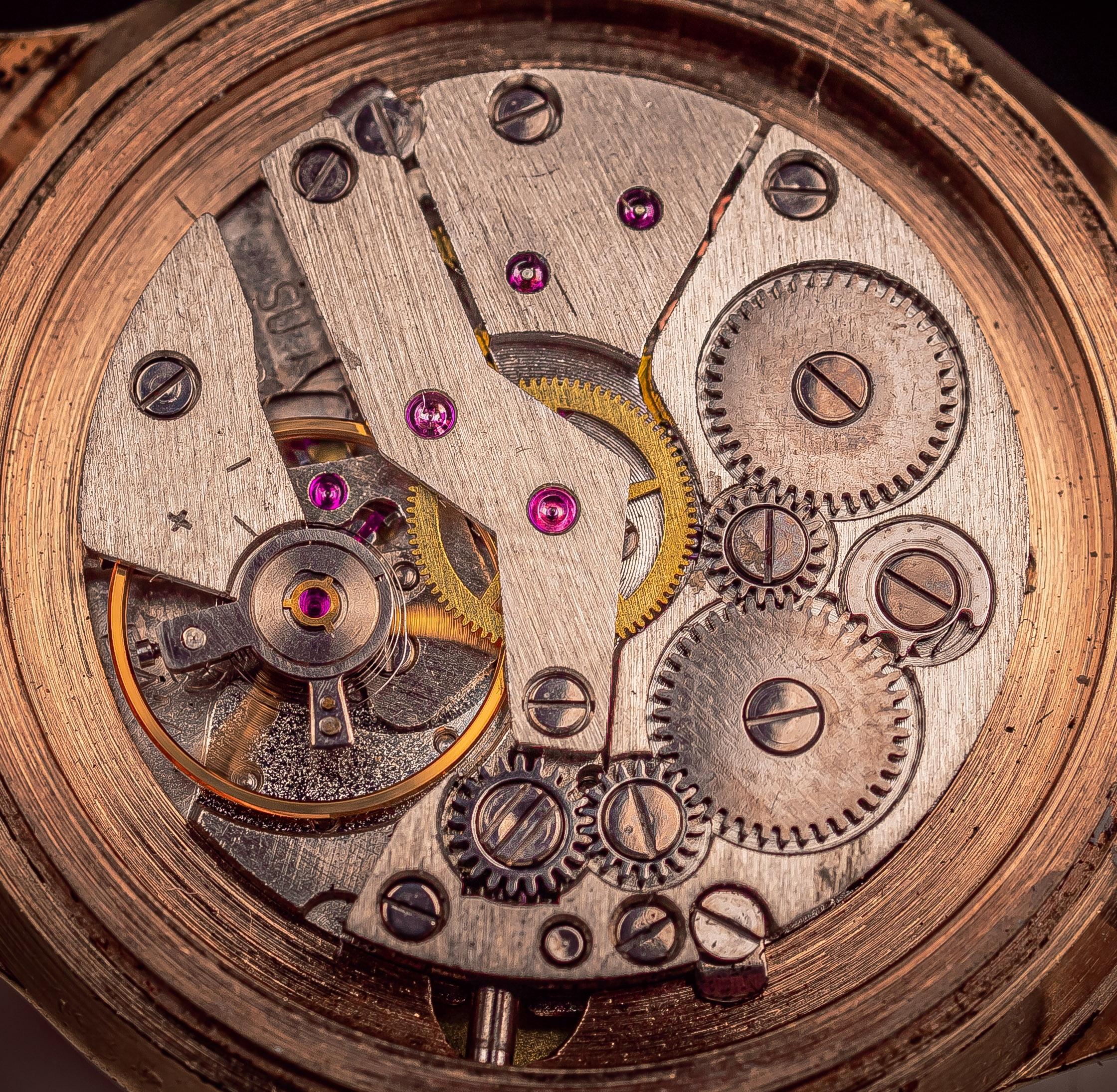
Unlike conventional methods, where ores are reduced using carbon to produce carbon-contaminated metals, the team’s method uses hydrogen as the reducing agent to produce Invar alloys.
Iron and nickel form the basis of Invar alloys, which are essential for sectors such as aerospace, energy, precision instruments and transport because of their low thermal expansion.
Conventional alloy production is a three-stage process, with intensive energy demands and carbon required at every stage. The ores must be reduced to their metallic form, then alloyed with liquefied elements and finally thermomechanically treated.
Dr Shaolou Wei, Humboldt Research Fellow at Max Planck Institute for Sustainable Materials (MPI-SusMat) and lead author of the study, says the team 'aimed to reform the millennia-old, multi-step, alloy-making process' in three areas:
- Eliminating CO2 emissions during fossil-reductant-based metal extraction.
- Reducing the energy cost of liquid processing that scales with melting temperatures.
- Exploiting the diffusion processes involved directly for compaction and bulk material fabrication.
The result is a single-stage method that, Wei claims, 'dissolves the classical boundaries between extractive and physical metallurgy'.
The alloys are bulk fabricated 'directly from oxides, merging the traditionally separated metallurgical processing of metal extraction, liquid alloying and thermomechanical processing in one single solid-state process step while also leaving no CO2 emission'.
Using hydrogen as a reducing agent instead of carbon has four key advantages, according to Professor Dierk Raabe, Managing Director at MPI-SusMat.
'First, the hydrogen-based reduction only produces water as a by-product, meaning zero CO2 emissions. Second, it yields pure metals directly, eliminating the need to remove carbon from the final product, thus saving time and energy. Third, we do the process at comparably low temperatures, in the solid state. Fourth, we avoid the frequent cooling and reheating characteristic of conventional metallurgical processes.'
To test the results, Wei reported, they 'analysed the microstructure across multiple length scales by means of scanning electron microscopy, electron backscatter diffractometry and atom probe tomography. We also opted for in situ synchrotron X-ray diffractometry, which enables time-resolved analyses of the governing redox and solid-state alloying mechanisms.'
The resulting Invar alloys are said to match the low-thermal-expansion properties of conventional Invar alloys, but also offer superior mechanical strength due to the refined grain size naturally inherited from the process.
However, using pure hydrogen will be costly for large-scale operations, while lowering the hydrogen concentrations requires an increase in temperature, which comes with environmental and financial costs of its own.
The team therefore needs to find the optimal balance between hydrogen use and energy costs, making the process more economically viable for industry.
And while the researchers used pure oxides for a proof-of-concept study, industrial applications would likely involve conventional, impurity-laden oxides. The process would need adapting to handle less-refined materials while maintaining alloy quality.
Wei identifies two further practical challenges for scalability – first, the effective removal of gangue oxides from natural ores through mechanical separation. Second, hydrometallurgical purification and the ability to achieve complete pore annihilation in mass production, which he says might necessitate overlaid hot isostatic pressing to improve the structural integrity of the final product.
If these are successfully overcome, however, the versatility of this one-step hydrogen-based process could impact further areas of metallurgy, eliminating the need for high temperatures and fossil fuels.
The team has identified production of high-entropy alloys and the transformation of metallurgical waste into valuable feedstock as future possibilities.