Sensing the force – a non-electric soft touchpad
A soft, silicone, non-electric touchpad could offer solutions in MRI machines, advanced prosthetic hands and movement aids used for rehabilitation post-surgery.
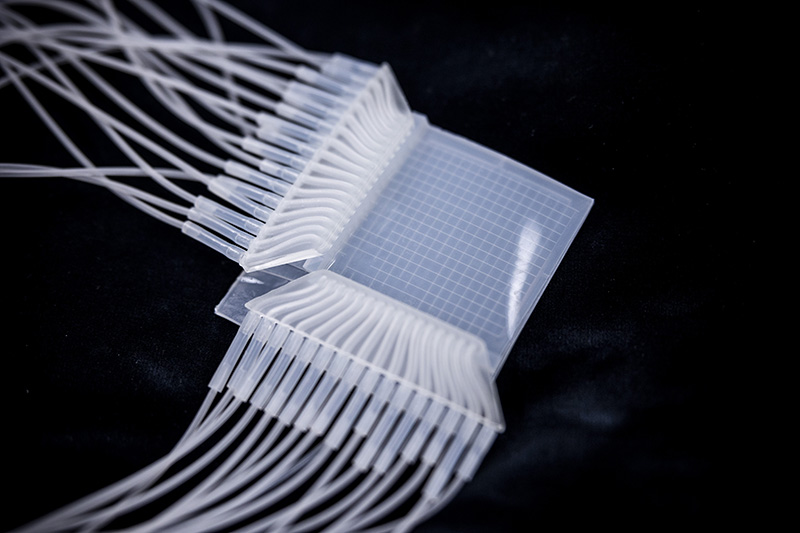
In what is claimed to be the first such device of its kind, data collected using its 32 pneumatic sensing channels could make it possible to eventually map the location, force and area of touch across its entire surface.
The touchpad’s precision means it can reportedly recognise handwritten letters on its surface as well as distinguish multiple simultaneous touches, say the researchers behind its development at Tampere University in Finland.
Doctoral researcher Vilma Lampinen explains how the team has fabricated the micropneumatic device by making a mould for the 32 channels – each measuring a few hundred micrometres wide – using the light-sensitive material SU-8 (a photoresist) to create a patterned surface coating.
Next, they poured liquid silicone elastomer into the mould, which cures to take shape. Once the elastomer has cured, it forms open-top channels. The researchers then stack three silicone layers on top of one another to form 16 horizontal channels, 16 vertical channels and a lid.
'The next layer acted as the lid for the previous layer, closing the channels from the top side,' Lampinen explains. 'The layers were bonded together using a thin layer of the same silicone elastomer as a glue.'
The touchpad has been mechanically tested using an exchangeable probe. 'The mechanical tester has a motor to move the probe up and down, and by measuring the fluid flow through all the channels, we were able to detect which of the channels were touched by the probe,' adds Associate Professor Veikko Sariola.
'The different probes we used included cylinders or spheres, of varying diameters. Additionally, we had an XY-table beneath the touchpad, so we could move the touchpad beneath the mechanical tester horizontally.'
By varying the force used to compress the touchpad, the probe’s diameter and the device’s horizontal position, the team confirms the non-electrical device can sense the force, area and location of contact.
Although the scientists note that the response time (50ms) and spatial resolution cannot compete performance wise with electrical sensors, they point to the advantages it offers in not containing any electrical components.
This means that, unlike electrical sensors, the touchpad could be used in high magnetic fields, for example, in MRI machines, or where there is strong radiation and even a small electrical spark could present a serious hazard.
'Electronic sensors may stop functioning in extreme conditions, such as in a strong magnetic field. Since the touchpad is not electric, a strong magnetic field does not affect it, which makes it ideal for use in devices such as MRI machines,' explains Lampinen.
In this context, the sensor technology could, together with the data produced by MRI images, guide a pneumatic robot during a scan and enable it to take a biopsy if a cancer tumour is detected, reports the team.
Alternatively, soft robotic hands could replace current prosthetic hands. 'Being soft, they are safer, lighter and potentially cheaper to manufacture. Touch sensors around the hand would also enable a more delicate grip,' adds Lampinen.
Before the touchpad can be manufactured at scale, the researchers say they must first improve the reliability of the device’s microchannels and better integrate its measurement pneumatics.