Rubber tyres using recycled carbon black
Dr Michael Ford MIMMM at Haseltine Lake Kempner explores a patent relating to rubber tyres using recycled carbon black.
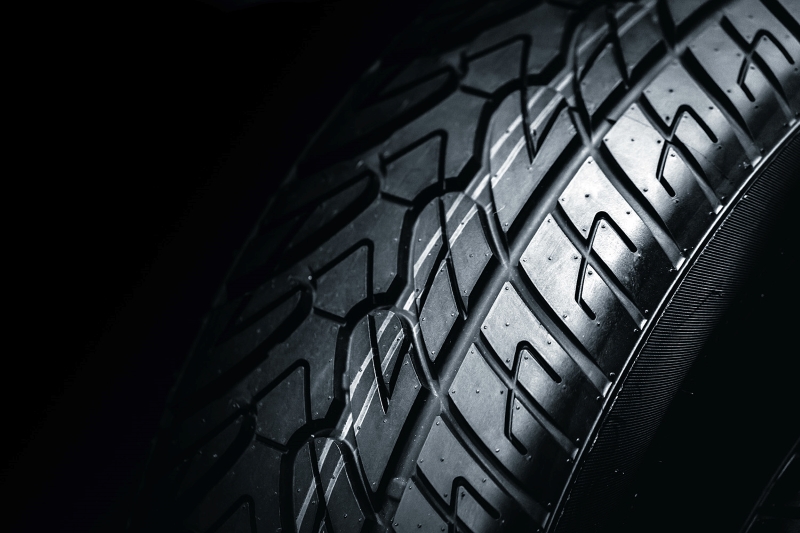
Vehicle tyres are commonly manufactured using synthetic elastomers, such as styrene-butadiene rubber, compounded with reinforcing particulate fillers. One such filler material is carbon black, which has been found to improve key mechanical properties of vulcanised rubbers including tensile strength and abrasion resistance.
Carbon-black-filled rubber tyres, however, present several environmental problems. For example, carbon black has typically been produced by the incomplete combustion of coal and coal tar, petroleum products and vegetable matter, and so a more environmentally friendly source of carbon black would be desirable. Used tyres containing carbon black are also often disposed of in landfill or by incineration, wasting valuable materials.
Efforts have therefore been made to improve the environmental impact of the tyre industry by recycling high-value components such as carbon black, which can be extracted from used tyres through a pyrolysis process. Pyrolytic carbon black (also known as CBp) accounts for more than 35% of the products obtained from pyrolysis of waste tyres, and could thus provide an important source of starting materials for the manufacture of new tyres.
Unfortunately, pyrolytic carbon black does not have the same physicochemical properties as non-recycled carbon black. In particular, pyrolytic carbon black particles tend to lack the surface functional groups that promote bonding with polymeric materials. This makes it difficult to use recycled carbon black as a filler material in new tyres or other rubber applications. Rubbers filled with CBp have been found to exhibit reduced abrasion resistance, tensile strength and moduli.
In March 2023, however, Bridgestone Corporation was granted European patent EP3173251B1 entitled Rubber compound for tyres comprising recycled carbon black.
This patent describes a rubber compound comprising a cross-linkable unsaturated-chain polymer base, carbon black, a silane bonding agent, and a vulcanisation system. A part of the carbon black used in the compound is recycled carbon black obtained by pyrolysis of tyres. The recycled carbon black has been treated to produce hydroxyl and/or carboxyl groups on its surface. The patent also describes a method of treating recycled carbon black to obtain the desired surface groups and a tyre portion manufactured using the rubber compound.
The surface-activated pyrolytic carbon black tested in the patent was obtained by an oxidation treatment involving exposure of pyrolytic carbon black to a solution of potassium permanganate (KMnO4) acidified to a pH of 1 using nitric acid. This process was found to form a number of hydroxyl and carboxyl groups on the surface of the carbon black particles.
According to experimental results included in the patent, use of treated pyrolytic carbon black with the hydroxyl and/or carboxyl surface groups, together with a silane bonding agent, produced a rubber compound that matched a reference compound (including only first-use carbon black) in terms of tensile strength, modulus at 300% extension and ‘bound rubber’ (a measure of the strength of the chemical-physical polymer-filler interaction which causes rubber insolubility when filled).
The measured resistance to crack propagation was also improved relative to the reference compound by adding treated pyrolytic carbon black.
None of the examples tested used pyrolytic carbon black (whether treated or untreated) as the sole filler material. Instead, all the examples included a significant quantity of first-use carbon black, with some of this first-use carbon black replaced by CBp, while maintaining the same amount of carbon black in total as measured in parts per hundred rubber (phr).
The experimental results appear to show that 20% of the first-use carbon black can be replaced with treated pyrolytic carbon black, while maintaining or improving the mechanical properties of the resultant rubber compound.
Interestingly, the benefits of using the treated pyrolytic carbon black were only achieved when this was combined with a silane bonding agent. In fact, the treated pyrolytic carbon black produced worse results than untreated pyrolytic carbon black when no silane bonding agent was present. The experimental results also showed that use of the silane bonding agent with untreated pyrolytic carbon black led to no improvement over the exclusive use of the latter.
Silane bonding agents are already commonly used in combination with silica fillers to facilitate the chemical interaction between the silica and the polymer base. Silane also interacts with silanol groups to inhibit the formation of hydrogen bonds between silica particles and the consequent formation of agglomerates, which can lead to inhomogeneous silica dispersions within the rubber compound. The silane bonding agent evaluated in the patent was Si75, also known as bis(triethoxysilylpropyl) disulphide.
The rubber compound tested in the patent was based on a 50:50 mixture of a natural 1,4-cis polyisoprene rubber and a butadiene rubber with a 1,4-cis content of at least 40%.
Read the full patent