Reusing and recovering industrial heat
Nina Webber and Judith Britnell, from the UK Department for Business, Energy & Industrial Strategy, describe outcomes from its heat recovery programme.
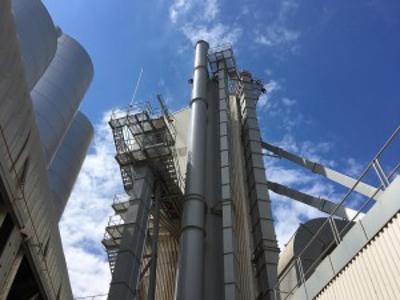
Waste heat can be used in many ways. This includes heating within the same industrial facility, converting it to power or feeding it into a heat network – helping businesses to grow revenue, lower fuel costs and cut emissions.
The UK Department for Business, Energy & Industrial Strategy (BEIS) launched its Industrial Heat Recovery Support (IHRS) Programme, specifically designed to encourage and support industry investment in heat recovery technologies across England and Wales. Support is given to businesses that take part by providing them with the chance to bid for a grant from a total funding pot, worth £18mln. This has helped to co-finance businesses’ efforts to identify and invest in opportunities for recovering and reusing heat that would otherwise be wasted.
The programme is split into two phases. Phase 1 conceptualises and defines the areas where waste heat could be reused and assesses business costs and benefits. Support is offered through grant funding, with the potential to receive 50% of the cost of a feasibility study and 30% of eligible costs for preliminary engineering. Phase 2 offers further grant funding of up to 30% of eligible costs for the project’s delivery, including detailed design, procurement, construction, commissioning, operation start-up, and monitoring and evaluation.
To date, the programme has approved funding for 32 projects covering sectors including food and drink, glass, cement, iron and steel, paper, plastics, chemicals and minerals products. These projects span 14 regions and cover 11 different types of heat recovery technologies all used in diverse ways. John Wainwright & Co Ltd, a vertically integrated construction materials business, is one such company.
Simon Lumkin, of Mines & Quarries Consultancy Ltd, based in Bristol, UK, says, ‘This project has shown that challenging industry assumptions, seeking transferrable technologies and exploring technical and engineering research can provide investment opportunities that would otherwise be dismissed.’
Reducing fuel demand and emissionsJohn Wainwright & Co Ltd is a vertically integrated construction materials business with a quarry, two asphalt plants, surfacing and civils engineering operations. It is headquartered near Shepton Mallet, Somerset, UK, at Moons Hill Quarry, with a satellite operation at Avonmouth, Bristol.
This case study relates to the asphalt production facility at Avonmouth, constructed in 2015. The plant includes a 19MW multi-fuel burner capable of using natural gas and gas oil that dries and heats aggregates as part of the process of manufacturing products for road construction.
The aim is to reduce fuel demand by ducting hot air from the site compressor exhaust and recovering heat from the plant exhaust with a heat exchanger to preheat the primary air supply to the burner.
The combined effect will reduce emissions by about 145t of carbon dioxide per annum. The site configuration is ideal for retrofitting the heat recovery equipment. The plant includes equipment monitoring for operational reasons and sub-metering has been installed to further enhance energy management.
A key factor allowing this project to progress was the grant provided via the IHRS programme, without which the project does not meet the company’s internal rate of return. Research undertaken for the feasibility study identified two key areas for heat recovery that would help to decarbonise the process, and support environment, social and governance benefits. The structure and rigour of the application process ensured client confidence along with learning outcomes likely to be applied elsewhere in the business. Phase 1 was for proof-of-concept and allowed for increased data acquisition and finessing design criteria for Phase 2.
Burner intake
Burners are known to operate more efficiently if the primary air is maintained within a consistent temperature range. Fuel savings can be made if this temperature is elevated within burner design parameters for efficient combustion. However, many asphalt plants are not enclosed in buildings due to cost, therefore key components, such as the burner, are exposed to the elements. For this project, measurements across the air intakes showed that distribution and velocity is very susceptible to crosswinds onsite.
The effect of wind and variable weather is believed to impact flame geometry and heating efficiency. Directing the compressor exhaust onto the burner air intake has provided the calculated minor improvements, although monitoring through the winter months is required. Measurements show that the compressor exhaust emits 5,000m3/hr (which was higher than expected) at around 45oC, reducing slightly once ducted to the burner. Calculations from the initial data acquired indicates at least 50MW per annum is being transferred from the compressor exhaust to the burner. The burner operates at a range that generally requires 15,000-20,000m3/hr of air, so providing around 25% of the air intake at elevated temperatures will be beneficial.
The Phase 2 objective is to ensure all burner input air temperature is elevated to 40-50oC. Phase 2 includes enclosing the burner to eliminate weather effects and to improve the equipment’s longevity.
The technical concept of diverting the compressor exhaust along with the associated energy benefit calculations was well understood, but not applied at asphalt plants. Enlarging the exhaust has improved compressor cooling. Additional flow measurements within the main plant exhaust, undertaken during Phase 1, were complicated by the high vapour content, but the reproducibility of the data was improved by ensuring the temperature of the pitot tube could equalise with the exhaust flow before measurements. Beneficially, this led to further evaluation of the vapour quantity by volume in the exhaust and calculations on the amount of precipitate expected because of implementing Phase 2. This provided confidence that the volume of precipitate could be used elsewhere in the process limiting the requirement for potable water.
Moving into Phase 2
Thorough technical evaluation for the feasibility study underpinned the decision to enter the IHRS programme. Ongoing evaluation during the application process and Phase 1 implementation
quantified the large volume of warm air emitted by the compressor and, when combined with main plant exhaust heat recovery, made the opportunity compelling for decarbonising the process through Phase 2.
Business projections indicate that energy demand is likely to increase along with the unit cost. The data, which was fed into the evaluation models, underscored the imperative of the broader environmental, economic and social benefits of decarbonising the business.
The next opportunity to apply to the programme ends on 31 July.