REE-L value from rare-earth elements recycling
Enzo Satkuru-Granzella, Analyst at Mkango Resources Limited, and Abeshaa Mahendran, Metallurgist at HyProMag, review a novel, rare-earth elements recycling technique using hydrogen.
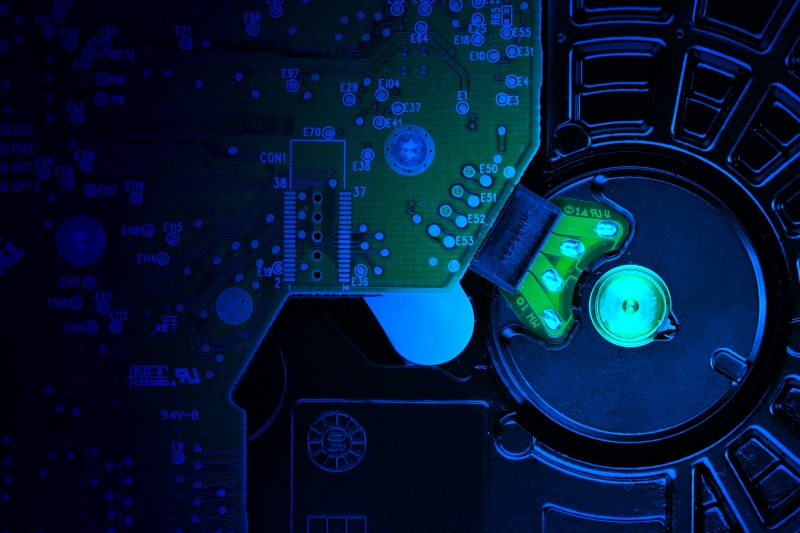
Rare-earth elements (REEs) are increasingly in the spotlight as critical minerals globally. Comparative analyses of 35 national and regional critical minerals lists finds neodymium to occur 23 times, only bested by cobalt and lithium. Dysprosium comes in at 22, with praseodymium at 17. REEs as a collective receive mentions on nine lists.
Most criticality assessments in the critical mineral context boil down to a mineral’s supply risk and the relative importance of its utilities, and whether there is an adequate substitute for its applications.
Rare-earth permanent magnets (REPMs) attribute most of the market value to neodymium, praseodymium, dysprosium and terbium, with an honourable mention to samarium in samarium-cobalt magnets – another class of REPM with specialised applications.
Neodymium-iron-boron magnets, or NdFeB, are the key market driver in REE demand and are crucial in over 200 products, with higher-temperature applications using dysprosium additives. The NdFeB magnets are used in consumer electronics – such as smartphones and hard disk drives (HDDs) – and are key to net-zero goals with uses in electric vehicle motors (EVs) and in permanent magnet generators in wind turbines.
Concentrated supply
While rare earths themselves are not particularly rare in objective terms, they are seldom found in concentrations that make their exploitation through mining operations economically viable or justifiable.
REEs are geographically – and geopolitically – concentrated. China remains dominant in the mining and refining stages of the REE supply chain, mining both hard-rock orebodies and ionic sand deposits. The latter being favourable for extracting ‘heavy’ rare earths such as dysprosium and terbium, while hard-rock deposits tend to geologically favour the ‘lights’ such as neodymium and praseodymium.
China currently refines ~99% of dysprosium and 88% of neodymium, with ~90% global REPM manufacturing capacity.
Apart from China, only the US, Australia and Myanmar are mining REEs in significant volumes. There are several REE mining projects under development, in multiple African jurisdictions, in Australia and in North America, most of which are at various feasibility stages.
The lag time in bringing mining operations online, alongside their intensive capital and operating expenditures, make REE projects a difficult sell despite high-demand projections, largely due to continued weak pricing for rare-earth oxides (REOs). This will change in the future.
Additionally, the necessary industrial capabilities and technical know-how to process and refine the mine product into separated REOs raises further issues, with market leader China introducing a ban on the export of REE processing and separation technologies in late-2023. A multi-pronged approach seems to be the logical way in achieving a secure supply of critical minerals.
The environmental issues associated with each stage of the REE supply chain also certainly do it no favours. There is clear acknowledgement that mining should be carried out in an environmentally and socially responsible manner, as there is little doubt that mining as an extractive method will continue to be necessary for the foreseeable future due to demand outpacing mined supply in coming years.
Circular economies therefore have an even larger role to play. The capacity and capability for large-scale recycling of various critical minerals needs to start now if there is any hope of meeting the targets set out in legislation across different jurisdictions.
The EU’s Critical Raw Materials Act stipulates a 25% recycling rate for critical minerals by 2030. This may sound modest, but in the REE context, less than ~1% were being recycled in the EU in 2021, and it has likely not increased by much. The rapid commercialisation, investment and policy support for recycling technologies are crucial if there is to be growth in the critical minerals recycling sector, and in achieving a responsible and secure supply, with demand rocketing in the coming years.
Did you know?
Forecasts indicate that the demand for rare-earth elements will increase by three-to-seven times by 2040, driven by the green transition and the associated clean technologies.Source: The Role of Critical Minerals in Clean Energy Transitions, International Energy Agency
Keeping it clean
Recovering REEs from mine tailings is one avenue being explored as an alternative source, but the most abundant, accessible and exploitable waste stream in the context of REEs, is end-of-life REPMs. Currently, these magnets are generally not recovered from end-of-life HDDs and consumer electronics. The drives are being shredded along with their housing, so the contained REE content is lost to waste streams.
Conventional recycling routes for NdFeB magnets exist, using a chemical long-loop process. This generally uses hydrometallurgical methods such as leaching and solvent extraction.
It is a multi-step process, beginning with the roasting of scrap alloys to produce an oxide, which is then transferred through a series of leaching steps with strong acids to dissolve it. This is followed by iron removal with an organic solvent in a mixer settler unit operation.
The solution is purified, and the REOs are recovered using selective precipitation and calcination, producing separated rare earth carbonates.
Drawbacks include large aqueous and organic waste streams, with a considerable environmental footprint from the use of hazardous chemicals. There have been numerous developments to optimise processes, particularly by maximising the recycling and regeneration of the reagents and improving wastewater treatment processes. However, some of the key challenges in recycling REPMs lie in the dismantling and pre-processing steps.
HyProMag, a spin-out company from the University of Birmingham, UK, is commercialising the patented hydrogen process of magnetic scrap (HPMS) technology. This involves a combination of mechanical agitation and hydrogen decrepitation to liberate NdFeB material from end-of-life components.
Components used in many ‘clean energy’ technologies can be processed, liberating tonnes of magnet material that would have otherwise been lost as waste. Unlocking this stream of recycled NdFeB material presents an alternate source of feedstock from primary mined REEs to produce new NdFeB magnets.
In the context of HDDs, the automated dismantling unit is mobile and container-based, and uses optical and magnetic means to identify the REPM location in the housing. It then uses an alligator shear to cut off the corner of the HDD containing the REPM and discards the rest for shredding. This allows a substantial reduction in magnet extraction time, taking two seconds per HDD on average, in comparison to previous semi-automated times of two minutes per drive, and manual dismantling of up to five minutes per drive. This ensures that the technologies necessary for managing the increasingly large scrap quantities will be well developed and in place to deal with the increased demand for the recycling of REEs.
The HPMS process lends itself to the recycling of components containing REES as it avoids the need for thermal demagnetisation, or significant manual dismantling, all while using room temperature and atmospheric pressure to decrepitate the magnets.
Hydrogen decrepitation expands the magnet material volume, causing any coatings to peel away from the surface of the magnet, leaving a friable, demagnetised powder. Contaminants, such as coating materials, screws and fasteners, can be easily separated by mechanical means from the demagnetised powder. Sieving the powder to an appropriate purity level enables it to be jet-milled and reprocessed into a sintered magnet. The post-purification process (sieving) used by HyProMag is identical to that of conventional NdFeB magnet manufacture.
HPMS is more energy efficient than conventional recycling processes that use hydrometallurgy and pyrometallurgy, and significantly more efficient when compared to conventional mine-to-magnet supply chains.
Studies have put the HPMS magnet-to-magnet recycling route at 78% less energy intensive than traditional mine-to-magnet, also offering 80-90% savings in comparative toxic unit equivalent to humans and freshwater ecosystems. Water use is reduced by 85%, and overall CO2e stand at 85% less. HyProMag aims to source the hydrogen for its commercial-scale plant from a local provider based at the same site at the Tyseley Energy Park, UK, producing green hydrogen with no carbon footprint.
The HPMS process can readily accept magnets from end-of-life components including HDDs, loudspeakers, automotive drive motors, magnetic filtration systems and production scrap from NdFeB manufacturing. Trials and projects pertaining to the efficient processing of other scrap sources – such as wind turbine, direct-drive, permanent magnet generators – continues.
HyProMag has manufactured well over 3,000 magnets to date on pilot-scale equipment at the University of Birmingham – announcing in early 2024 the production of sintered rare-earth magnets on commercial-scale equipment in the UK.
Development of magnet coating capabilities in the UK is key to creating a market for sintered magnets. The recycled magnets have been successfully coated in both epoxy and zinc, with trials continuing on nickel-coated magnets. Combining these proficiencies with machining capabilities underpin the skills and know-how that are critical to mass production of sintered NdFeB magnets – skills that were outsourced from the country almost 20 years ago.
Through continued R&D with the University of Birmingham, and the optimisation of several processing steps such as jet milling and sintering, HyProMag can manufacture magnets using recycled feedstock exceeding the N45 neodymium disc magnet in remanence and SH in coercivity. There is constant development taking place to further improve properties of the output magnets, regardless of the grade or of the incoming scrap source.
According to their chemical composition, which is verified through inductively coupled plasma emission spectrum, magnets have their sintering profile tailored allowing for significant improvement in their properties. This enables HyProMag to bring recycled magnets in-line with the properties exhibited in the primary market of NdFeB magnets. These developments are collectively underpinned by ~US$100mln of R&D at the University of Birmingham, and with associated project partners to date.
HyProMag has the potential to increase rare-earths recovery and change the recycling and manufacturing of increasingly vital NdFeB magnets. It is one of only 23 global projects selected for support by the Minerals Security Partnership, made up of 14 partners including the US, UK, the EU and Japan.
With massive volumes of NdFeB scrap forecast to enter the global market in the coming years from clean-energy technologies such as EVs and offshore wind turbines, HyProMag stands ready to offer a solution that will recover material and add value to critical REEs in an environmentally responsible and sustainable manner.
Did you know?
HyProMag was founded in 2018 by the late Professor Emeritus Rex Harris FIMMM, former Head of the Magnetic Materials Group (MMG) within the School of Metallurgy and Materials at the University of Birmingham, UK; Professor Allan Walton, current Head of the MMG; and two Honorary Fellows Dr John Speight and Mr David Kennedy, leading world experts in rare-earth magnetic materials, alloys and hydrogen technology, with significant industry experience.As with most ventures in the world of industrial innovation, the development of the enabling technologies, know-how and friendships that facilitated the inception
of HyProMag stretch back much further.
The MMG has been active in the field of rare-earth alloys and the processing of permanent magnets using hydrogen for over 40 years. The hydrogen decrepitation method itself was originated by the late Harris, used to reduce neodymium-iron-boron alloys to a powder, and is ubiquitously employed in worldwide magnet processing. The hydrogen process of magnetic scrap (HPMS) was originally developed within the MMG, and subsequently licensed to HyProMag for commissioning and scale-up to provide an end-to-end, magnet-to-magnet supply chain.
The commercialisation of its sister company, HyProMag GmbH in Germany, is scheduled for later this year, with further expansion into the US market targeting 2025 production on an even larger scale.