Reducing the energy intensity of carbon fibre production
The heating method is based on a dielectric susceptors nanocoating made of layers of carbon nanotubes.
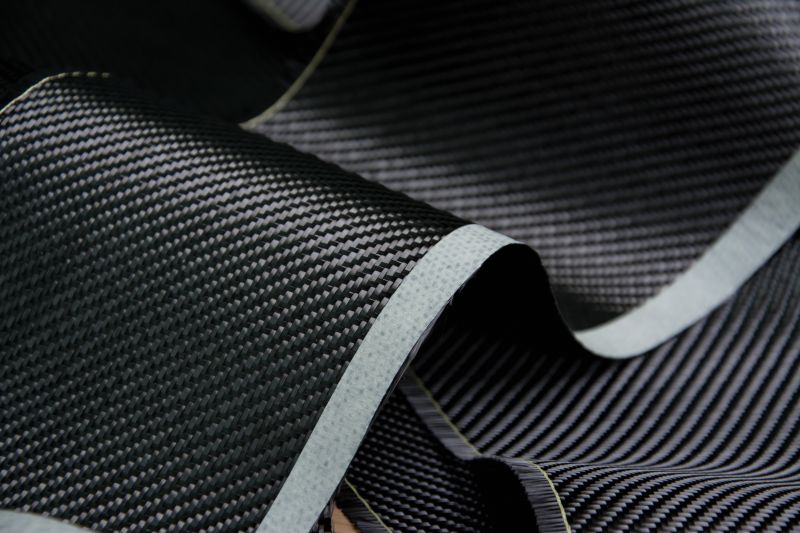
Producing carbon fibre using plasma and microwave heating could 'drastically' reduce its energy footprint by up to 70%.
A team at the University of Limerick (UL), Ireland, leads on the CARBOWAVE project, a collaboration of research institutions and industry partners across Europe.
The group believes the advances will enable more efficient conversion of polyacrylonitrile (PAN), a key component in carbon-fibre production.
A dielectric susceptors nanocoating made of layers of carbon nanotubes absorbs microwave energy and converts it into heat with high efficiency.
The UL team says, 'By applying these nanocoatings on microwave transparent materials, such as PAN carbon-fibre precursors, we can heat up the fibres (that typically cannot be heated with microwaves) to more than 1,000oC in an inert atmosphere, allowing for the conversion into carbon fibres.'
The concept originates from an earlier project carried out at UL and the University of Valencia, Spain, where scientists hypothesised the benefits of susceptor microwave heating.
One of the postdoctoral researchers developed carbon-based, nanostructured, susceptor coatings on precursor fibres. These findings were ultimately translated into a patent.
The paper – Decreasing the environmental impact of carbon fibre production via microwave carbonisation enabled by self-assembled nanostructured coatings in Advanced Composites and Hybrid Materials – details the group’s method.
The spun PAN fibres are a blend of Alcell organosolv hardwood lignin and thermoplastic polyurethane, developed by melt-spinning into a precursor fibre in a ratio of 50:50.
Before coating, the precursor fibre is corona-treated to improve wettability and then coated with the microwave susceptor coating, containing multi-walled carbon nanotubes (MWCNTs).
These are ground into a cationic solution, which the fibres are immersed into for five minutes, followed by rinsing and drying and then dipping into an anionic suspension for another five minutes.
The group reports how the electrostatic interaction between the aqueous solution and the charged polymer deposits the MWCNTs. Subsequent cycles are completed with two-minute dip times, and the team applies one-to-five cycles of the susceptor nanocoating to the fibres.
The study concludes that susceptor-assisted microwave carbonisation results in rapid heating of 20-40 minutes with the highest recorded temperature of 1,346°C, and calculated graphitic crystallite size values are comparable with the conventional carbonisation process.
Reduction of heating rates during intermediate stages of microwave carbonisation, to 600-800°C, is required. Increasing the nanocoatings up to five cycles was found to improve the absorption of microwaves.
'Microwave heating is a faster and more efficient heating method than the conventional heating, which use large convection furnaces with high amount of nitrogen,' the UL team states.
'The microwave energy applied to the fibres can be tuned and is converted instantly into heat, reducing the inertia in the process and the amount of energy used.
'The high efficiency of the microwave heating allows for the reduction in size of the carbonisation chamber, allowing for a reduction in the amount of energy necessary to heat up the nitrogen gas.'
The paper reports that the average tensile strength, Young modulus and strain of the carbon-fibre samples, coated after stabilisation, are in the range of 0.41-0.83GPa, 76.5-131.75GPa and 0.64-0.84%, respectively.
CARBOWAVE will scale up this technology to continuously produce fibres under microwave carbonisation.
Their study includes a lifecycle and environmental impact analysis, which shows that microwave heating reduces the energy demand and environmental impact of lignin-based carbon-fibre production by up to 66.8% and 69.5%, respectively.
The team reports the coating technology is transferable to other microwave transparent materials to produce complex geometries.