Recyclable polymers for 3D printing
A new class of recyclable polymers called polythioenones (PCTEs) are reported suitable for 3D printing.
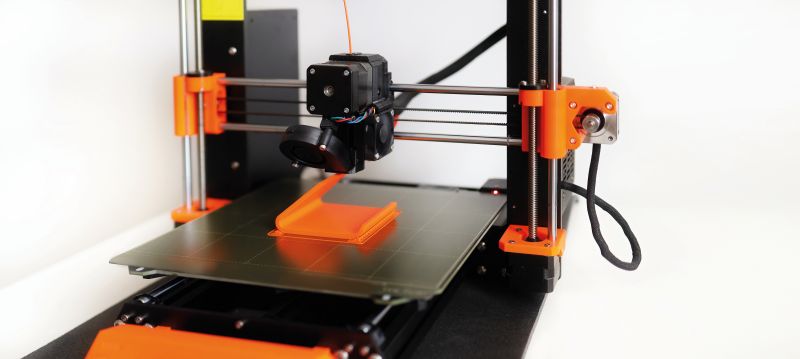
These polymers also reportedly demonstrate better mechanical properties than conventional polyolefins.
Polymers currently used in 3D printing have limited recyclability, or display degradation of material properties upon mechanical recycling.
A team from the Georgia Institute of Technology, USA, has now developed a novel family of monomers, cyclic thioenones (CTE) – rings made of seven carbon atoms and one sulphur atom. The rings contain one C=C double bond and one carbonyl group (C=O), and can readily be modified by the addition of different side groups.
The monomers can be polymerised through a ring-opening reaction in which monomers are added one at a time to the end of the growing chain. Known as a thia-Michael addition, this reaction is reversible, meaning that the resulting PCTEs can be depolymerised back to the starting monomer.
One of the synthesised polymers, PCTE-Ph, is a thermoplastic made from a CTE monomer with an aromatic six-membered carbon ring (phenyl ring) as its side group.
Will Gutekunst, Associate Professor at the Georgia Institute of Technology, says, 'The key CTE monomer is synthesised in a two-step reaction sequence starting from phenylacetylene and chlorovaleryl chloride…the final step closes the eight-membered ring with potassium thioacetate.
'The polymerisation is performed by treating the monomer with a thiol-containing initiator and appropriate base. From there, the polymerisation is halted by the addition of an equivalent of acid, and the final material is isolated through precipitation.'
He continues, 'PCTE-Ph has a glass transition temperature (Tg) of 24°C, Young’s modulus of 640MPa, a yield stress of 40.4MPa and an elongation at break of 373%. It can be readily processed into filaments or transparent yellow films, and the films show promise for UV-blocking applications.
'It makes for a nice filament material due to the large window between its flow temperature (Tf ~100°C) and its decomposition temperature (Td-5% = 295°C), and this characteristic also permits mechanical processing without reduction in material performance.'
The advantage of these properties over existing filaments for fused-filament fabrication is the ability to catalytically depolmyerise the printed polymer back to its original monomer in 90% yield, while preserving the mechanical properties.
It can also be mechanically recycled by melting the material without degradation, says the team.
Gutekunst adds, 'Higher-molecular-weight samples of PCTE-Ph show a yield stress of 40.4MPa and samples could be elongated to nearly four times its original length before breaking, meaning the material is quite tough and ductile.'
This work builds on a collaboration between laboratories at the Georgia Institute of Technology.
The Ramprasad Lab has developed machine-learning algorithms to accelerate the prediction of the ring-strain energies of monomers for use in ring-opening polymerisation. The ring-strain energy determines the thermodynamic favourability of a polymerisation reaction.
When this energy is moderate, the equilibrium between the monomer and polymer can be shifted based on temperature. This means that a polymer can be synthesised at low temperature, and then chemically recycled back to the original monomer at high temperatures.
The Ramprasad group predicated a subset of CTEs with eight-membered rings would have suitable ring-strain energies for this recycling process, and Gutekunst’s group set out to synthesise the CTE monomers and validate these predictions.
They are looking to further modify the CTE monomer scaffold to design polymers for new application areas and further optimise properties.
Gutekunst says, 'While additive manufacturing is a great testing ground to demonstrate performance, we believe this polymer platform has exciting potential as a recyclable material beyond the 3D-printing space.'