Preventing power pole-top fires with a silicone composite
Engineers at RMIT University in Australia have made power-pole insulators resistant to fire and electrical sparking with a silicone composite.
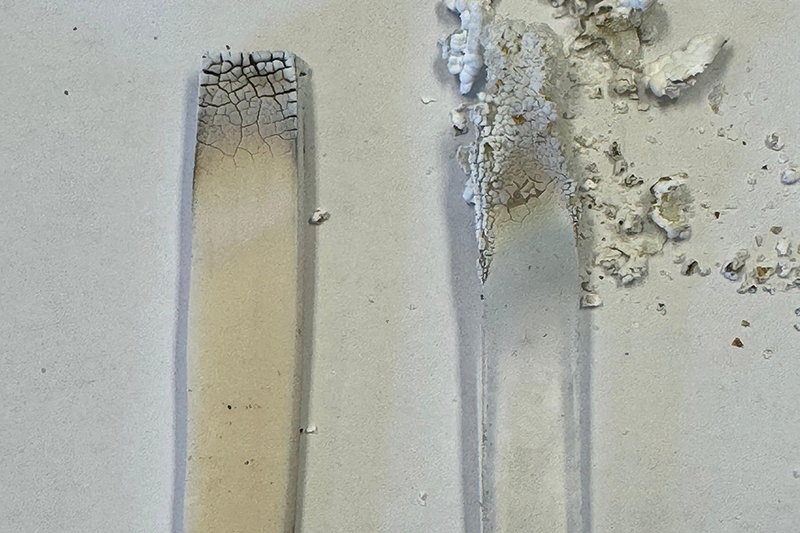
Engineers in Australia have discovered a way to make power-pole insulators resistant to fire and electrical sparking with a silicone composite.
Pole-top fires pose significant challenges to power providers and communities worldwide. In March this year, pole-top fires cut power from 40,000 homes and businesses in Perth.
RMIT University’s Dr Tariq Nazir explains how these fires can occur when consecutive hot, dry and windy days are followed by damp and misty conditions. 'Dust and pollution builds up on power-line insulators, which enables electricity to spark and heat metal fixtures that can cause wooden power poles to catch fire,' he shares.
In collaboration with the University of New South Wales, Nazir reports improving the performance and safety of these insulation materials with a silicone rubber composite material of chopped fibreglass, aluminium hydroxide and a type of clay derived from volcanic ash as additives.
Nazir breaks this down, 'Silicone rubber material with its excellent hydrophobic properties was used as main binder for the coating, while aluminium hydroxide is used as flame retardant filler, and anti-electrical discharge provider, nanoclay montmorillonite [is] engaged as flame retardant and barrier against gas and heat flow. Moreover, hopped glass fibre is used as reinforcer filler to enhance structural integrity and contribute to improved flame retardancy.'
He says, 'In terms of fire resistance, the proposed new material demonstrated a 54% improvement compared to the non-additive pure form of silicone material and exhibited 35% higher flame resistance than commercially available silicone materials filled with additives.'
Nazir says the new composite also displays 'a 59.3% reduction in maximum average heat-release rate and a 92% reduction in total smoke production compared to commercially available material'. Meaning the material is less likely to contribute to fire spread and produces less smoke, enhancing overall safety, he claims.
Also, the material 'exhibits better surface discharge resistance with a 18% higher partial discharge inception voltage rating, indicating that it can handle higher electrical stress and has improved electrical insulation properties, reducing the risk of electrical failures'.
Nazir states, 'With coating, maintenance costs can be reduced by 50% and fire incidents by 80%, lowering the total annual cost to A$70,000 and reducing maintenance time by 500 hours. This results in annual savings of A$130,000 and 500 hours'.
Nazir said their research’s novelty was in exploring the flame retardancy of insulator materials. 'Others are working mainly in electrical discharge resistance.'
He shares how 'a commercially available pure form of liquid silicone was received in parts (A&B) with a base viscosity of 5,100centiPoise. Part A is a main polymer while part B is mixed as harder to cure the polymer…Afterwards, the composites were placed in a lab vacuum pump chamber and degassed until no trapped air is seen on the top surface in the form of bubbles'.
He continues, 'The moulds were preheated in the oven to abstain the settling of additives on the surface of the moulds. Finally, the moulds were placed in the lab oven and the curing was performed at 120°C for 1,800s.' Composites with five different formulations were prepared.
Nazir is working closely with industry partner Flame Security International and the Defence Science Institute in Australia.
He adds, 'We are keen to engage with fire-retardant coating manufacturers, electrical utilities, electrical insulation designers, manufacturers of electrical insulation products and regulatory agencies to further develop and prototype this work.'
Next steps include transitioning to larger-scale production and durability testing under simulated outdoor conditions. Additionally, application-specific testing will assess various scenarios and integration with existing systems.
Nazir will also pursue regulatory compliance and certification, amid ongoing exploration of new additives and technologies. These steps aim to refine, validate and deploy the material for widespread use in outdoor electrical insulation applications.