Polymer upcycles to structural adhesive
A common household plastic has been transformed into a reusable adhesive by US scientists, who claim it combines strength and ductility producing one of the toughest materials reported.
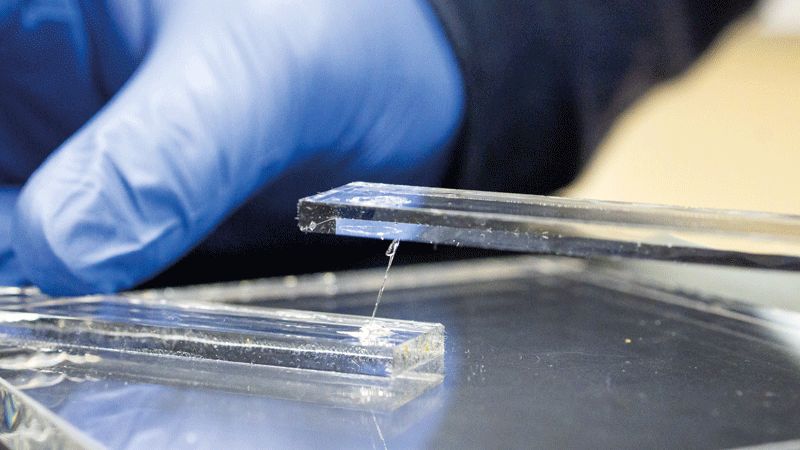
Researchers at the Oak Ridge National Laboratory say the new adhesive can bear heavy loads, endure extreme stress and heat, and reversibly bond to different surfaces, including glass, aluminium and steel.
They note that structural adhesives, such as epoxy, are made for load-bearing applications but lack the toughness to dissipate stress and prevent sudden failure.
‘The challenge has been to add the toughness you get in flexible materials without sacrificing strength. Our approach uses dynamic chemical bonds to develop a novel adhesive with remarkable properties not seen in current materials,’ says research lead Tomonori Saito. The study upcycles a rubbery thermoplastic – polystyrene-b-poly(ethylene-co-butylene)-b-polystyrene (SEBS) – that is easily processed but not suitable for tough adhesion. The team has modified the SEBS structure with dynamic crosslinking so it is more robust and can be reused in alternative applications.
Boronic esters are mixed with the functionalised commodity polymer to crosslink it with silica nanoparticles (SiNP) in a minimum amount of solvent for one to two hours at room temperature.
Normally, crosslinking creates permanent bonds that would prevent the adhesives being reprocessed, but the boronic esters enable ‘dynamic’, or reversible crosslinking, which is key to the new material’s adhesion and ability to be recycled.
‘A fundamental discovery was that the boronic esters on SEBS can rearrange bonds with hydroxyl groups – oxygen and hydrogen – on SiNP to adapt properties for demanding jobs. We also found the formation of similar reversible boronic ester bonds with a variety of surfaces that have the hydroxyl groups,’ says first author of the study, Md Anisur Rahman.
Once applied to a surface, the adhesive then needs to cure at 215°C for one to two hours under minimum pressure. It can be used as both a solid and liquid glue, but it uses a minimum amount of solvent for a liquid glue.
‘The process is similar to commercially available adhesives, but lowering curing temperature, minimising the process time, and reducing the cost are desirable for commercial deployment,’ adds Saito.
A thin square centimetre of the new material can hold approximately 135kg, reports the team, while shear tests used to determine toughness are said to surpass many existing commercial adhesives. For example, a 20wt.% SiNP S-Bpin composite dry adhesive performs as follows at 23°C – 25 ± 0.92MPa with aluminium, 28.54 ± 1.45MPa with steel, and 39.6 ± 3.2MPa with glass.
The adhesive is reported to be so tough that the glass fractures before debonding. It also displays thermal stability up to about 200°C while still capable of being applied and detached multiple times.
‘By design, this adhesive allows you to make repairs or correct costly mistakes and can be reprocessed for new uses in very challenging applications,’ Saito says, such as aerospace, automotive, or construction.
Even after its adhesive properties are exhausted, it can be repurposed. ‘Due to the presence of dynamic boronic ester bonds, our materials (even after using for adhesives) can be reused/reprocessed into tough thermoplastic materials for different commodity applications, beyond adhesives, including car parts, sports gear, toys, etc.’
In a bid to commercialise the adhesive, the researchers are exploring dynamic crosslinking with other fillers to manufacture tough adhesives for specific surfaces and functions.
‘We are currently working on reducing the curing temperature and to scale up the adhesive materials.’ The other challenge is reducing the cost of the building blocks.
Saito believes that the research has replicable processes that could be exploited in other studies. ‘This result is due to the formation of dynamic chemical bonds between our upcycled polymer and SiNPs as well as various oxide surfaces (aluminium, glass, steel). Our finding of dynamic bond formation with many hydroxyl surfaces can be adopted in many hybrid materials as well as joining types of applications. Material scientists can utilise this strategy in various material systems,’ he says.