Perfect pitch – closing the loop on carbon fibre production
A US university collaboration has developed carbon fibres from petroleum pitch – a by-product of oil refining.
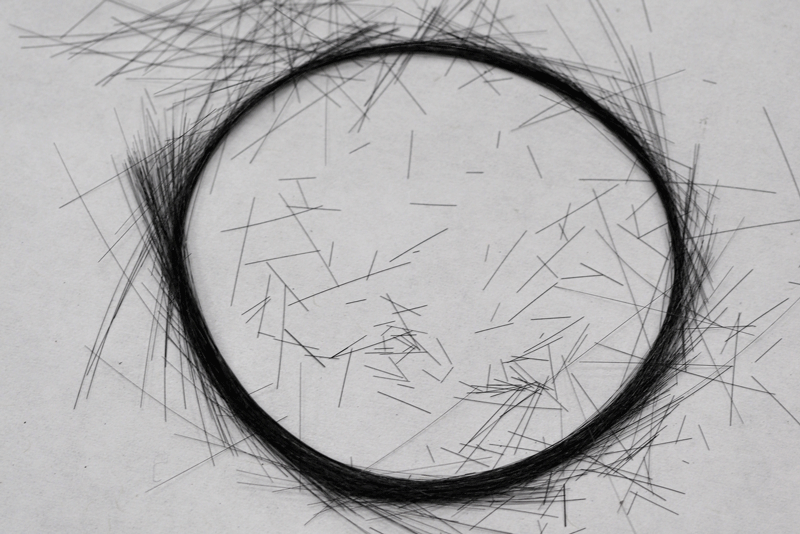
The four-year research project at the Massachusetts Institute of Technology (MIT) and Oak Ridge National Laboratory also tested coal pitch from coking coal in steel production.
Lightweight materials made from carbon fibre have traditionally been more expensive to produce than comparable structural elements made of steel or aluminium. The US Department of Energy (DOE) funded this study in its search for more affordable structural materials for automotives that are comparable to steel but cost less than U$11/kg. MIT research scientist, Nicola Ferralis, notes that a pick-up truck made of existing carbon fibre instead of steel roughly doubles the cost. The researchers estimate their carbon fibres will be less than U$6.50/kg.
Carbon fibres usually come from petroleum-derived polymers, such as polyacrylonitrile, but the carbon compounds must be polymerised, which can be more than 60% of the cost.
MIT researcher, Asmita Jana, explains pitch is made up of polycyclic aromatic hydrocarbon molecules that are randomly oriented (isotropic pitch). These are thermally aligned (mesophase pitch) along the fibre direction before being melt-spun, where they are extruded in a molten stage to give precursor fibres.
These are heated to 250-300°C with oxygen so crosslinks form via oxygen functional groups between neighbouring molecules. The fibres are then heated to ~500°C in an inert atmosphere to remove the oxygen, before being heated to ~3,000°C to give graphitic flakes so they have a very high modulus.
The researchers have modelled the bonds and crosslinking between constituent molecules to predict how different processing conditions affect the resulting properties. ‘Firstly, the pitch precursor molecules are heterogeneous, so, we figured that the shape, size, functional groups, and dispersity of the initial molecules could affect the final properties. Secondly, the manufacturing procedure used results in processing parameters like density, temperatures, oxygen diffusion rate, etc. that can also affect the final properties,’ explain Jana and Ferralis.
By adjusting the conditions, they have modelled fibres that are strong in compression as well as tension.
Carbon fibres based on the models have been fabricated at both laboratory-scale and pilot-scale. The scientists have found that the performance metrics of density and elastic modulus are computationally aligned with the experimental fibres. They say, ‘We believe that the phase space performance evaluation these models have achieved can be used in research and commercial labs to reliably predict elastic modulus.’ Ferralis notes the fabrication can be adapted depending on the required performance metrics.
A separate analysis has found that the pitch-based carbon fibre can be produced reliably and at scale. By focusing on isotropic pitch and pressure and density control, crosslinking can now occur in all directions.
A more affordable cost, say Jana and Ferralis, means carbon fibre could be used anywhere in a car.
‘More extensive use, under this cost bracket, could be foreseen in more significant components than the one we see right now in supercars, such as in parts of the chassis, roof, and heavy system supports (powertrain, suspensions, etc.), where titanium and aluminium are currently used,’ Ferralis says. ‘Even in [its] limited deployment, carbon fibre can provide significant weight redistribution benefits, for example, lightweight components high on the car (roofs) lower the centre of gravity, providing better and safer handling.’
The team thinks another potential application could be structural elements in buildings, such as rebars.
When asked if their pitch-derived fibres would help prolong fossil fuel use, Ferralis says, ‘It should be considered, as we do for many other mined elements from lithium to cobalt, as a resource that could be used directly (not because of other processes).’