Peatland plants pack a punch
Peatland plants could make folding boxes, trays and similar items, says the team at the Fraunhofer Institute for Process Engineering and Packaging IVV in Germany.
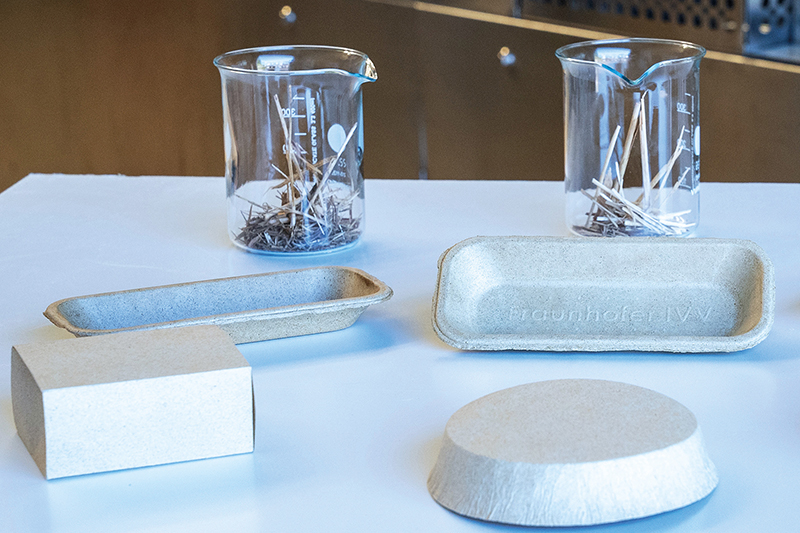
The team in Freising and Dresden were looking for alternative raw material sources for paper after market prices sharply increased due to a high-import ratio of 80%.
They have tested peatland plants such as reed, sedge or reed canary grass cultivated in rewetted peat bogs and fens.
The EU Nature Restoration Law of February 2024 plans to rewet and renature at least 30% of forests, grasslands and wetlands in Europe. Paludiculture is the discipline of farming in wet peatlands with locally adapted plant species.
Compared to wood, reeds and similar plants have a low lignin content, reports the team, after chemically characterising paludicultures from the Freisinger Moos fen region. Fewer chemicals are therefore needed to pulp the plant fibres to a sufficiently high quality for packaging applications.
And because lignin is more easily separated from non-wood fibres, pulping methods use less energy than conventional paper manufacturing processes, the team says. Depending on the plant, the group claims to achieve a lignin content of 20-23% – 25% or 15% lower than soft or hard-wood.
The team used a soda pulping process, which they say is more suitable for non-wood agricultural lignocellulose materials because of typically higher amounts of silica in comparison to soft and hard-wood.
This uses caustic soda as a chemical reagent to separate the cellulose from lignin and plant extractives and achieve high-quality fibre pulps.
They have focused on optimising the chemicals and energy demand at atmospheric pressure, rather than under pressure and with overheated steam, 'as the industrial state-of-the-art dictates'.
The researchers worked with temperatures under 100°C, up to 45% below the lowest values for chemical-fibre pulping methods, requiring less energy. They managed to separate 27-83% of lignin, with 14-53wt.% of pulp yield and 10-26% of residual lignin content, depending on the parameters. The team says up to 53% is within the expected range for conventional chemical processes.
The reed plant pulp is also said to have better mechanical properties than other straw pulps, such as corn or bamboo. Dr Marie Föllmer, Matthias Kott and Lorenzo Tomei at Fraunhofer say, 'The mechanical properties of reed grass are similar to those of other plant fibres. The tensile strength is higher in some cases, while the elongation capacity is somewhat lower.'
The experiments carried out sought to understand the impacts and potential synergies of caustic soda charge on the fibre mass, pH, temperature and time on pulped mass yield and residual target.
Subsequent experiments produced flat, fibre-moulded papers with good processability, reports the team. These samples had a tensile strength that was significantly higher than reference sample values, which had an egg carton shape. Additives like potato starch and common sizing agents further increased the tensile strength, elasticity and water-repellency. The papers could also be folded, glued and printed.
Using fibre-moulding and deep-drawing processes, the researchers say they can produce sturdy paper jars and trays from reed fibres without additives. They have developed a laboratory plant specifically for these packaging demonstrators.
Initially, there are plans to manufacture packaging for the non-food sector such as cosmetics, logistics and office materials. The team say larger quantities of paludic fibres are needed to optimise processes to make this economically viable, and there are issues of processability, printability and barrier properties to overcome.