Pandemic PPE testing
As PPE and ventilator production has ramped up during the COVID-19 crisis, the UK’s National Physical Laboratory (NPL) has scaled up its testing and inspection processes. Andy Morris, Operations Manager at the NPL North of England Laboratory, offers some insight into what’s been going on behind the scenes.
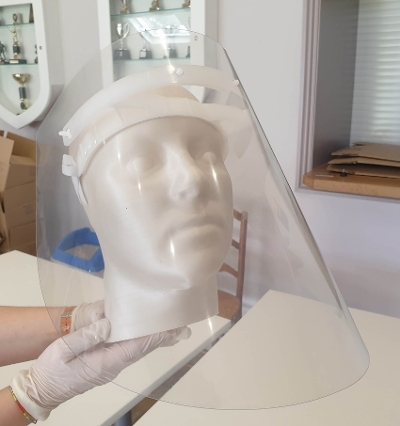
What have been the challenges and key considerations for testing and inspecting Personal Protective Equipment (PPE) and ventilators during the pandemic?
The initial challenges encountered at the NPL have been associated with the relevant standards. During the early days of the COVID-19 crisis, the guidelines coming out from Public Health England were changing quite quickly, this was to allow for those organisations that wished to produce PPE to be able to, but this also meant that NPL had to be agile in its response.
Some organisations were unaware of which standards would apply to PPE and how to interpret them, especially with the changes in requirements that were made to meet PPE needs for the crisis. In addition, all testing for PPE is usually undertaken by a Notified Body (NB), of which only a small number exist in the UK based on the usual requirement for testing or re-testing PPE products.
In response to this, there has been a need to try to replicate some of this testing to help screen out products that are most likely to fail when they are sent to a NB for testing. This additional step helps lessen the risk of a product failing and subsequently needing to be retested, which brings with it greater cost and increased demand on the NB. NBs use specialised rigs for their tests, so another challenge has been to try to replicate these tests quickly and at an affordable cost.
How has this work been impacted by the speedy turnarounds required?
When the Coronavirus hit the UK and cases started to rise, the demand for PPE sky-rocketed. To meet this demand, UK industry – from the smallest to the largest companies – stepped up to produce PPE which was often outside their usual scope of expertise. Due to the exponential rise in the demand and nature of the current climate, the quality and manufacturing process of PPE has never been more critical.
To minimise the risk of unknown quality or falsified CE marks entering the market, there has been an urgent requirement on manufacturers and customers to take action. There is widely available guidance to suppliers to ensure PPE is safe, especially during expediated production and delivery. Advice and support is available to end-users to ensure equipment meets safety criteria.
What have been the key technical developments in testing and inspection?
Where NPL has produced pre-compliance test systems, we have aimed to produce test systems that were capable of gathering as much data as possible about the PPE to try to understand why it passed, failed or was a borderline pass/fail. We believe that this information will be of use to manufacturers in the future and useful for those planning to produce more novel designs and adding novel features to their products (e.g anti-viral coatings).
Can you talk us through your work with industry partners during the current crisis?
NPL has had a wide involvement in a number of COVID-19 related projects. For PPE we have been a source of information for manufacturers and users to help them to ensure that any PPE entering the market was suitable and safe.
We started by helping organisations to design and manufacture face shields (visors) by advising on the correct interpretation of relevant standards and how designs could be improved to ensure that when tested against these standards, they would pass first time. This included inspecting CAD models of designs, checking materials against data sheets for performance and safety, modelling some of the tests and linking manufacturers to materials suppliers.
Protecting Heroes, a community interest company, worked with NPL to get their face shield through the testing and CE marking process. NPL also provided a packing and despatching service within our grounds in Teddington, UK, staffed by NPL volunteers. This work continues with an expectation that in excess of 100,000 face shields will be supplied to the NHS.
NPL has worked with a number of organisations to help them to produce a suitable face shield design and to get it through the testing process, this includes plastic injection moulded products as well as 3D-printed and laser cut products.
In parallel with this activity, NPL has worked with face mask manufacturers and end-users including hospital trusts. Our current work in this area is to build a range of test systems for pre-compliance testing of key performance characteristics for face masks, including breathability, filtration performance and splash resistance.
We are also working on additional tests that have been requested by manufacturers and end-users. We hope to be able to use these systems to gain a good understanding of face mask performance especially when this includes novel designs or materials.
Our most recent work has been on understanding how PPE can be cleaned and reused without any degradation in performance. Any reuse will be a significant saving in cost to users and also with the added benefit of reducing the amount of waste being produced by single-use products that currently dominate the market.
We are also working with companies who are keen to produce low-cost PPE, which will help to reduce the burden on those needing to use these products. It should also help to get PPE to those places where current products are unaffordable, including developing economies.
Can you elaborate on the insights gleaned through testing and how these influenced the various iterations of the designs and manufacture?
Some of the biggest lessons learnt were by engaging with the relevant NBs to understand why PPE fails testing. This gave us a great deal of insight into how a product should be designed to avoid these failures. For example, face shields sometimes fail due to lack of coverage or shielding above the brow, meaning that any coughs or sneezes could reach the wearers eyes if they were leaning down or nodding their head to speak to a patient.
We also know that there is a fine balance between breathability and filtration efficiency in face masks which can make them unusable or unsafe. For example, a highly efficient filter that blocks almost all external particles could be too difficult to breathe through. Or a mask with excellent breathability characteristics could have poor filtration and therefore expose the wearer to droplets containing pathogens.
By understanding why PPE fails, we have been able to help influence designs and also design test systems that can provide data to evaluate different designs and materials.
How do you ensure products meet clinical standards?
Ultimately, in most instances it is necessary that PPE products should be tested by a relevant NB and ideally CE marked for use. This means that these products must pass the tests outlined in relevant standards applicable to each of these products and their intended use.
In addition to this, end-users may have their own acceptance criteria which may go above and beyond the standard depending on the intended use. This is in the hands of these users.
NPL’s approach is to ensure that all PPE products that we are involved with helping to design and manufacture will not only meet necessary standards but will be capable of meeting these standards with ease. Any manufacturing process will include a degree of process variation, so by ensuring that products meet specification and pass testing easily, there is greater confidence in a very high percentage of these products always meeting specification and being safe.
Additional test data (where available) can help to determine if a product will pass easily or only just pass.
What have been the considerations around the supply chain and safe assembly?
In some instances, the end-user will be expected to ensure that the PPE they use is clean and/or sterilised. For some products, however, these need to be manufactured and packed in a clean environment to prevent any chance of contamination by COVID-19 or any other pathogen.
The manufacturing process needs to include a process for ensuring cleanliness and instructions to the user regarding the state of cleanliness.
In the projects where we have been involved in making, assembling and/or packing PPE products, we have worn appropriate PPE. In addition, when testing PPE, we ensure that the environment where the testing is taking place is clean and that PPE is worn by our own staff.
NPL runs a network, the NPL Manufacturer Measurement Network, which includes companies that have needed to sub-contract or supply chain skills including for PPE manufacture. We have called on this network for help and also helped network members to manufacture PPE.
What different skills within the Laboratory has this work drawn on?
We have experts in environmental monitoring, gas analysis, pressure instruments, instrument design, sensors, modelling and in various fields of testing.
We have designed all of our test systems with good metrology in mind, ensuring traceability of measurement, understanding of uncertainty, a greater range of measurement options, comparison techniques to help with correlation of data and a high degree of robustness.
How do you see activity during the pandemic influencing future development of PPE and ventilators?
I expect to see a big increase in domestic manufacturers of PPE to meet current and future demand. When Coronavirus landed, the whole world was in an auction to obtain PPE which resulted in lack of supplies. UK manufacturers have proved they can make PPE at the right quality and the right price. A lot of these manufacturers have helped in the short term, but others are already planning to continue with PPE manufacture into the future.
We are seeing lots of novel designs. Some of these are just for fashion purposes to encourage people to wear them. Others are more practical, to add additional safety, to make them more comfortable, significantly cheaper, recyclable, reusable etc.
If face mask wearing becomes more common, for example when seasonal flu hits us, then more and more clothes manufacturers will include publicly worn face coverings in their range, and then, perhaps new standards will emerge for testing these.
Have there been any lessons learnt that can be transferred to other areas of protective equipment in different sectors?
There has been quite a lot of collaboration, especially between SME manufacturers to produce PPE, this can only be a good thing and could lead to more collaboration of future manufacturing projects.
The way that manufacturers have successfully shifted their processes to PPE demonstrates how versatile they can be, and I would hope encourage them to be more flexible and agile in the future to meet shifting market demands.
NPL’s own knowledge of PPE has increased and we feel confident that this knowledge could be used in other areas of PPE design and testing, especially where this involves innovative designs and novel materials.
We have generated a lot of internal ideas about how future testing could be performed, how materials could be analysed for performance, how tests could be modelled and how we could help to determine the level of PPE reuse.