On the right wavelength - measuring moisture levels in clay bricks
Increased pressure has been placed on the UK clay brick sector to improve its resource and energy efficiency in a drive to reduce carbon emissions. Kevin Goodison, Product Specialist at LIMAB UK, explains how a near-infrared moisture gauge can accurately and reliably measure moisture levels in an effort to achieve this goal.

In October 2018, the Intergovernmental Panel on Climate Change (IPCC) reported that if the international community fails to limit global warming to 1.5°C above pre-industrial levels, it risks triggering multiple, climatic tipping points, which could result in unprecedented changes to our climate.
In an effort to avoid this potentially catastrophic scenario, countries were urged at the UN Climate Change COP26 Conference in November 2021 to strive towards achieving net-zero carbon emissions by 2050.
Every UK economic sector has a part to play in meeting this target. In its Net Zero Strategy, the UK Government states that it will decarbonise industry by supporting companies to switch to cleaner fuels, by helping them to improve their resource and energy efficiency, and through fair carbon pricing.
Manufacturing of clay bricks is a highly energy-intensive process. However, as stated in the Brick Development Association Sustainability Report 2021, 'The UK clay brick industry is determined to be a responsible stakeholder on this journey to net-zero”. With regard to energy, the aspiration is, 'to improve energy efficiency in the manufacturing process and reduce carbon emissions generated during manufacturing'. An important way in which UK clay brick manufacturers can do this is by accurately and reliably measuring clay moisture levels across the entire manufacturing process.
Measuring moisture
Water is integral to clay brick manufacturing. It is added at various stages during the process. However, all the added water needs to be driven off during the drying process before the bricks are fired. The more water that is added, the greater volume that needs to be evaporated off, which, in turn, extends the drying time.
However, if manufacturers can accurately and reliably measure the moisture levels in the clay throughout the manufacturing process, they should be able to precisely control the amount of water that is added and ensure that only the minimal amount required is applied. By doing this, the amount of water used is minimised, which reduces the drying time, improves energy efficiency and, ultimately, cuts carbon emissions.
Until recently, the moisture levels in clay have been measured by an extremely skilled workforce, drawing on a wealth of experience gained from years of working in this specialist sector. With their ‘calibrated fingers and eyes’, they would be able to determine whether the moisture level was correct simply by looking at and feeling the clay. However, as the industry becomes increasingly accountable for its water usage, energy efficiency and waste reduction, there is a need for more accurate, objective and reliable testing and inspection methods.
The manufacturing process has also become increasingly automated and the traditional method of moisture measurement (a loss on drying moisture balance or oven), which can be time-consuming, does not fit into this continuous method of production.
Near-infrared
Near infrared (NIR) moisture gauges are an effective and alternative measuring tool and work on the principle of NIR spectroscopy.
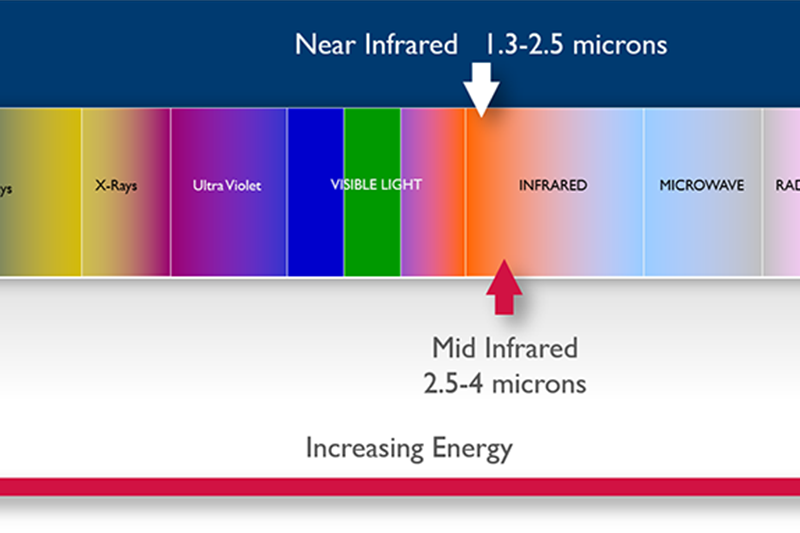
Spectroscopy is the study of the interaction between light and matter, and NIR spectroscopy refers to analysing how the bonds in various molecules react when exposed to NIR light. If NIR light strikes a molecule and the bonds within the molecule bend and vibrate, then the NIR light is absorbed.
The bonds in different molecules are known to bend and vibrate, i.e., absorb the NIR light, when irradiated with different wavelengths, so it is possible to identify the presence of a given molecule based on the wavelength of NIR light it absorbs.
Before you use a NIR moisture gauge to measure the levels of moisture, you first need to know what the base material is, in this case, clay mix for bricks, and the moisture range – 5-30% for example.
You then use this information to determine the precise wavelengths of NIR light that are required. Put simply, two wavelengths of NIR light are chosen – but, in reality, multiple wavelengths are used to increase the device’s range and capability. The first – the reference wavelength – is not absorbed by the base material, i.e., the clay mix. The second wavelength, which is absorbed by the constituent, i.e. water, is measured.
The moisture range is important – if the moisture is high, a less absorbing NIR wavelength needs to be chosen to give the gauge the required sensitivity. Conversely, if the moisture range is very low, a more sensitive NIR wavelength is more suitable.
White light is emitted via the source lamp, and this light contains the full spectrum of visible and NIR wavelengths. The light then passes through a multi-position, optical filter wheel, which rotates at around 7,500rpm. This wheel contains a number of special optical filters that only allow specific wavelengths of NIR light to pass through. These will be precise wavelengths that have been determined, based on the intended application for which the device is being used.
This method allows a number of very specific wavelengths of NIR light to be pulsed at a high frequency from the device. In the transmission graph right, 1.94µm is the wavelength used to determine the absorption by water, and another wavelength – that is unaffected by changing moisture levels – is used as a reference wavelength.
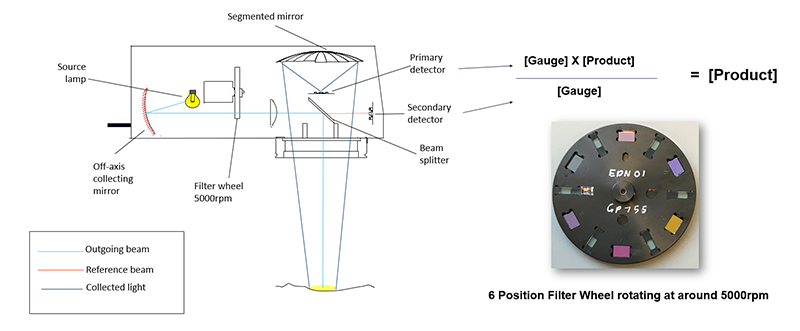
The light is then passed through the objective lens, which results in a slightly conical beam of light hitting the beam splitter. The beam splitter contains a matrix of precision holes and produces the reference beam, which is projected onto the secondary detector. Meanwhile, the outgoing beam passes through the viewing window down onto the clay, where some of the light is absorbed and some of the light is reflected.
This diffusely reflected light is captured on the segmented collecting mirror and focused onto the primary detector. The signals from the primary detector and the secondary detector are then processed through a specific algorithm to give a reading of the water level in the clay.
Not only does the use of a moisture gauge improve the accuracy and reliability of the moisture measurement, it also speeds up the process. The gauges are online and can be placed in multiple places throughout the production line, and the measurements can be used as part of an automated control loop to adjust the flow of water that is added during the manufacturing process.
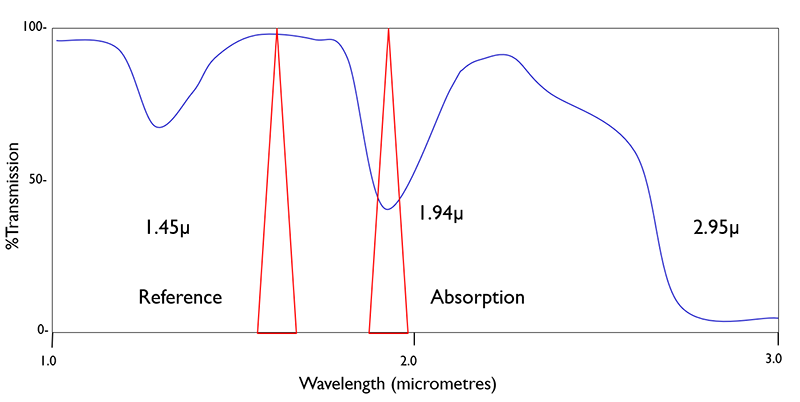
In situ
Many of the leading UK clay brick manufacturers are already using NIR moisture gauges to improve their production processes, enhance their energy efficiency and reduce their carbon emissions.
Andrew McGillivray, Engineering Manager at Forterra’s Kings Dyke Works, says, 'We have recently purchased three NIR moisture gauges to accurately measure the moisture content of the clay throughout the production cycle. The first NIR moisture gauge has been installed in the clay store, to monitor the initial moisture level of the clay arriving from the quarry. The second NIR moisture gauge has been installed above the main raw product infeed conveyor in the production shed, which feeds into the supply conveyor system.
'The third NIR moisture gauge has been fitted adjacent to our conveyor control office and is just after the grinding process, where the raw clay has been reduced in size ready for the presses – this is where the moisture content is at its most critical, just before the clay is formed into a brick.
'We used to rely on a moisture balance for the moisture reading, but this can take up to 30 minutes, which is just too long. By using the NIR moisture gauges, we are now able to monitor the live moisture levels from all three gauges simultaneously from one central point.
'We conducted a trial comparing the data from the NIR moisture gauges and two moisture balances. We had a good correlation, so we could see the NIR moisture gauges were accurate and stable. It gave us a good insight into the process.'
Scott Bamford, Technical Manager at Ibstock Brick Ltd based at Aldridge, adds, 'We found that we were actually losing a lot of money due to not having the correct moisture content in our bricks, so back in January 2019, we decided to look into implementing some NIR moisture gauges to enable us to monitor the process more effectively...having the ability to constantly monitor the moisture content has massively improved our quality control processes.'
Philip Smallridge, Process Improvement and Quality Control at Wienerberger, continues, 'I knew that some of the other Wienerberger sites had already purchased some NIR moisture gauges and I had heard that they were really improving the production processes and quality control procedures. After discussions, we went ahead and purchased four NIR moisture gauges. The NIR moisture gauges have really helped us to monitor and maintain greater control of our water input system. We are already getting some really useful data.'
By using a NIR moisture gauge to accurately and more effectively measure the moisture levels in the clay, it is possible to precisely control and consequently reduce the amount of water used during the manufacturing process. The rewards are shorter drying cycles, improved energy efficiency and reduced carbon emissions.
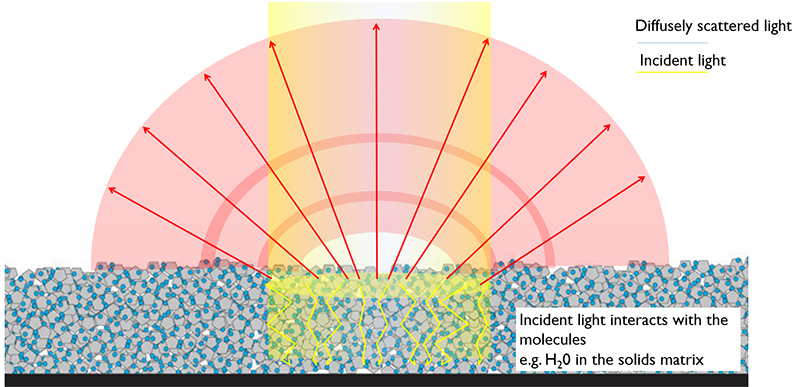