Novel flame-retardant epoxy resin is also recyclable
An epoxy resin from Empa, Switzerland, is reportedly repairable, recyclable and flame retardant.
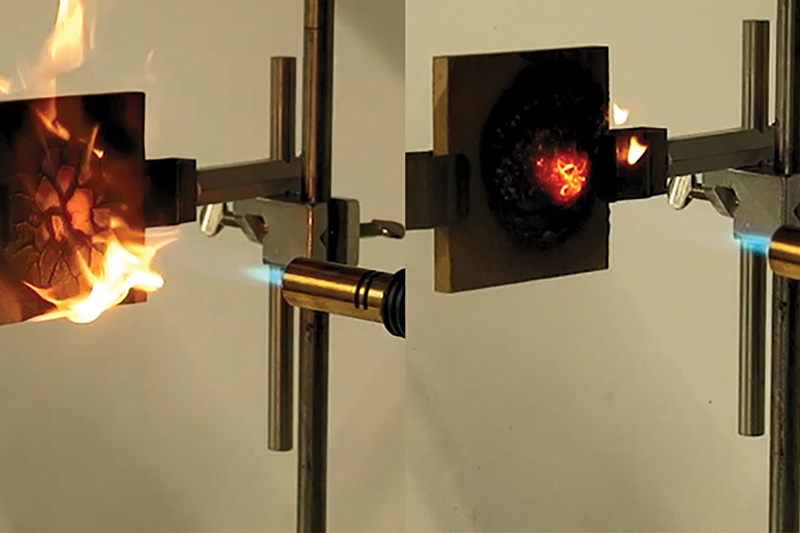
The resin has been created by researchers at Empa’s Advanced Fibres Laboratory in Switzerland, along with international partners.
The team, led by Dr Sabyasachi Gaan, claims the resin retains all the favourable thermomechanical properties associated with conventional epoxy resins.
They envisage applications such as coatings for wooden flooring or composites in aerospace and railways.
Epoxy resins are thermoset polymers where the molecular chains are closely crosslinked, and so melting and reshaping once hardened is difficult, traditionally inhibiting recycling.
However, this resin from Empa is reported to be melted and reshaped like a thermoplastic due to the addition of a functional molecule in the matrix from a class of phosphonate esters.
The resulting molecular bond is therefore dynamic and can be broken down on heating the resin to around 180°C, which softens the material enough for reforming.
'In presence of heat and a catalyst, you can break this bond and make new ones, and that is the key to recyclability of this material basically,' shares Gaan.
'You normally have an epoxy resin and a hardener, and what we did was substitute a part of a normal [amine] hardener with our tailored hardener, which is this phosphorus-containing monomer.'
The specific molecule is a bisphosphate – two phosphorus units bridged by the alcohol pentaerythritol, which ends up with a phosphorus molecule with two pH bonds at the end. And these pH bonds are very reactive, they react to the epoxy to form the phosphorus-carbon (PC) bond, explains Gaan.
The phosphorus-containing monomer binds to the resin via the PC bond, which is non-cleavable, and a phosphorus oxygen and carbon bond (POC), which is cleavable.
'We link the phosphorus moiety to the epoxy network via a POC bond, and the remaining part of the phosphorus moiety is linked by a dynamic covalent bond, which is this PO bond. The resulting phosphorus-containing moiety has “covalent adaptable bonds, which are actually reversible bonds'.
'You deliberately insert some weak points, and these weak bonds only respond to certain stimuli. You can reversibly break these bonds using a change of pH, or it could be temperature, pressure or light. When they break, you let the polymer network flow and that way you can recycle the material,' adds Gaan.
Explaining the importance of the recyclability, he says, 'A thermoset material is either completely combusted, incinerated or landfilled, depending on where you are in the world. People have tried to recycle thermoset material by heating them up, breaking them into smaller fragments and using these for fuel, but that’s not real recycling, you always lose a part of it.'
The flame-retardant ability comes from the phosphorus reacting with the polymer to form an “intense amount of char, and also produce radicals in the gas phase and quench the fuel radicals and prevent further burning of the material”, outlines Gaan.
Resin co-inventor Wenyu Wu Klingler notes that fibre-reinforced composites are difficult to recycle, except under very harsh conditions, which damages the fibres. Klingler and Gaan therefore see opportunities for the resin in carbon-fibre-reinforced plastics components.
Gaan suggests other properties, apart from flame retardancy, recyclability and repairability, can be optimised for the intended use, such as making exterior wood coatings weather resistant or improving flow properties.
Reportedly, the resin is inexpensive and straight-forward to manufacture, as it is made from materials that are readily available. While the phosphorus moiety requires synthesising, it can be prepared with a simple process from commercially available materials. 'Our eventual goal is to show full chemical recycling. To cleave these weak bonds, separate the resin from the matrix or the fibres and separate both,' Gaan concludes.