Non-wood biomass for textiles
Researchers at North Carolina State University, USA, have tried making man-made cellulosic fibres from non-wood sources such as agricultural residues and dedicated fibre crops.
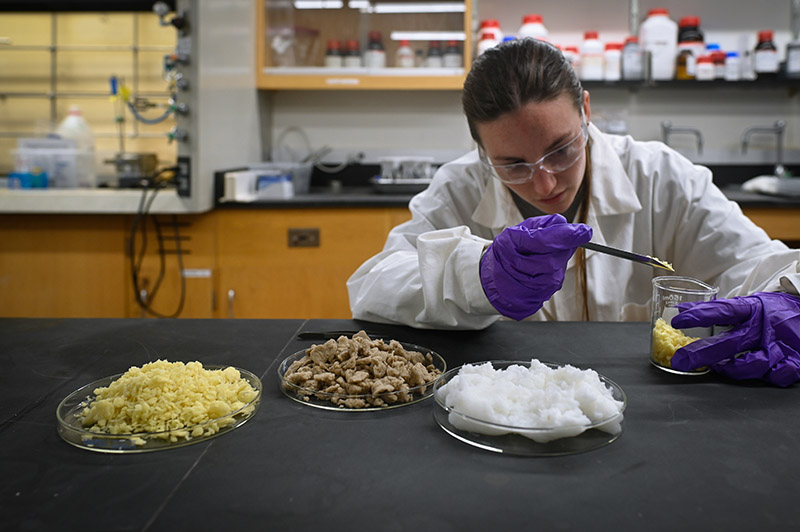
Researcher Ryen Frazier evaluating different grades of pulp
© North Carolina State UniversitySynthetic fibres like polyester account for more than 50% of the fashion industry’s market share and there is increasing pressure on cotton manufacturers to produce more natural fibre for growing demand. The paper in the Journal of Bioresources and Bioproducts focuses on suitable conversion technologies using non-wood-based dissolving pulp as a sustainable alternative.
Associate Professor Ronalds Gonzalez, from the University’s Department of Forest Biomaterials, explains how non-wood cellulose fibres offer multiple benefits for man-made cellulosic fibres (MMCFs) production.
As a natural polymer, cellulose biodegrades more easily than most synthetic polymers, he says. Also, non-wood residues tend to be burned or left on fields to decompose – if used to make dissolving pulp, these plant by-products could benefit other production streams such as textiles.
Researcher Ryen Frazier explains that non-wood-based dissolving pulp can be used to produce MMCFs through both conventional and established manufacturing methods such as viscose, acetate and lyocell.
Each method results in slightly different properties and specifies a criteria for the alpha-cellulose, hemicellulose, lignin and ash content of the dissolving pulp as well as other impurities.
Initial laboratory studies referenced in the academic paper reveal lithium chloride/N,N-dimethylacetamide has been used to convert straw biomass into textile fibres.
Ionic liquids, lyocell and nano/micro-fibrillated cellulose suspensions look promising as conversion methods for non-woods, Frazier adds. They require less purity than other manufacturing methods, and, consequently, can more easily integrate different fibre types.
As part of their study, the researchers explored a method to spin fibres from a hydrogel made of an undissolved nano/micro-fibre suspension.
After pulping the non-wood-based material in a treatment process that follows the same steps for making paper, the pulp is pretreated to oxidise the fibres, says Gonzalez. Next, mechanical shear treatment is applied to fibrillate the pulp to a nano- or micro-scale using homogenisation or microfluidisation.
'At a certain concentration, this fibre slurry forms a viscous, gel-like suspension, which can be regenerated into fibres upon extrusion from a spinneret into an acidic bath,' he explains. 'Post-treatments may also be applied after spinning to improve or alter fibre properties.'
Frazier explains the spinning method resembles the one developed by Finnish company Spinnova, which spins conventional and waste biomass cellulose feedstocks. However, the US study differs due to its sole focus on non-wood biomasses.
The researchers claim this method is highly efficient. It reduces the processing steps, the use of mechanical fibrillation minimises chemical use, and it draws on paper-grade pulp rather than higher-purity dissolving pulp as a feedstock.
However, Gonzalez acknowledges that using this new material requires adjustments to perfect the manufacturing process.
'Although this method may not require a high-purity cellulose pulp, it is still unknown if the presence of certain impurities could create defects or hinder mechanical properties of the final fibre,' he says.
Frazier explains that Spinnova is the only company applying this method to test its commercial viability and the US researchers are waiting to see its findings before exploring how to scale their own method up.
The team plans to undertake a broader assessment of different feedstocks in the laboratory to determine potential success at a larger scale.
'Each non-wood feedstock, even after pulping and purification, may have unique properties,' says Frazier. 'Certain feedstocks may have more challenges than others due to different starting impurity contents or different fibre-cell lengths and structures.'
Should this spinning method prove economically viable, Frazier says conventional fibre spinning mills would need to be retrofitted to make it operational.