Mineral ores study builds case for ‘responsible source’ of sand
A 12-month research project studying the physical, chemical and mineralogical characteristics of sand by-products recovered from mineral ores – also termed ‘ore-sands’ – has concluded that they could become a sustainable alternative for aggregates.
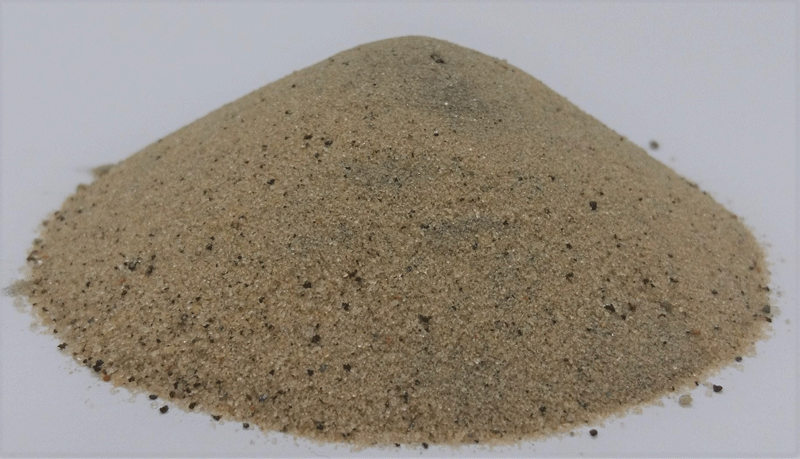
The joint research team from The University of Queensland’s Sustainable Minerals Institute, Australia, and the University of Geneva, Switzerland, has used a Brazilian iron ore processing facility as a case study.
They note that aggregates – sand, gravel and crushed rock – are the second most exploited natural resource globally after water, with an estimated 50Bt used each year.
The problem is that with soaring demand, the extraction of sand from rivers and coastal areas can be environmentally detrimental to local ecosystems and communities.
Meanwhile, an estimated 30-60Bt of mine waste are generated each year, so any innovations that could separate and repurpose mineral residues before they are added to the waste stream ‘would not only significantly reduce the volume of waste being generated but could also create a responsible source of sand’, says Professor Daniel Franks from The University of Queensland and project lead.
‘The University of Geneva comes from a sand sustainability perspective and understanding the importance of sand in biological systems and its use in global economies,’ adds Dr Artem Golev, part of the Queensland team.
He explains that one of the issues associated with grinding mineral ores is that the process produces relatively fine sand, limiting its potential applications.
However, innovations such as coarse particle flotation, which avoids overgrinding and enables mineral ore processors to create a coarser material, may help to address this limitation, broadening the markets for ore-sands.
The researchers’ interim, six-month report notes two barriers that need to be overcome before end-users will consider ore-sand to offset the use of naturally sourced sand. First, the recovered ore-sands must be able to compete economically with conventional materials, in particular, they need to be located close to logistical hubs and/or final markets. Second, they need to meet the technical requirements and standards set by different industries.
Mining company Vale was granted the first environmental licence to produce sand in 2020, and has adjusted its iron ore processing operations at its Brucutu mine in Minas Gerais, Brazil, to recover the sand by-product.
An independent, in-depth analysis of sand samples collected from full-scale production has been carried out at The University of Queensland to test the material’s suitability for potential applications in construction and elsewhere, such as for concreting, road building and land reclamation.
The tests confirm the material’s characteristics, including grading, particle shape and texture, and shear strength.
Golev says that the samples are essentially a quartz-based sand, comprising 90-91% silica and 8-9% residual iron oxides, with very minor trace elements.
‘It is a relatively fine, very angular sand, mainly in the range from 100-300µm, which may define where and how this material can be used,’ he adds. ‘Overall, it is compliant with the existing requirements for construction and industrial use.’
The final report’s conclusions will be presented at the 5th UN Environment Assembly in Geneva, held from 28 February to 2 March.