Material Marvels: High-technology swimwear
Where is the line drawn for ‘tech doping’ and what materials are used in competition swimsuits? Idha Valeur takes a deep dive into the pool of high-technology swimwear.
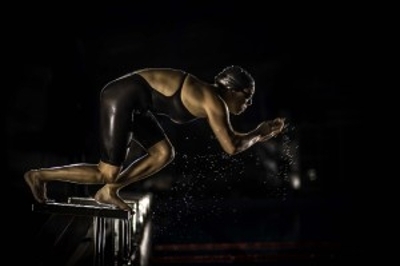
As a former competitive swimmer turned materials science journalist, I am now intrigued by the science behind the competition suits that I once used to nag my parents about before nationals. Unfortunately, I wasn’t lucky enough to get my hands on one of these impressive pieces of kit – I ended up with hand-me-downs from the older girls in my team. Since then, I have watched the new swimwear launches with awe and seen some banned as they made everyone ‘too good’, especially during the 2008 Olympics in Beijing, China.
From buff to knitted polymers
Before any swimwear entered the arena, it was more common to bathe naked than it was to wear any form of suit. It was not until the 18th Century, a body suit that reached the ankles and wrists was created to protect modesty.
A lot has changed in the sea of suits since the traditional large cotton varieties. Shape, size, fit, length and material are all factors that influence the best swimwear. Initially, natural materials were used. Oliver Logan, Analysis Lead – Biomechanics, Race Analysis and Skill Acquisition at British Swimming explains that suits were often made from wool and then moved onto silk in the 1920s and 30s. It was also in the 1930s that these garments became more figure-hugging. The next step was man-made fabrics and the introduction of ‘knitted fabrics with elastane composition for stretch and recovery properties,’ notes Logan.
Rory England, PhD Researcher at the Sport Technology Institute at Loughborough University, explains that the knitted polymer textiles often have a hydrophobic finish to repel water. ‘The composition of material is secretly developed by each manufacturer with the intention to outperform their competitors, especially in the run up to a major international competition. Suits are usually constructed with ultrasonically welded seams which are reinforced with heat-bonded polyurethane (PU) tape for strength.’
A tight squeeze
The fact that technology and innovation has made a splash in the pool is, of course, no real surprise but with it comes an abundance of choice and brands. The major breakthrough came in the first decade of the 21st century, Logan explains.
When it comes to being as fast as possible in the water, breaking world records and making a big impact in competitive swimming, the key is to actually make as little impact as possible in the water. Swimmers are in a constant battle to maximise buoyancy and adopt a more streamlined shape so as to not disrupt too much of the water surrounding them.
Then there is the big shark itself – drag and how to reduce it. Hence the need for suits that are tight, figure-hugging and a challenge to put on to make the swimmer more compressed, compact and streamline. An old changing room rule says that if the competition suit takes less than 30 minutes to put on, it is not small enough.
Logan explains that the benefit of high-technology swimwear is two-fold ‘through decreasing drag but also providing some energy return to the swimmer. The suits shape and mould the body to a more hydrodynamic shape to reduce form drag of the swimmer and also reduce the friction drag co-efficient of the body as the suits create less friction drag than the skin'.
England adds, ‘Materials choice determines or partially determines some of the key performance factors of a suit, including the hydrodynamic interaction with the water, fit on the athlete, compression on the athlete’s muscles and the suit’s durability/longevity.’
In the early 2000s, the material of choice was elastane nylon coated in Teflon, ‘then they moved to coating the suits in PU which created a very high hydrodynamic surface’, shares Logan. ‘These materials were used as they were efficient in reducing drag but also repelled water and were extremely lightweight. Another benefit was that the suits trapped air and created extra buoyancy for the swimmer [further] reducing form drag in the water.’
Too much of a good thing?
Any swimmer and non-swimmer will know the US competitor Michael Phelps, who did what no one had done before him – taking home eight gold medals at the Olympic games in Beijing in 2008. He, as many others, was wearing the Speedo LZR Racer suit, which was later mentioned by Time magazine as one of the best inventions of 2008. ‘94%. That's the percentage of Olympic swimming races won in Beijing by athletes wearing the LZR, a second-skin suit that's the first to be made with ultrasonically bonded seams’, the magazine wrote at the time.
‘The LZR, which was co-designed by NASA experts, comes with a built-in corset to improve buoyancy and is constructed with compression fabric that keeps muscles from vibrating in the water.’ There was much hype about the suit in the lead up to the Olympics and a lot of questions about it after – whether it gave an unfair advantage or not. An article published by NASA states that in the process of creating the LZR, Speedo tested almost 60 different materials in a wind tunnel at NASA's research centre in Langley, USA.
An article from Harvard University details how the new fabric for the LZR suit was better than previous versions and how the design further reduced the well-known problem of drag. It states, ‘LZR Pulse is the new fabric Speedo developed for the LZR Racer. It is an improvement over their FastSkinII … which contains small parallel grooves that emulate a shark’s skin. LZR Pulse consists of very fine microfibres of nylon and spandex in a high-density weave. It is extremely lightweight and water-repellent. It is also highly stretchable – it presses firmly against the body and creates the compression needed to streamline the swimmer’s body to reduce form drag, and to reduce entry of water between the suit and the body which can become a source of drag.’
Several other measures were taken to reduce drag and enhance the feel of being streamlined. The seams were ultrasonically-welded instead of sewn to eliminate bumps and the zipper was facing the body to again ensure the smooth surface on the outside. According to NASA, having welded seams reduced drag by 6%, whereas the ‘low-profile’ zipper, which was also ultrasonically bonded into the fabric, ‘generated 8% less drag in the wind tunnel tests than a standard zipper’.
The ruling hand of FINA
So where is the line drawn between impressive tech innovations enhancing performance and the so-called ‘tech doping’? In Fédération Internationale de Natation’s (FINA) eyes, the LZR suit crossed that line. In 2009, the international swimming federation released a new regulation to keep the focus and emphasis on the swimmers’ performances rather than the technology and innovations behind the suit they are wearing.
The new rules – agreed on 24 July 2009 during the World Championships in Rome, Italy – only allowed suits from waist to knee for men and from shoulders to knee for women. As well as the ban on full body-length suits, the rules also mentioned that the fabrics used in high technology-swimwear have to be either a textile or a woven material. Logan explains, ‘They should be constructed of natural and/or synthetic fabrics, and any treatment to the fabric should not close the overall open mesh structure of the base textile fabric. The fabric should also be permeable. The material should not be more than 0.8mm thick and should not exceed buoyancy effect of above 0.5N. Also, there are no zips or fastening systems and seams should be functional.’ These new rules took effect from 1 January 2010, leaving the LZR and similar suits a thing of the past. ‘The FINA swimsuit regulations were changed in an attempt to keep emphasis on swimmer performance rather than the suit technology. Amongst a number of regulations, they limit the static buoyancy of the suit when measured in the water and set a threshold for how water permeable the main panels of the suit must be,’ England says.
Several of the records set during 2009 were scrapped after the new rules were in effect and set back to the times achieved before the PU suits entered the arena.
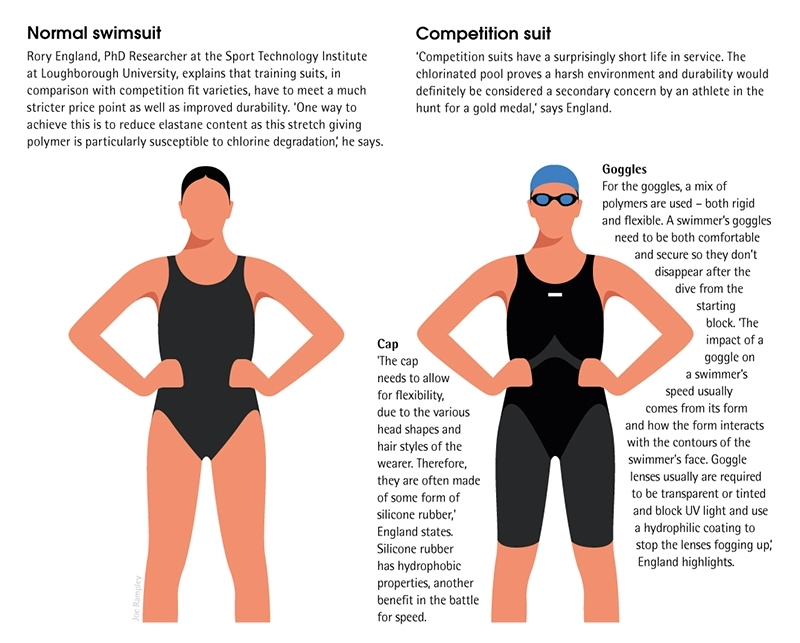
Competition fit
How the industry creates new innovative suits for competitive swimmers is often focused around the Olympic cycle and is a four-step process, England says. ‘1) Painstaking research and communication with materials suppliers to identify materials and innovation ideas that have a good chance of yielding benefit to the athlete. 2) Lab testing to determine and measure material properties deemed relevant to benefit performance. 3) Pattern design and fit testing to create a suit that complements the chosen materials and the form of the athlete. 4) Wear testing in the pool to get an in-depth understanding of overall performance.’
As to what the manufacturers and industry are currently experimenting with, Logan cannot say with complete certainty, but he believes they are looking into several areas of new fabrics including ‘stretch/recovery properties, friction drag of the materials and also treatments that they can apply to the materials’.
‘Of late, a big focus has been on providing a level of targeted compression and elastane seams in certain lower leg positions to facilitate energy return. Whether these actually do anything or is just marketing remains to be seen as the brands don’t tend to release any scientific testing they do,’ he adds.
Whatever the future might hold for high-technology swimwear and whatever the outcome when swimmers ‘take their marks’ – one thing is certain, they just have to keep swimming.