Magnesium alloys enhance heat removal in electronics
High-heat conductivity magnesium alloys that can reduce the weight of radiators and heat removal systems in electric vehicles and consumer electronics are being put forward by scientists in Russia.
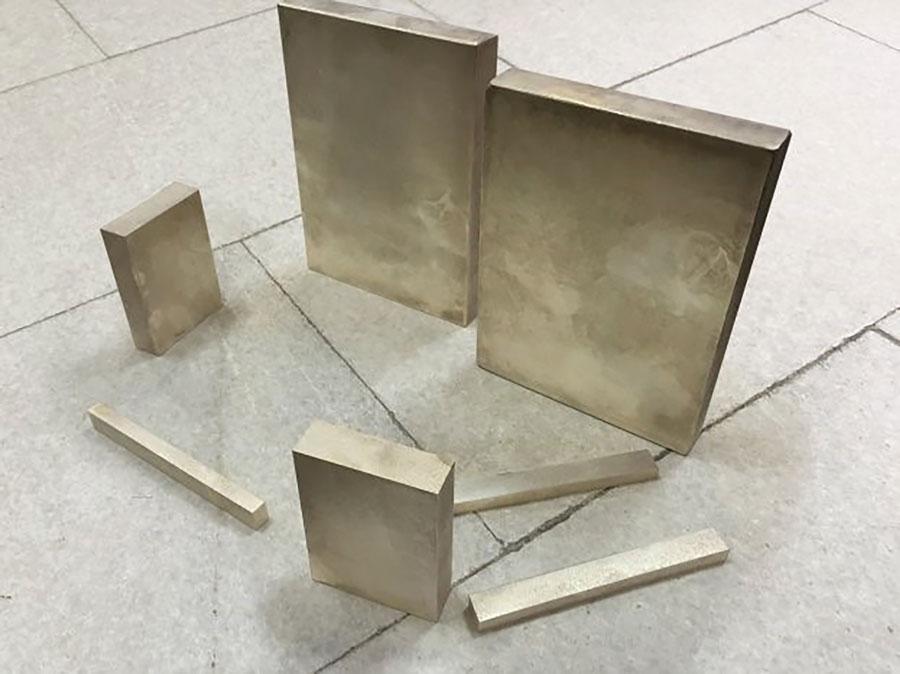
To meet the rise in demand for efficient heat removal, researchers from the National University of Science and Technology (NUST MISIS), in collaboration with LG Electronics, have created two new magnesium alloys which they say offer a weight reduction of one third.
The first is made up of magnesium, silicon, zinc and calcium (Mg-Si-Zn-Ca), giving it thermal conductivity of 126W/mK, which is 81% of the thermal conductivity of pure magnesium, with average strength characteristics. While the second alloy comprises magnesium, zinc, yttrium and zirconium with a higher strength and slightly lower thermal conductivity of 105W/mK – 67% of pure magnesium.
Vyacheslav Bazhenov, Associate Professor at NUST MISIS, says, ‘The composition of the alloys selected was based on…calculations of the phase composition using the CALPHAD (CALculation of PHAse Diagrams) method.
‘In the course of the development of highly heat-conducting magnesium alloys, the main concept was to provide strengthening of a magnesium solid solution with the help of elements that reduce the thermal conductivity of pure magnesium to the least degree. We also tried to achieve the formation of a large amount of the eutectic phases in the structure of the alloy, providing good casting properties.’
Bazhenov notes that aluminium heat sinks are most commonly used for heat dissipation, but due to global trends in environmental regulation and the need for lighter materials in electronics, alternative materials are being explored.
‘Among the materials that can provide a weight reduction compared to aluminium alloys for heat sinks, magnesium alloys and high thermal conductivity plastics can be distinguished.’
Using plastics is challenging due to their lack of strength, Bazhenov explains, while magnesium alloys traditionally tend to have low thermal conductivity.
‘For the development of the alloys, we used the alloying elements that have a minimal effect on magnesium thermal conductivity (zinc and yttrium), as well as elements that practically do not dissolve in magnesium (silicon and calcium). This combination helped us achieve the desired result, namely a combination of a high level of mechanical and technological properties while maintaining high thermal conductivity.
‘In contrast to currently used aluminium alloys with a density of 2.7 g/cm³, the developed magnesium alloys have a density of 1.8 g/cm³…At the same time, the mechanical properties (if we compare the casting aluminum and magnesium alloys) remain at the same level.’
The addition of calcium and yttrium also tackles another issue. ‘The main problem with the manufacture of products from magnesium alloys and their operation is their flammability…The oxide film on the surface of magnesium alloys is broken and provides no protective effect (low value of the Pilling-Bedworth ratio). We have decided to use the additives of yttrium and calcium, which replace a significant part of the magnesium in the oxide film and make it denser (increase the Pilling-Bedworth ratio).’
LG has tested the technological properties of the Mg-Si-Zn-Ca alloy at one of its facilities and samples have been obtained in an industrial high-pressure die casting machine. Bazhenov concludes, ‘The technological properties of the developed alloy turned out to be practically the same as the properties of the most widespread casting magnesium alloy in the industry (AZ91), which means that it is suitable for the manufacture of products of very complex shapes.’