Longer-life sacks aid international relief
More than 2,000 sacks made from 'more durable' multilayer structures are being field tested for distributing aid in the form of food and basic necessities.
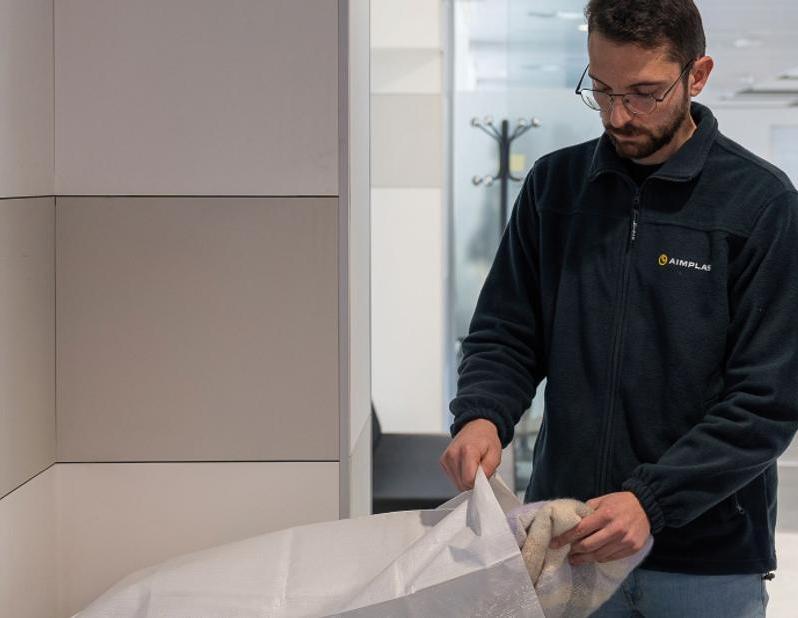
The bags are based on raffia fabric and recycled polypropylene layers, containing additives. The proprietary additive-based formulations use different thermal stabilisers to increase shelf-life.
The sacks have been fabricated for the International Committee of the Red Cross (ICRC) by AIMPLAS, the technological institute of plastics in Spain.
The development is part of a project funded by Innovation Norway and led by the ICRC, the United Nations High Commissioner for Refugees and the UN World Food Programme.
The aim was to find alternatives for sacks made from woven polypropylene that are used for packaging food and relief items.
While the formats of the bags vary, as do the additive composition, for different applications, the new sacks have the same multilayer structure.
AIMPLAS researcher Héctor Rivero explains, 'The bag has two layers. The inner layer – the main one and the thickest – is a textile layer. This is a polypropylene-based raffia layer. The outer layer – of low thickness – is a polypropylene-based film as a coating over the textile (raffia layer).
'[The] additional coating…was incorporated to the raffia bags production with the aim of providing better properties in terms of permeability and UV resistance. This process is based on an extrusion-coating process, incorporating a low-thickness film to the textile raffia structure.'
Rafia Industrial S.A has produced the multilayer sacks on an industrial scale, supplying different variations of the bags for field-testing in diverse environments amid challenging humanitarian work in Cameroon, India and Turkey.
More than 1,500 sacks have been used to transport wheat flour and dried beans to delay degradation from extreme environmental conditions. AIMPLAS has also formulated a second coating containing recycled material to make a further 500 sacks for distributing blankets.
Rivero notes that the trials are testing the mechanical, as well as UV, properties of the different formulations, when the bags are both empty and full. 'In this regard, we have carried out different studies to evaluate the performance of the bags, using irradiance levels equivalent to a range of one to five years.'
He continues, 'It is [also] important to manage the [balance between] durability/cost of the bag, which depends on the quantity and quality of the additives selected to be incorporated into the polypropylene structure. We are currently working on that.'
The field-testing will include a Life Cycle Assessment. One of the project aims was to boost reusability of the sacks and use recycled polypropylene. Rivero remarks that collection systems will be needed for the sacks at the end of their life to close the loop.
ICRC is currently working to scale up the products, says Rivero, and is looking for compounding and masterbatch companies to produce the polypropylene formulations. The charity is also seeking additional bag manufacturers.
Also participating in the project is Bangladeshi university AUST, which is developing a jute sack with a biopolymer coating. Giotti & SUPSI – a Swiss consortium of a university and consultancy – is meanwhile working on a natural fibre-based material treated layer-by-layer.