Local soil for local people – 3D printing houses
Applying locally sourced soil to 3D print load-bearing structures could be the next building block for more sustainable construction, say US researchers.
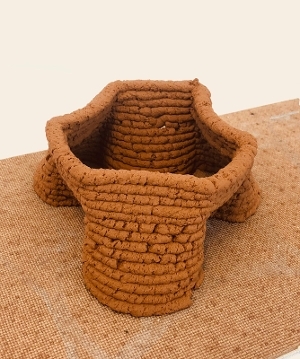
While additive manufacturing is not new to construction, there is scope to make the materials used in the process more sustainable, asserts Sarbajit Banerjee, Principal Investigator at Texas A&M University, USA. He envisions a future where local soil is 3D printed for local structures.
‘We have devised a method based on the use of silicate linkers to bind together soil particles and to reinforce them with fibrous additives to develop strength. We have further designed a “paste” from such a material that is amenable to being 3D printed and cures rapidly to form a cohesive structure that can sustain the weight of the next layer. The use of additive manufacturing methods is significant because it allows for realisation of versatile forms…suited to the needs of the location with great economy of materials use,’ explains Banerjee.
Using local soil in 3D printing, he says, allows for recyclable structures with a much lower carbon footprint, while forming bespoke buildings. In trials, the team used soil from a colleague’s backyard that was ground up to obtain a fine particle size distribution. The soil, silicate crosslinker and cellulose crosslinkers were mixed in a KitchenAid ‘to get a 3D printable clay mixture, adjusting the rheology of [it] to ensure printability. This mixture was then placed in the delivery system of a 3D printer. Nozzle parameters were then controlled to get the desired 3D printed structure’, Banerjee says.
He adds, ‘The compressive strength of the [burlewash series clay] composite was 3MPa, which represented a decent load-bearing capability for a clay composite. We have additional clay composites that are now approaching upwards of 30MPa and are competitive with concrete.’
One obstacle to tackle is variations in the soil, depending on where it is sourced. Banerjee notes that this element is incorporated into the research, whereby a palette of materials with different admixtures and crosslinkers can be produced based on the soil chemistry specific to the region/area.
‘We are seeking to develop a toolkit that with minor modifications will allow for local soil to be harvested and used for construction – mitigating the…environmental consequences of clinkering and high-energy grinding associated with concrete production,’ Banerjee explains.
He adds that further work is required to enhance the strength. ‘This will enable us to be able to print different structural elements. Further down the road, we aim to provide extended stability to the composite via the incorporation of fibre and integration with rebar. We are also interested in elaborating these methods to regolith to enable the design of landing-pads on lunar and Martian soil.’