Liquid-metal catalyst makes ammonia at reduced pressures
A way of making ammonia using a liquid-metal catalyst requires one-fifth less heat and 98% less pressure than conventional processes, say the inventors at RMIT University, Australia.
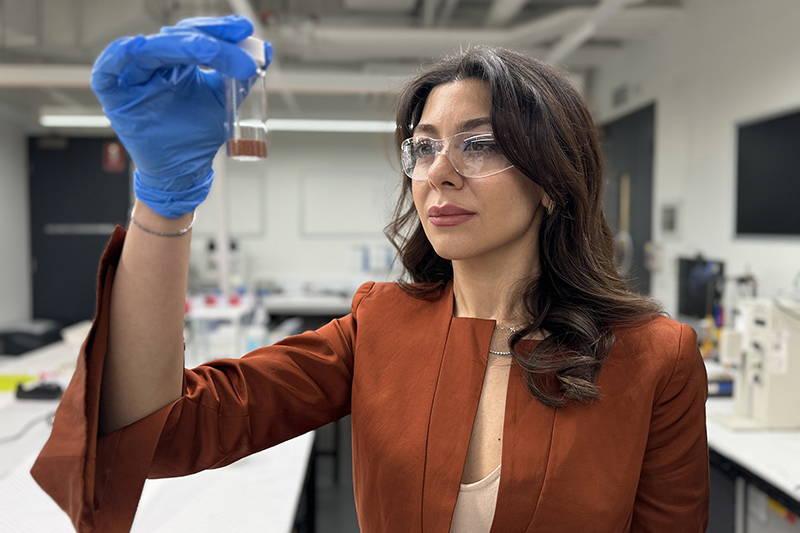
Ammonia is used in fertiliser to grow food, but also plays a role in clean energy as a carrier to safely transport hydrogen.
However, global ammonia production is said to consume more than 2% of energy and produces up to 2% of carbon emissions worldwide, mostly using the century-old Haber-Bosch process for splitting nitrogen and hydrogen into ammonia.
'Ammonia production worldwide is currently responsible for twice the emissions of Australia. If we can improve this process and make it less energy intensive, we can make a large dent in carbon emissions,' says Research Fellow and study lead Dr Karma Zuraiqi.
The team says ammonia from the traditional Haber-Bosch process is also only viable at huge facilities, whereas their approach could suit large and small-scale decentralised production. Small amounts could be made cheaply onsite at solar farms, further reducing emissions and transport costs.
The liquid-metal catalyst comprises 2% copper and 98% gallium. These are cheaper and more abundant than the precious metal ruthenium used in current approaches, notes Zuraiqi.
The copper and gallium are turned into tiny liquid-metal droplets – named ‘nano planets’ for their hard crust, liquid outer core and solid inner core structure.
Using liquid metals allows the researchers to move the chemical elements in a more dynamic way to the interface and enables more efficient reactions.
'Copper and gallium separately had both been discounted as famously bad catalysts for ammonia production, yet together they do the job extremely well,' notes Professor Torben Daeneke, also at RMIT University. In tests, gallium broke the nitrogen apart, while copper helped to split the hydrogen.
The tests can run at much lower pressure (4bar), as the catalyst works differently at an atomic scale. 'Rather than breaking the triple bond between the two nitrogen atoms first, the nitrogen molecule is adsorbed onto the liquid surface,' explains Daeneke. 'After this, the ammonia molecule is assembled step by step, adding one hydrogen at a time. This is in part possible due to the fast diffusion that is possible at the liquid-metal surface.'
The catalyst has been found to be stable for several days, and while it should be recyclable, the researchers need to conduct further experiments on this.
Optimised at 400°C and 4bar in the lab, the process will be upscaled and designed for even lower pressures, but also should yield more ammonia at higher pressures, says the team.
RMIT is leading commercialisation of the technology, which is based on a jointly filed patent application by RMIT and the Queensland University of Technology.
Daeneke envisages different routes to market and says there might be an advantage to operate at high pressures to replace noble metal versions that operate at large facilities. 'In these settings, our catalyst may turn out to be much more effective than the conventional ones due to a lower activation energy.'
Another application could be for ammonia production in remote settings, such as a farm, with excess renewable energy being used to make hydrogen and then ammonia, which could be deployed onsite or sold on.