Lightweight composite boom heads for space
Flexible electronics have been integrated within a three-ply, self-deployable, composite boom.
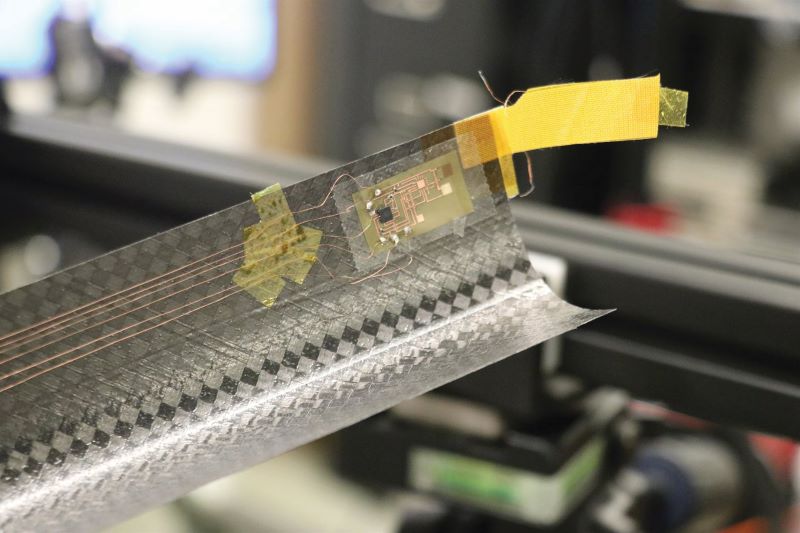
The Virginia Tech, three-unit, CubeSat with the multifunctional boom – weighing around 20g – is aiming for launch this year.
Being lightweight is essential for space structures, particularly for tools used on small satellites.
Each layer of the carbon-fibre-reinforced polymer (CFRP) boom is 50μm-thick, making the whole structure 150μm-thick – as thin as a sheet of paper. It is rolled up like a tape measure with stored energy in its coils until it unfurls on its own in space.
The flexible electronic patch on the boom uses 25μm-thick polyimide as the substrate, with the copper electrical circuit 12μm-thick. The wires embedded in the middle CFRP layer are standard copper wires coated with enamel.
The patch weighs only 0.05g, making up only 0.25% of the structure’s total weight.
'It’s difficult to get commercial electronics integrated into these super-thin structures,' says Professor Xin Ning at the University of Illinois, USA, who led the work.
'There were a lot of engineering constraints adding to the challenge of making the electronics able to withstand the harsh environment of space.'
The thinness needed for this type of product creates two challenges, Ning explains. 'One, we need to make sure the electrical data and power lines/wires embedded in the thin, composite boom do not alter the boom cross-section or delaminate the material, and two, the integrated electronics must be flexible so that they can deform with the boom during furling/unfurling.'
To overcome the first challenge, they needed to ensure the wires were at most ~50μm thick. The wires must be longer than 4ft and have electrical encapsulation layers. They tried multiple fabrication methods before testing a few commercial options and found a type of thin wire that worked best and had consistent, reliable quality.
For the second challenge, they developed fabrication methods to make thin, flexible, electronic circuits using micro-fabrication and electronics integration techniques. In their design, the substrate of the electronics was below 40μm so that they can deform with the boom.
The multifunctional boom installed in the CubeSat is designed to unfurl in space using a motor in a controlled manner. However, the structure is also capable of being self-deployed by releasing elastic strain energy.
During deployment or vibration, the boom tip moves, creating accelerations and rotations, which will be captured by a motion sensor. The data can then be used to inversely analyse the deployment and vibration.
The process to make the boom involved quite a few iterations and collaborative efforts between Ning’s team, NASA Langley and Virginia Tech. They used a thermal-vacuum chamber to verify the devices can function under outer-space thermal and vacuum conditions.
While on-ground deployment and vibration tests ensured the devices can survive various folding and deployment motions.
As well as creating a multifunctional, lightweight boom, they have also 'generated systematic fundamental knowledge on the structural mechanics of such structures', according to Ning.
The team are working on more advanced, multifunctional booms that can survive longer in low-earth-orbit conditions.