LEGO-inspired glass bricks for circular construction
An MIT team has made 3D-printed glass bricks that can disassembled at the end of a building’s lifetime and reassembled into a new structure.
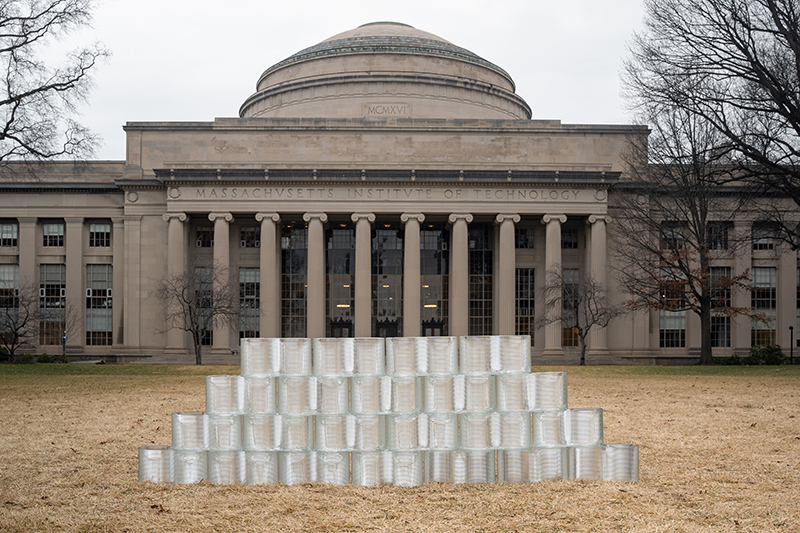
Sustainability and circularity are major areas of focus for the building industry, while a significant amount of post-consumer glass material is still not recycled. Now a set of LEGO-inspired manufacturing processes might offer a solution to both problems –
A team of engineers at Massachusetts Institute of Technology (MIT), USA, has developed three manufacturing processes to fabricate interlocking glass masonry units with dry-mounting interlayers, which could provide a circular building material.
The team has used a combination of 3D printing and casting to melt the glass and print custom shapes without moulds, reducing waste. Working in collaboration with Evenline, an MIT-spinoff, they used a glass printer that contains a furnace to melt crushed glass bottles into a molten, printable form.
The work was done in parallel with another paper that focused on printing with recycled window glass and recycled bottle glass.
The team printed prototype glass bricks in layered patterns using soda-lime glass. Each printed brick was incorporated with two round pegs, similar to the studs on a LEGO brick, to enable them to interlock and be assembled into larger structures.
In mechanical testing, a single glass brick withstood pressures similar to that of a concrete block. As a structural demonstration, the researchers constructed a wall of interlocking glass bricks. They envision that 3D-printable glass masonry could be reused many times over as recyclable bricks for building facades and internal walls.
The three different methods are customisable. Lead author Daniel Massimino reports that, 'Average strengths varied between each process, but the better performing manufacturing processes had comparable crushing strength to ceramic and concrete masonry units.'
Those bricks were made mostly from printed glass, with a separately manufactured interlocking feature made from a different material, which is attached to the bottom to prevent scratches and cracks. These can be removed and recycled when the structure is dismantled and the glass bricks remelted and reformed.
Kaitlyn Becker, Assistant Professor of Mechanical Engineering at MIT, highlights that, 'As long as it’s not contaminated, you can recycle glass almost infinitely.'
Each method could be improved for industrial use with further development. However, Becker also notes that, 'Glass is a complicated material to work with. The interlocking elements, made from a different material, showed the most promise at this stage'.
The team believes the process is close to scalability. They report, the 'technology excels in producing scientific specimens and architectural-scale masonry units, with the capability to create objects up to approximately 30cm in all dimensions'.
One option going forward would be to scale the printer to accommodate customer requests for larger objects measuring up to 1m3. Another option would be a specialised printer for large sheets of window glass (measuring 1.2m x 2.4m), enabling deposits of the intricate printed patterns required for glass faҫades and other architectural applications.
A third possibility is the integration of new thermal elements to increase the system’s operating temperature from 1,150°C to 1,800°C, allowing them to print higher-melting-point, lower-thermal-expansion terrestrial glasses like borosilicate.
For now, the team has achieved its goal to make a system of interlocking glass blocks.
The team cites Olafur Eliasson's Fjordenhus, a building made for the Lego family using differently sized and shaped bricks, as well as glass features, as a specific inspiration.