Layer by layer
The importance of taking a materials-first approach to embed sustainability in additive manufacturing.
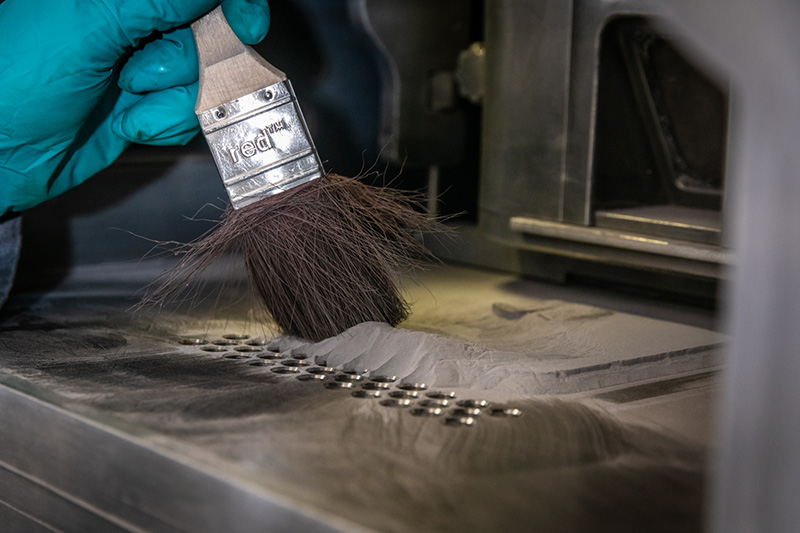
Today, one of the most significant challenges that industries face is the conundrum of how to balance production needs with the pressing demand for sustainability.
Traditional manufacturing methods often generate significant waste through subtractive processes. According to Chinese manufacturer 3ERP, computer numerical control machining can have material utilisation as low as 10%.
By creating products layer-by-layer using either laser powder-bed or binder jet printing techniques, additive manufacturing (AM) allows for more precise material usage – with the potential of less waste and fewer emissions compared to traditional manufacturing methods, while still producing high-quality goods.
This can be especially beneficial for the automotive and aerospace sectors, where reducing weight through optimised designs directly leads to lower-fuel consumption and reduced carbon emissions.
Advanced manufacturing approaches like AM are therefore already playing a crucial role in enabling businesses to reduce their carbon footprint while maintaining operational efficiency. However, this trend needs to accelerate over the coming years. And it is essential that manufacturers innovate to remain competitive.
In the race towards more sustainable manufacturing, reducing waste is not just about cutting excess material, it’s also about rethinking processes at their most fundamental level.
In a bind?
In conventional binder jet printing, binders hold metal or ceramic powders together to form a 3D structure before sintering.
Conventional binder jet printing relies on polymer-based binders, which must be removed in a furnace after printing. This debinding process is time-consuming and can lead to shrinkage, distortion and porosity as the polymer burns away. These issues require extensive post-processing and can compromise the final part’s integrity.
A more advanced approach rethinks the role of binders by incorporating functional metal and ceramic materials instead of relying solely on polymers. Rather than burning out completely, a significant portion of the binder remains in the final part, reducing shrinkage and distortion while shortening post-processing time.
These reactive binders are designed to react with the powder bed to form strong metallic or ceramic bonds, further enhancing green part strength and improving overall part functionality.
This method enhances structural stability and minimises defects caused by material loss.
Beyond improving dimensional accuracy, functional binders also influence the microstructure of the final component. By embedding useful properties directly into the material, this approach can enhance characteristics such as electrical conductivity, thermal stability, or mechanical strength. This allows for greater control over material performance, expanding potential applications in industries where precision and reliability are critical.
For example, binders with in situ nanoparticle formations could bind the powder together with a non-sacrificial material. Nanoparticle formations can in turn be controlled to create varied microstructure and properties, such as being able to control the microstructure of a 3D-metal component spatially across a 3D part.
Such functional binders can also enable multi-material printing, such as the production of an aluminium-printed block with an internal aluminium-copper alloy component.
Furthermore, binder and ink formulations can be tailored in synergy with the powder beds and print-heads used in the process, reducing the need for excess binders, expensive powders and lengthy post-processing steps.
By eliminating the drawbacks of traditional polymer-based binders, these innovations streamline the 3D-printing workflow and enhance the quality of printed components. It represents a shift towards more efficient and advanced manufacturing techniques, leading to stronger, more functional parts with fewer processing challenges.
And by engineering materials that require less energy and produce fewer by-products, overall improvements in efficiencies are seen while maintaining high-performance standards.
Atomik AM’s patented technologies include in-flight ink mixing for enhanced material flexibility and reduced waste, coated particles for multi-material integration, and multi-powder delivery for scalable production of complex, energy-efficient devices.
The firm is working with automotive companies to print large parts for lightweighting of components. It is also collaborating with the aerospace sector on 3D-printed heatsinks that have controlled microstructure to improve overall efficiency and thermal conductivity in electric vertical take-off and landing aircraft.
One man’s aluminium…
Waste often occurs at the microscopic level in AM, where inefficiencies in powder deposition, binder distribution, or curing processes lead to material inefficiencies.
Waste in binder jet printing can be minimised by ensuring the binder serves a functional role beyond merely acting as a temporary adhesive that must be burned out post-printing. This reduction in waste can be achieved by incorporating additives into the binder, such as particles up to 1µm and organometallic solutions.
These additives enhance material properties by integrating with, and reacting chemically within, the powder bed, eliminating the need for burnout and improving the overall functionality of the final part.
Advances in binder jetting also overcome waste by reducing the need for traditional spherical powders that are often resource-heavy and energy intensive to produce.
Unlike sacrificial binders, these functional binders contribute to the final material properties by filling the porosity of the powder bed, eliminating the need for highly spherical powders and reducing the energy required for powder production. While powders from cheaper sources and waste fractions from other manufacturing processes can also be used, lowering cost.
Additionally, functional binders lower processing temperatures and shorten post-processing times by incorporating sintering agents within the binder itself. These additives facilitate densification during heat treatment, reducing the overall thermal energy and time required for sintering, leading to a more efficient and cost-effective process. This saves overall energy and cuts down waste material using a circular economy approach, helping companies meet their sustainability targets more effectively.
Although, the binder jet industry aims to recycle most of its unused powder, not all of this material can be reused, and some conventional binder jet processes reuse as little as 4% of the powder.
In the pursuit for developing more sustainable manufacturing processes, Atomik AM has partnered with Cygnus Atratus, a UK-based fuel-cell and hydrogen production technology developer. The goal is to take the waste from Atomik AM’s aluminium printing processes and use it in Cygnus Atratus’ fuel cells in a project led by Luke Evans, an engineer and PhD student at the University of Liverpool, UK.
Instead of commonly used aluminium alloys, Atomik AM uses pure aluminium powders sourced in the UK for 3D printing, opening up superior thermal management possibilities for energy applications. Pure aluminium offers higher thermal conductivity and lower impurity content as it has fewer lattice defects and impurity phases, allowing for more efficient heat dissipation. This makes it ideal for applications like heat sinks, thermal interface materials and cooling components in electronics and aerospace.
In this project, the waste that is produced from Atomik AM’s printers is being analysed.
If the initial stage of the project is successful, it is hoped that additional funding can be unlocked to design, build and test a conversion machine.
Cygnus Atratus would then build the prototype machine in conjunction with Atomik AM, to work towards creating a minimum viable product, paving the way for more sustainable manufacturing processes that transform waste into clean energy.
Broadening horizons
In addition, Atomik AM seeks to modify and optimise existing additive manufacturing machinery, to broaden the pallet of materials manufacturers can process without needing to invest in entirely new equipment.
As part of a three-month project funded by a global multinational company, Atomik AM has developed an aluminium binder jet printing process to control printing at a molecular scale, allowing voxel-level influence over the final part as well as for wider material specifications.
By improving the properties of materials at every step of the process, manufacturers can produce the quantities they need with minimal waste – a capability that’s reshaping the way industries think about production.
Through cutting energy consumption by up to around 50% compared to traditional methods, businesses can reduce their carbon footprint, saving up to 2,500kg of CO₂ per year per machine. This results in significant environmental impact reduction across industrial sectors, supporting a more sustainable future.