Laser welding solar panels increases recyclability
Femtosecond lasers that can weld glass-to-glass make solar modules easier to recycle, says a US team.
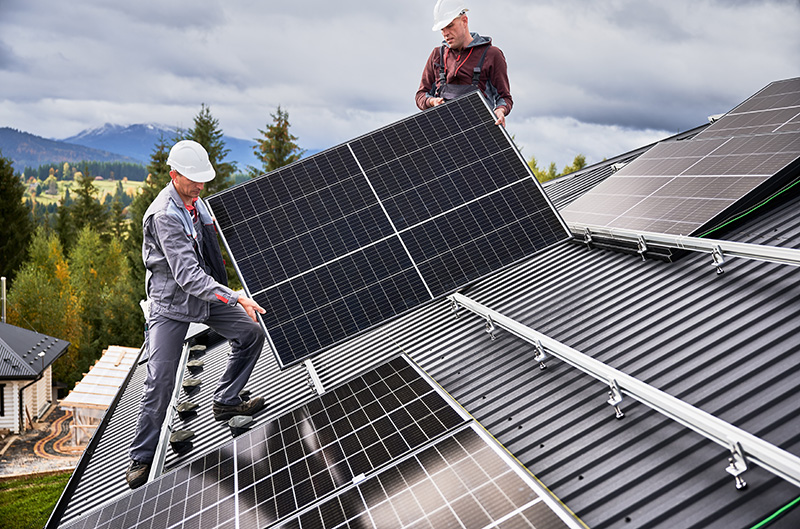
Semiconductors in solar modules are typically sandwiched between two sheets of glass laminated with polymer sheets.
This research reportedly shows that laser welds between glass are as stiff as the glass itself, negating the need for laminated plastic sheets for stiffness, which have been hampering recycling efforts.
Instead, at the end-of-life, the laser welds can be shattered, the glass and metal wires can be recycled, and the silicon reused.
The weld can reportedly be used on any type of solar technology – silicon, perovskites or cadmium telluride – because the weld heat is confined to a few millimetres from the laser focus.
The team comprises researchers from the US National Renewable Energy Laboratory (NREL) and Trumpf Inc, a California-based company that makes femtosecond lasers.
The technology uses a short pulse of infrared light that melts the glass to form a strong, hermetic seal.
The short bursts of photons last a femtosecond – 10-¹⁵ of a second – which is a million times faster than a nanosecond laser. For the same power, the femtosecond laser effectively has a million more photons per burst, explains David Young, Senior Scientist and Group Manager at NREL.
He says the large number of photons changes the fundamental absorption process in the glass from linear to non-linear, allowing the glass to absorb more light, which heats it up and produces a weld.
The proof-of-concept involved focusing the laser at the interface of two sheets of glass and welding them together.
The team says with proper mounting and modification to the embossed features of the rolled glass, the welded module can be stiffened enough to pass static load testing.
Young notes that the module will need redesigning in many ways to use the femtosecond laser welds.
The elimination of matched polymers on the module’s inside does reduce the amount of light transmitted to the cells, Young admits. To overcome this, they propose adding an anti-reflection coating to the glass inside. '…it’s a very simple optics issue,' Young expands, 'but not having plastics between the glass and the cell reduces unwanted absorption of low wavelength light in the polymers that heats the module and reduces its efficiency'.
NREL’s research is reportedly the first to use a femtosecond laser to form glass/glass welds for use in a solar module. A different type of edge sealing using nanosecond lasers and a glass frit filler was tried in the past, but the welds proved too brittle for use in outdoor module designs.
Young says, 'Our design allows for a hermetic seal that will keep moisture from migrating between the glass sheets and to the semiconducting cell. Many degradation modes seen in solar modules are caused by moisture, so we feel our design will likely last much longer in the field.'
Having analysed the technoeconomic factors for the solar industry to adopt the technique, the research team does not foresee any apparent showstoppers in terms of equipment, cost, energy input and throughput.