IOM3 Sustainable Future Awards preview
IOM3 Sustainable Future Awards are back for a second time. In November, we will recognise and award excellence in the transition to a low-carbon, resource-efficient society. Find out more about the finalists and the judging panel, with thanks to our sponsor, Cornish Lithium.
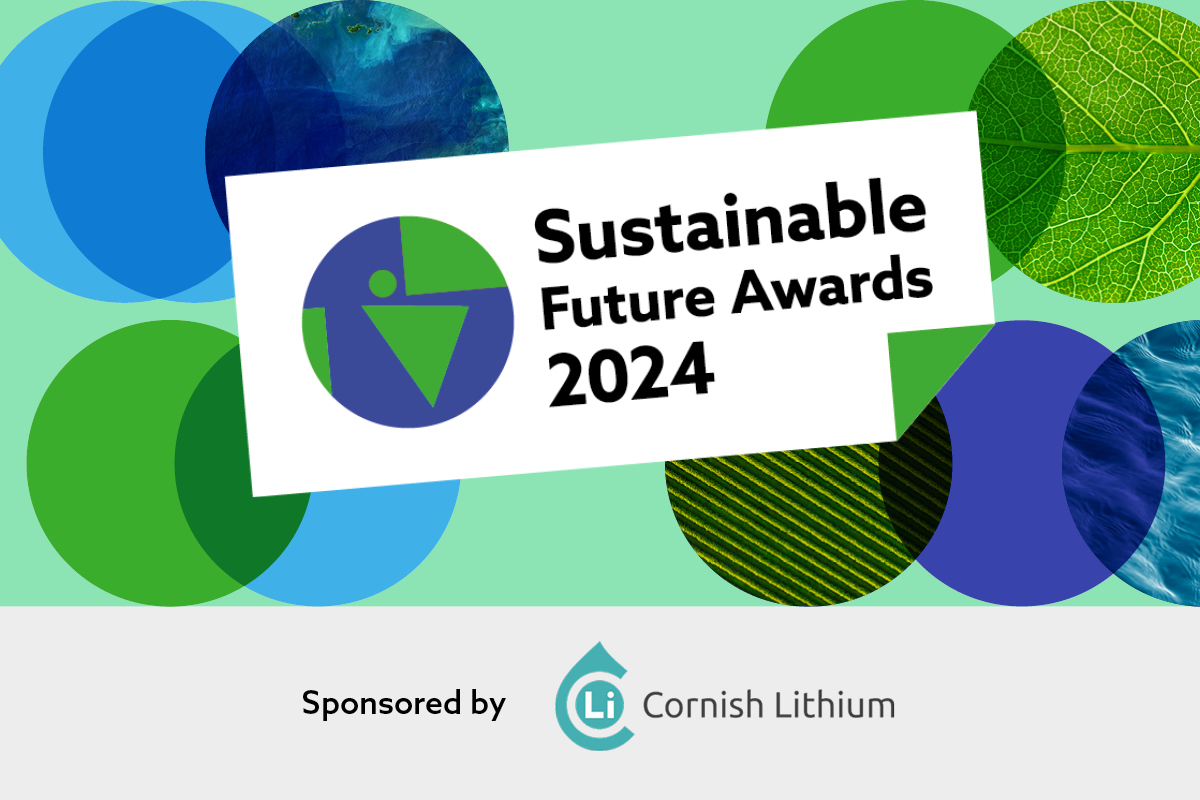
IOM3 is committed to supporting professionals in materials, minerals and mining to be champions of the transition to a low-carbon, resource-efficient society. This is part of our endeavour to be leaders in the global network for the materials cycle, at a time when current and future society depend fundamentally on materials that are responsibly extracted.
The 2024 IOM3 Sustainable Future Awards, sponsored by Cornish Lithium, offers a platform for knowledge exchange, promoting organisations and individuals that are advocating the need for greater circularity in the extraction, processing and use of natural resources.
Adjudicated by an independent panel of experts to recognise pioneers in sustainability, equality, diversity and inclusion, and the promotion of circular practices, the Awards will culminate at a ceremony in London in November this year.
Judging panel
- Dr Emma Wilcox CEnv FIMMM FCMI CMR, Chief Executive for the Society for the Environment
- Dr Sarah Connolly CEng FIMMM, Strategic Partnership Lead, Glass Futures
- Jude Allan MIMMM MInstPkg(Dip), Chair of the IOM3 Packaging Society and Interim CEO of ORNL
- Dr Cynthia Adu CEnv MIMMM, Sustainability Manager at PACT and IOM3 Strategic Advisor on Skills
- Mark Miodownik MBE FREng CEng HonFIMMM, Professor of Materials & Society, UCL
- Roger Harrabin, Journalist specialising in environment, energy and transport
The finalists are as follows.
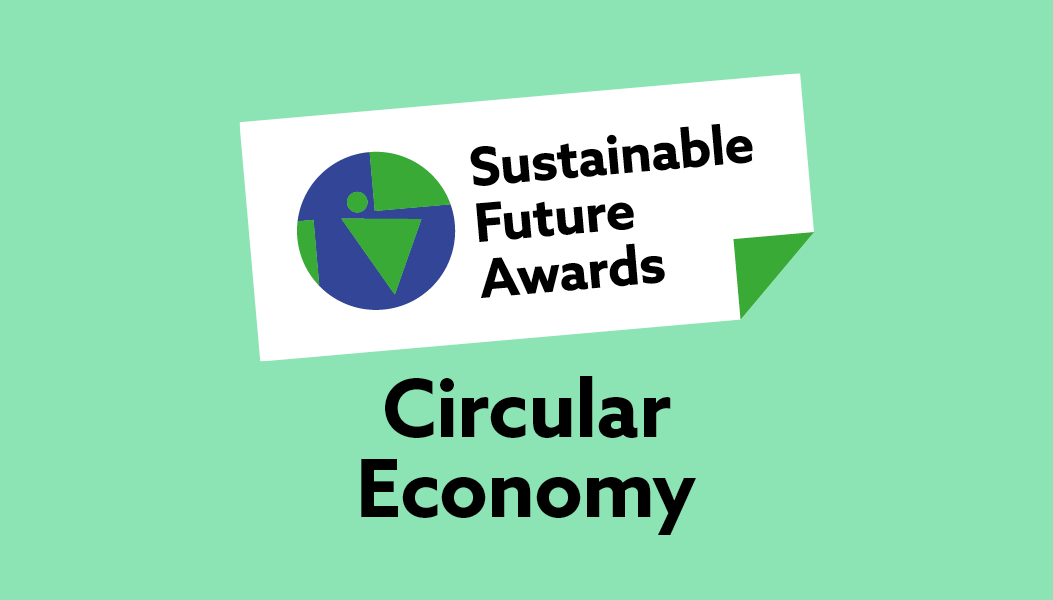
Circular Economy
DurInno
DurInno is shortlisted for 3D printing biocomposites based on polylactic acid (PLA) and Durian Skin Fiber (DSF), extracted from waste durian fruit. PLA serves as the matrix material, while DSF is the reinforcing filler.
The composite material combines the environmental advantages of PLA, a biodegradable thermoplastic material from renewable sources, with the abundant agricultural waste of durian fruit in Malaysia, addressing both sustainability and waste management concerns.
DSF, being a natural fibre, has enhanced mechanical properties, including increased tensile strength and stiffness. The synergy between the two components results in a robust and environmentally friendly 3D printing filament.
The development process involved careful optimisation of DSF treatment methods, ensuring compatibility with PLA and efficient dispersion within the matrix. This synergy facilitates fabrication of intricate and durable 3D-printed objects, making it an ideal candidate for various applications, such as packaging, engineering components and leisure.
Elmery Ltd
Elmery provides a patented metal recovery technology for metal refineries to better circulate precious metals and platinum group metals. These are currently refined through processes with significant chemical consumption, and industry has been looking for innovative electrochemical solutions that use process data to further improve refining operations.
Elmery has developed, and is implementing on an industrial scale the patented EDRR methodology. The technology is designed to recover metals from the process and side streams, but also from waste streams with very low metal concentrations. It also enables harmful element removal from wastewaters, waste streams or inter-process streams.
Refineries will therefore be able to reduce, or eliminate, the amount of chemicals consumed in conventional processes, while also minimising installation and carbon footprints with efficient and smart use of energy.
EPFL, Switzerland
Drs Yunting Wang and Yudong Xue at EPFL Switzerland have developed an electrochemical recovery and regeneration process for industrial and urban solid waste, which could eliminate millions of tonnes of hazardous waste annually while reducing the need for metal extraction from ores.
Electrochemical leaching, enhanced by reactive oxygen species and the cyclone electrowinning process, achieve high-purity metal recovery with improved efficiency.
The technology recovers valuable metals like copper, vanadium, selenium and titanium from waste materials, such as printed circuit boards and spent selective catalytic reduction catalysts, significantly reducing energy consumption compared to traditional methods.
Collaborations with industry partners have ensured practical application and scalability of the scientists’ innovations. Their commitment to sustainability is further demonstrated through extensive publications, patents and public engagement efforts.
Freefoam Building Products
Freefoam is a manufacturer of a wide range of PVC-UE fascia and soffit products, including gutter systems, external cladding and interior panelling systems for the building industry in Ireland, the UK and mainland Europe. They run a closed-loop production system and, since 2015, have replaced 8,200t of virgin material with their own recycled PVC.
Freefoam also offers a take-back scheme for customers to return obsolete products and packaging for recycling into new products and packaging. This end-of-life solution brings circularity to offcuts at installation and demolition stages. With the take-back scheme, they are bridging the gap of long broken logistical links in the waste sector and with end-users, and proving PVC is a resilient material of the future.
The firm also uses a web-based collaboration tool to manage circular economy projects across both its Cork and Northampton manufacturing plants, allowing it to set ambitious targets like '100% reuse of all PVC material entering our production facilities, in the manufacture of finished goods'.
HyProMag Ltd
HyProMag is establishing short-loop recycling facilities for neodymium, iron, boron (NdFeB) magnets at Tyseley Energy Park in Birmingham, UK, and other locations. These sites will be using the patented Hydrogen Processing of Magnet Scrap (HPMS) process to provide a sustainable solution for the supply of NdFeB magnets and alloys for a wide range of markets, including automotive and electronics.
Short-loop magnet recycling is expected to have a significant environmental benefit, requiring an estimated 78% less energy versus primary mining for magnet production.
The plant at Tyseley Energy Park is being developed together with the University of Birmingham, with a minimum capacity of 100tpa NdFeB.
One Bin to Rule Them All, University of Manchester, UK
One Bin to Rule Them All is an interdisciplinary project using behavioural understanding and new economic models to reshape recycling practices, mapping household contamination and influencing UN Plastics Treaty negotiations.
With over 39 different bin regimes across 391 local authorities in the UK, household recycling is complex and unregimented. Often, an item can be recycled in one local authority, but not in a neighbouring one. This lack of standardisation causes confusion and complications for waste recovery facilities.
One Bin to Rule Them All, funded by UK Research and Innovation’s Smart Sustainable Plastics Packaging Fund, brings together academic experts and leverages expertise from over 30 industry and policy partners across the supply chain. This includes the Sustainable Materials Innovation Hub, the Tyndall Centre for Climate Change Research and the Sustainable Consumption Institute. The research team aims to improve plastics recycling by developing ‘one bin’ to hold all plastic-like items, improve UK ‘binfrastructure’ and create more usable recycled plastics that can be fed back into a circular economy.
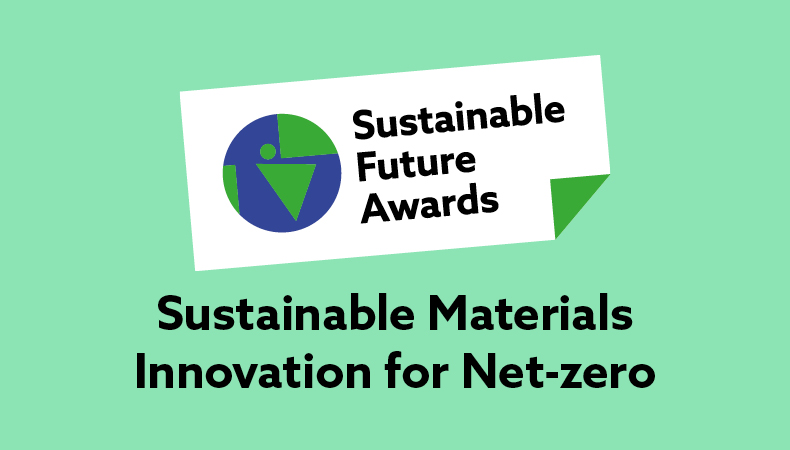
Sustainable Innovation Materials for Net-Zero
Denimolite Ltd
Denimolite Ltd is combatting the UK’s staggering volume of denim waste, estimated at 260,000t annually.
Conventional waste disposal methods for polycotton blends involve incineration due to the labour-intensive process required to separate cotton from man-made fibres.
Denimolite Ltd has developed a proprietary method to efficiently process polycotton waste into new denim composite products, countering the fast fashion trend that leads to excessive waste. Its consumer donation programme encourages customers to give back their unwanted denim. This reduces the burden on municipal recycling systems and the emissions from polycotton waste.
The manufacturing process operates at lower temperatures with a bio-resin. Through the introduction of a super-sized press, the company can efficiently process 50-100kg of fabric waste at a time, diverting this substantial mass away from landfills and incinerators into construction panels for furniture, decorative wall cladding and other applications.
Ecobelt
Ecobelt is challenging the global conveyor belt market by fostering technology and partnerships to achieve carbon neutrality and a circular economy.
Conveyor belts are generally multi-material composites of single- or multi-layer laminates. This makes them almost impossible to upcycle, downcycle or recycle. The manufacturing process of the materials, as well as the production of the belts themselves, consume huge natural resources while producing significant greenhouse gases throughout all the stages from cradle to grave. It is estimated that more than 80% of belt failure is attributable to splice failure, therefore, if the belt splice is no longer prone to fail, its expected lifespan will be considerably extended.
AnnStuMax is a new belt splice technology that has been proven to outlast a conventional spliced belt by a factor of 12. The technology increases the strength of a belt joint beyond that of the belt carcass itself, therefore eliminating the historical ‘weak link’ that the splice has always been. This is because a splice is typically only one-third the strength of the belt carcass in both tensile and puncture resistance.
Lucideon
The safe and long-term storage of radioactive waste is a critical challenge for the nuclear industry. Traditional concrete encapsulation methods, while effective in containing contamination, have limitations. Lucideon has explored a novel geopolymer technology called MALLET (MIDAR-Augmented Lower-cost Lower-carbon Encapsulation Technique), for low-carbon radioactive waste management.
MALLET is a collaborative effort between Lucideon and NUVIA UK. The development involves rigorous testing to ensure waste containment integrity. This includes evaluating the formulations against specific criteria, such as crack resistance and waste leachability under submersion conditions.
By offering a lower-carbon footprint, higher waste-loading capacities and resource utilisation, this geopolymer technology paves the way for a more sustainable and efficient approach to nuclear waste management.
Material Evolution
Traditional Portland cement (OPC) production is a major contributor to greenhouse gas emissions. Material Evolution tackles this issue head-on with its concrete formulations.
Their focus lies in waste-derived feedstocks and recycled industrial by-products. By employing a patented alkali fusion technology, Material Evolution enhances the reactivity of these feedstock pozzolans without heat, generating >85% less CO2 than OPC production. These materials can be used as supplementary cementitious materials and as AACM cements.
The company has raised a £15mln, oversubscribed, Series A funding round to scale the cement production process.
They are building a large-scale manufacturing plant in Wrexham and have a pilot plant and R&D lab in Middlesbrough.
Material Evolution champions sustainable construction by dramatically reducing reliance on OPC. This translates to a significantly lower carbon footprint for the industry. Secondly, Material Evolution embraces circular economy principles. Recycled materials find new life as valuable pozzolans, diverting waste from landfills and providing a sustainable resource for construction.
WasteReBuilt, Cardiff University, UK
WasteReBuilt is a circular approach to transform waste sand into a resource for the built environment, supported by Weir Group Plc, Dragon Alfa Cements and the Cast Metal Federation. The project investigated the suitability of waste foundry sand, generated by the cast metal industry, as a replacement of fine aggregate in concrete.
The two most pressing issues related to concrete production are the carbon-intensive production of cement, and extensive raw material extraction and usage. The UN reports that 40-50Bt of aggregate are extracted annually, with over half consumed by the concrete industry.
The research demonstrates that replacing fine aggregate in concrete with waste foundry sand enhances the mechanical, physical and durability properties of the resulting concrete.
This, in combination with cement replacement, will decarbonise the concrete industry, contributing towards more standardised and accessible use of waste material within concrete.
Cardiff University is also leading an industry-focused project to decarbonise the concrete industry through waste valorisation, with companies involved in foundry and cast metal (Weir Group Plc), waste and carbon utilisation (Carbon Upcycling Technologies), and civil engineering (Knights Brown).
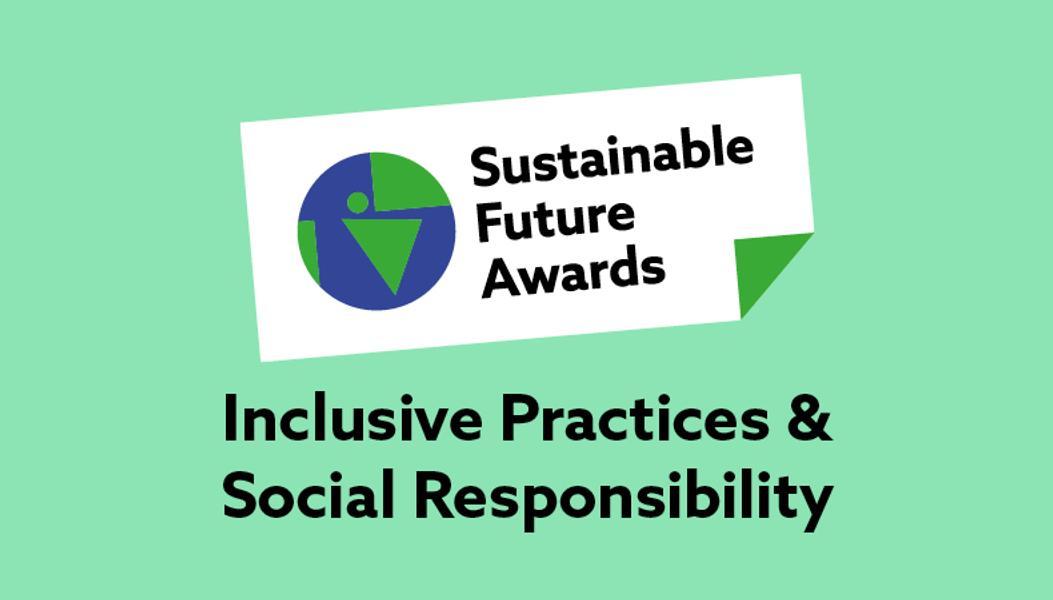
Inclusive Practices & Social Responsibility
Johnson Matthey Global Diversity, Inclusion & Belonging
Johnson Matthey fosters an inclusive environment by supporting nine Employee Resource Groups (ERG), a global network of Diversity, Inclusion & Belonging (DI&B) Ambassadors, and integration of its DI&B Roadmap into its sustainability strategy.
With the backing of senior leaders across the business, the commitment to DI&B can be seen through the involvement in multiple external talent programmes, ERG-led charity donations to support the wider community, and intersectional global events focused on creating a space where employees are free to be themselves at work.
IOM3 is guided by its commitment to the 17 United Nations Sustainable Development Goals (UN SDGs), to champion them to our members and stakeholders, and to operate by them throughout our organisation.
We understand that it is through the expertise that rests within our diversely qualified membership in science and engineering, that we will see progress in the journey to a sustainable, resource-efficient society.
As we encourage you to engage with this year’s shortlist, we also invite you to think about your role and contribution and consider applying to next year’s awards with research projects, campaigns and initiatives of your own.