Industrial heat cells store renewable energy
Demonstrator industrial-scale heat cells made from volcanic rock and scrap aluminium are to be built in Southampton, UK, by energy firm Caldera.
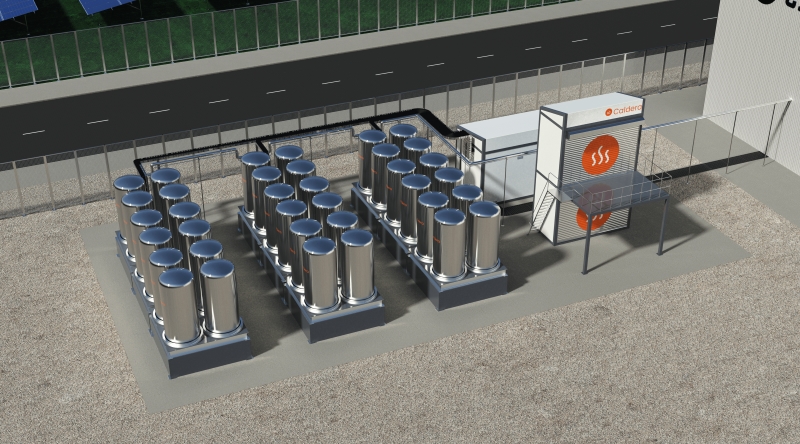
This is following an award of £4.3mln as part of the UK Government’s Industrial Fuel Switching Competition.
The technology aims to store renewable energy to provide industrial heat on demand. At the centre of the system is an array of heat cells. Each cell houses a solid core that ranges in temperature from 200-5000C, and is encased in vacuum insulation.
The company is working with the Manufacturing Technology Centre, part of the Advanced Manufacturing Catapult, to enable scaled production.
Though the exact manufacturing process is confidential, they note the recycled aluminium is melted and set over volcanic rock. Compared to other thermal energy storage technologies, Daniel Kirk, Chief Commercial Officer at Caldera reports, 'Our energy storage material…balances cost, conductivity and the ability to cope with thermal stresses.
'Conductivity in particular is important because it allows energy to be quickly put into and removed from the store. Solid aluminium has high conductivity but is expensive. Replacing most of the aluminium with rock reduces the cost significantly, yet the conductivity remains high as there is still a contiguous path for heat to travel through the aluminium.'
This thermal material 'took years of research from our thermodynamics experts and test engineers, building test rigs and trying different combinations of materials until we got it just right', says Kirk.
The vacuum insulation system, meanwhile, 'achieves vacuum performance affordably that is usually only possible at a very high cost'. This is because Caldera uses steam for thermal energy extraction, while some alternative thermal energy storage technologies use hot air.
Kirk explains, 'An air-based heat transfer system will have as much as 100x the insulation and 10x the thermal losses per metre of a steam system. If the piping requires solid insulation, the pipes will be heavy – the insulation alone will weigh 6t/m of paired pipe, run at 6.5MW heat flow. This means additional foundations for pipes, pipe supports and expansion joints, etc.'
A feasibility study estimates that the Caldera’s Storage Boiler can produce, '180°C/10bar steam, making them suitable to fuel switch 8% of global industrial heat demand'.
'Manufacturing processes will also be researched and optimised to minimise costs of production, installation, running and maintenance, with the aim of demonstrating how to switch industry to low-carbon fuels at an affordable price. Even with only a 5% share of the market, Caldera estimates global carbon savings of 197MtCO₂e by 2050,' shares Kirk.
Although energy density compares 'excellently' to most other options, fossil fuels remain denser, the firm acknowledges.
Kirk says, 'The good business case is almost always on sites that have space for a large ground-mounted solar array. That often means renting a field from a nearby farm and running ‘private wire’ connection up to a kilometre. Compared to the solar array, the Caldera thermal energy storage system, which is the size of a few shipping containers, is small.
'We plan to offer complete systems including solar panels and energy storage to provide 24/7 process heat from solar.'
He continues, 'The first version iteration will go live at the end of this year. As a demonstrator, it will heat a 15,000L hot water tank to prove it works well. It is based around heat cells that each store 100kWh of energy. Subsequent versions will use our next generation 200kWh heat cells and provide steam on demand. It’s about proving our technology works at the scale industrial customers need.'