Immobilising the UK’s plutonium stockpile
By transforming plutonium waste into a glass-ceramic material, it could be safe for geological disposal in the UK.
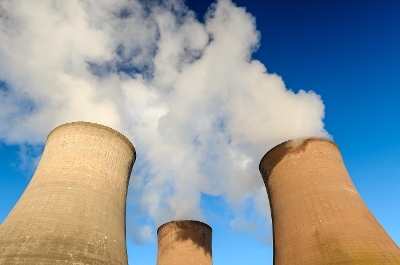
A Hot Isostatic Pressing (HIP) process has been shown to immobilise around 4.5t of contaminated plutonium residues at the University of Sheffield, UK. Converting the waste into a stable glass-ceramic material offers a safe and effective approach for creating an end-product that is suitable for geological disposal, say the scientists.
‘The glass-ceramic material is an effective solution for the more problematic proportion of the plutonium inventory which is heavily contaminated from degradation of the PVC packaging,’ says Professor Neil C. Hyatt, of the University’s Energy Institute and Department of Materials Science and Engineering. ‘It produces a stable glass-ceramic product which is durable and resistant to radiation damage.’
The team used the HIP process, which is being explored by the UK’s Nuclear Decommissioning Authority (NDA) with the US Department of Energy. Part sponsored by the NDA through a PhD studentship, the researchers at Sheffield have managed to incorporate the plutonium within a ceramic material and dissolve the chlorine contaminant within the glass phase.
‘We know from mineral counterparts of the ceramic phase, zirconolite, that this material will retain actinides like plutonium and remain stable to radiation damage, over the 240,000 years required in the disposal environment,’ Hyatt notes.
‘This work demonstrates that the glass-ceramic material would be suitable for treating heavily contaminated plutonium which may not be suitable for reuse, by showing that the chlorine contaminant can be managed without need for blending of plutonium feeds or needing a pre-treatment process to remove it,’ he adds. ‘It therefore contributes to the underpinning knowledge required to develop a treatment process to safely immobilise and dispose of this challenging material.’
When a geological disposal facility is available, the end product – a solid monolith with microscopic ceramic crystallites encapsulated in a glass matrix – can be emplaced in tunnels several hundred metres underground in a stable geological environment, within a corrosion resistant container and surrounded by a clay buffer. ‘This multibarrier approach will ensure the safety of the disposal system and retention of the plutonium over the required timescale,’ Hyatt adds.
The extremely bright X-ray microscope at the European Synchrotron Radiation Facility, France, was used to develop an atomic-scale model to determine the solubility of chlorine in the glass-ceramic.
‘We could then show that, even with very conservative worst-case assumptions, the chlorine concentration would be below the glass solubility limit preventing the possible formation of a soluble plutonium chloride salt,’ says Hyatt.
He explains that the next step is to develop a small-scale process line to demonstrate the application of HIP, which is being led by the UK National Nuclear Laboratory. ‘This will enable the process to be optimised and develop the skills and expertise necessary to develop a production scale facility.’